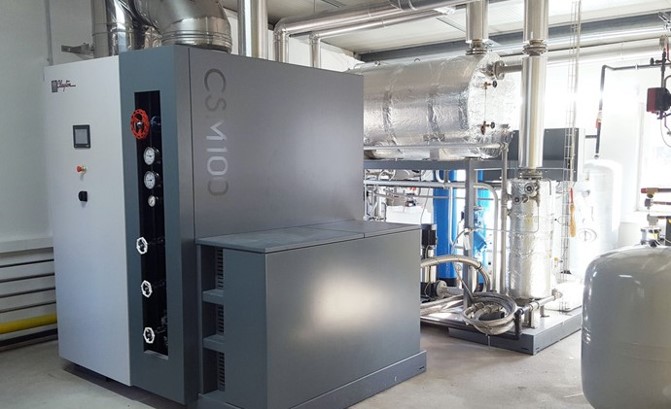
A Clayton Steam Generator has been in use at the Austrian based cleaning company Proxima GmbH (Fürnitz) for several months, and already provides 70 percent of the hot steam required for the entire washing process.
Austria-based Proxima GmbH has only been in the textile cleaning business for two years. The relatively young company, which Managing Director Heinz Haberl describes as a “comparatively small laundry business” with a target daily laundry volume of 20 tons, has established itself successfully on the market, thanks to careful selection of its customers and high-quality standards.
Haberl himself looks back on 25 years of experience in the industry and is familiar with the problems that textile cleaning companies often face: “The level of the industry standard prices per kilogram washed has been dropping progressively over the last 10 – 15 years, which plays a major role, especially when it comes to acquiring new customers. From the outset, Proxima had an agreement with the operator of about 30 retirement homes, whose textile cleaning we were allowed to take care of, from rental laundry, in the form of towels, to residents’ laundry, which corresponds to about 6,000 items per day.”
Another important aspect for Proxima are its customers from the high-end hospitality industry. Here, in line with the company’s claim, emphasis is placed on quality, allowing more economical prices to be realized. Half of the total turnover comes from customers within the city and seasonal hotel industry, although at the present time retirement homes still account for a large proportion of Proxima’s clienteles – a ratio that the managing director believes will be reversed in the future.
“Proxima, with its quality and price awareness, is steering against the prevailing industry trend in many respects. Especially when it comes to customer selection, we look very closely at who suits us in terms of distance, logistics and production sequence. Our manageable company size is sometimes even an advantage here: since we can wash on a customer-specific basis, our customers are never supplied with external laundry from a single rental laundry pool of inevitably fluctuating textile quality and color intensity – a circumstance that is unavoidable in larger laundry operations with significantly higher laundry volumes”, says Managing Director Haberl.
Balancing Quality And Efficiency
Proxima puts in a great deal of effort to successfully achieve the balance between quality and cost efficiency. Starting with the costs for the use of textile in the lingerie rental business, which accounts for about 90% of orders, and often requires the textile cleaning company to make advance payments in the millions. In addition, there is the close cooperation with the detergent suppliers, which is just as time consuming and cost intensive. These practices also require weekly inspections by chemists, as well as elaborate quarterly checks carried out for detergent residues, acidity, and bleaching levels. Considering the industry standard personnel costs of 45 to 48%, then it becomes unfeasible for the company managers to also consider technical process optimization.
The actual cleaning process extends over a 15-meter-long washing tube. In 15 chambers, all the necessary processes from prewash to main wash, post-wash and rinsing take place step by step. Every 2 minutes, the laundry enters the next chamber, while 60 kg of clean laundry continuously leave the machine at the same interval.
For several months now, a compact steam generator has been in use at the Austrian cleaning company, which now provides 70% of the superheated steam required for the overall washing process. The company opted for a high- speed steam generator from Clayton Germany, the Steam Master CSMG100 – which came equipped with an 800-liter water module, stainless steel tank and integrated chemical dosing, delivering 1.5 tons of steam per hour.
“At the beginning, a relatively small steam boiler was the appropriate solution for us. On one hand, the investment and operating costs were manageable, and on the other hand, the steam generator only supplied part of the equipment for the time being, so as not to be completely dependent on steam operation during the trial phase”, explains Heinz Haberl. “Due to the nature of the industry, we cannot make any compromises when it comes to reliability, because as a service provider we are committed to our customers through fixed delivery agreements. From the delivery of dirty laundry to sorting, washing, ironing, drying, and dispatching, we have no leeway in terms of time. Since bridging with new laundry in the event of bottlenecks is out of the question because of the costs and logistics involved, we are very cautiously approaching new possibilities here.”
At Proxima, the Steam Master CSMG100 operates a gas fueled configuration, as do some of the autonomous systems that are also available. These include, for example, the iron responsible for the smoothing process, which Haberl says is one of the “core components” of the laundry operation. The performance and user-friendly nature of the generator has been a welcome addition to the Fürnitz operation.