Boiler unit needed to produce consistent steam for reliable temperature modulation, and steam on-demand.
The Silvestri family has been in the renewable energy business for 14 years.
Their family-owned and operated business in Ontario, Canada —SILTRI Bio Fuels Inc. — has spent the last decade and a half contrib- uting to the global renewable energy market by aiding in the conversion of recycled vegetable oil into environmentally-friendly Biodiesel fuels.
A large component of SILTRI’s on-the- ground operation involves the refine- ment process, where the oil is filtered for contaminants before being shipped to the Biodiesel plant. As Joe Silvestri, the owner of SILTRI, explained, “We bring in used cooking oil from restau- rants and food manufacturing facilities, filter out the unwanted impurities and moisture, then send the refined product to Biodiesel plants in North America and overseas.”
This refinement process involves multiple stages, most of which require a consistent high level of heat. Temperature plays a critical role in this opera- tion and is key in produc- ing a high-quality product meeting specs.
THE PROBLEMS
Before they launched their new business, the Silvestri family knew it was important they find the right equipment to reliably provide them with the requisite heat output For this, they looked to steam boilers. The trouble was finding the right one.
Joe Silvestri was well-aware that their business, and thus livelihood, depended on the continuous operation of the boiler. If it went down, so too would their operation. He also knew that he needed a boiler that could produce consistent steam for reliable temperature modulation, and prefera- bly, steam on-demand. And, as a company with an eye to a greener future, it was imperative that the equipment they used was energy-efficient.
Initially, Joe was looking at fire tube boilers. Yet, Joe was concerned about the large amount of water required to operate them. The large amount of operating water content in a firetube design meant a greater risk of explo-sion (and the more inefficient and time-consuming it is to convert water into steam).
Even further, as per Canada’s regula- tions, any boiler (not classified as low water volume) exceeding 50 BHP needs to have a certified operating engineer to oversee it. Otherwise, the risk of an explosion is too great. And SILTRI’s production was going to require more than 50 BHP. As a fami- ly-run business just starting off, adding another person to payroll was not opportune.
SOLUTION
It was through word of mouth that Joe was first introduced to Clayton Indus- tries steam generators. As Ron Polidori, Clayton’s sales manager shared: “An old Clayton customer was closing their doors and was selling their used E-154 BHP steam generator.” Joe heard about the used unit and started comparing the Clayton steam generator to the fire tube boilers he’d been looking at.
Unlike traditional boilers, Clayton’s unique counterflow design and controlled circulation system technology necessitates the use of only a small amount of water at a time. For Joe, that meant the steam generator would be able to to offer more rapid start-up and follow load cycles, as well as ensure the absence of explosion hazards. And owing to these safety assurances, SILTRI wouldn’t have to invest in a stationary engineer — no matter the boiler horsepower.
As Joe stated, “it was immediately clear that the Clayton steam generator was the most reliable choice.” SILTRI purchased the used Clayton steam generator, kick-starting their business in the renewable energy industry.
RESULTS
For 14 years, the steam generator has been a crucial player in SILTRI’s growing business. The team runs the boiler non-stop whenever they are process- ing, which is most days. Even with this continuous usage, the boiler’s-con- trolled circulation design allows them to cut down on fuel and maintain relatively low energy costs.
Moreover, as Joe stated, “set-up in the morning is easy with the boiler, which is important for our team. To make 150 HP of steam — it’s almost instant. No lag-time at all.” Even when another tank of unheated raw material is introduced to the reactor, the steam generator can immediately compen- sate for the new load.
For Joe, an unexpected but crucial benefit of the Clayton steam generator has been its serviceability. As Joe shared, “the Clayton steam generator is the only piece of equipment I haven’t had to worry about.”
Joe continued, “Clayton always has the parts and knows what to do. Whatever the issue is, they’ll fix it, no problem.
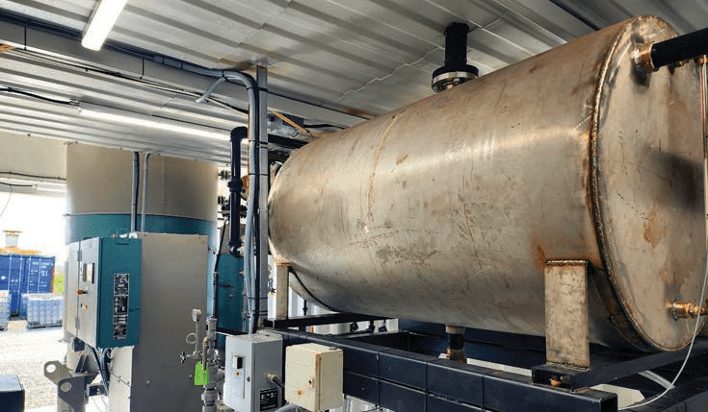
I would rather pay for a Clayton steam generator than take a free boiler from another manufacturer, simply for the reliability of the product and excellent customer support. Clayton’s service is unreal! What they do, no one else does, and I have experienced it first- hand. It’s one of the most important pieces of equipment in our plant, and it’s worry-free!”
RENEWED INVESTMENT
Although the steam generator is still going strong, Joe knew that it wouldn’t last forever. As Ron stated, “SILTRI bought the steam generator used, and with the added 14 years of operation, it was reaching the end of its useful life.”
Moreover, business was expanding, and demand was greater. It was time to upgrade their equipment. For Joe, there was no question of where to turn for
their new steam generator. “Because I was 150% satisfied with our old steam generator, I called Clayton.” This time, Joe was ready to move up. With an eye to his evolving company needs, Joe was ready to invest in a steam gener- ator with better efficiency, greater horsepower, up-to-date controls, and a full warranty. SILTRI purchased their Clayton E-254 250 BHP steam generator with the added economizer last year, and it has proven to be another worthwhile investment. With the improved PLC based controls, increase of 100 BHP, and higher fuel efficiency, this new steam generator has only brought more ease and efficiency to their operation. As Joe said, “The steam gener- ator pays for itself.” Yet, with their 150 BHP still going strong, Joe is not yet ready to give up his initial steam generator, which has been with him since the company’s inception. Instead, Joe is using the old steam generator for backup.
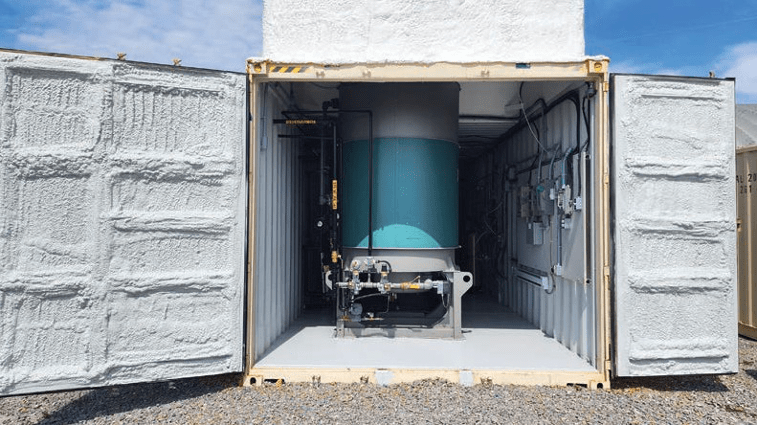