Automotive Industry
Home > Industries > Automotive
Clayton Industries supports the Automotive Industry
You could argue that the automotive industry began on January 29, 1886, when Carl Benz applied for a patent for his “vehicle powered by a gas engine”, patent number 37435, which is sometimes considered to be the “birth certificate” of the automobile.
From the oldest functioning car in the world, La Marquise, a steam-powered, four-wheeled, four-seat vehicle, manufactured by De Dion Bouton in France in 1884, Henry Ford’s Model T in 1908, and on to the supercars of today, automobiles have long held a special place in public fascination. While very few are steam powered, steam is still used extensively in the manufacturing process, starting in the mines that provide the raw material for your automobile.
Steam is used for Vulcanization for rubber products such as tires, bumpers, steering wheels or inside trim and wiring. Vulcanization improves elasticity, hardness, tear strength, and resistance to organic solvents and abrasion. It also offers excellent resilience, low water absorption, and oxidation resistance, as well as making an excellent electrical insulator. In tire manufacturing, green tires are placed in a steam press, or autoclave. This press is a hot pressurized mold using steam at a set pressure causing vulcanization, a chemical reaction which transforms the tire from a weak rubber to a strong elastic material, a process that requires a constant temperature throughout, ideally a source of dry saturated steam between 260 and 250 psi. Steam is an ideal medium for this process not only for its temperature regulation, but also as a way to prevent contaminants from fouling the process.
Steam is also used in the painting process as part of a phosphate bath. Phosphating is vital in ensuring a proper finish of powder coated or painted parts, as well as ensuring proper adhesion of paint, a better appearance, and corrosion protection for metal parts. The phosphate coating that developed in this application requires a constant high temperature. If the bath temperature dips too low, your finished products will have poor coverage, resulting in a messy appearance and leaving the metal open to corrosion.
To maintain a constant temperature and high-quality steam, look no further than Clayton Steam Generators to provide you with high quality steam at greatly reduced operating costs.
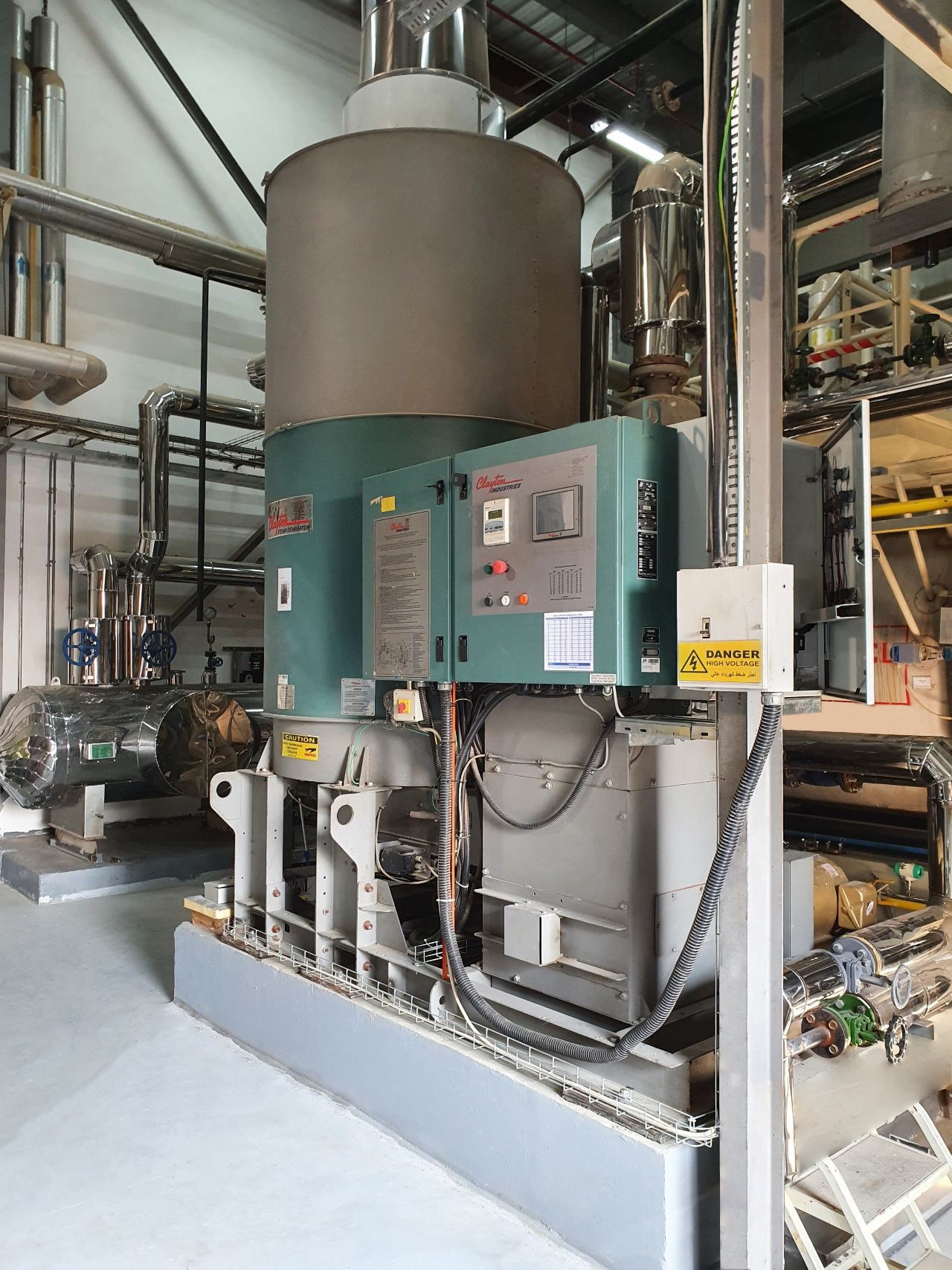
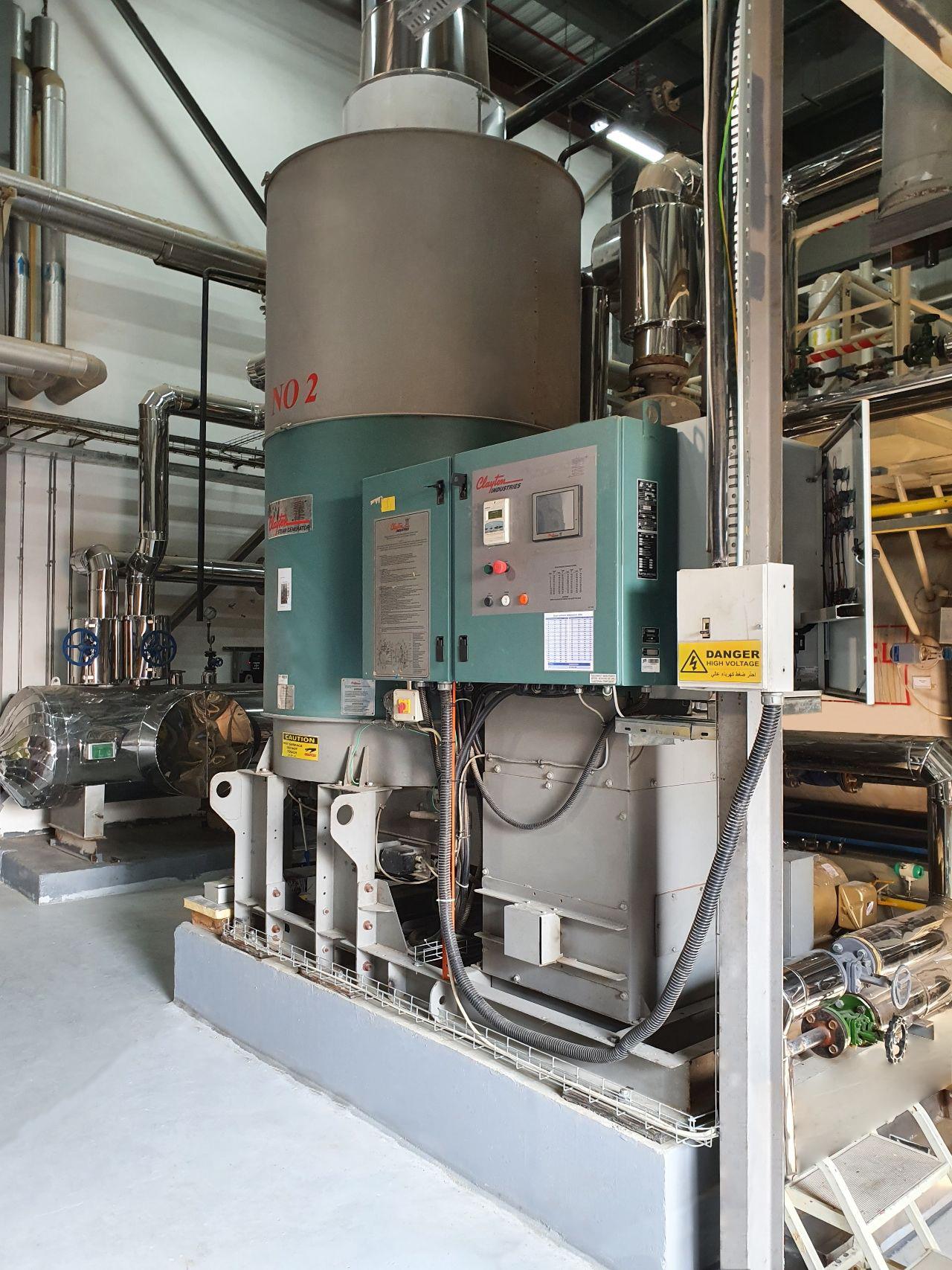
Clayton Industries supports the Automotive Industry
You could argue that the automotive industry began January 29, 1886, when Carl Benz applied for a patent for his “vehicle powered by a gas engine”, patent number 37435, which is sometimes considered to be the “birth certificate” of the automobile.
From the oldest functioning car in the world, La Marquise, a steam-powered, four-wheeled, four-seat vehicle, manufactured by De Dion Bouton in France in 1884, Henry Ford’s Model T in 1908, and on to the supercars of today, automobiles have long held a special place in public fascination. While very few are steam powered, steam is still used extensively in the manufacturing process, starting in the mines that provide the raw material for your automobile.
Steam is used for Vulcanization for rubber products such as tires, bumpers, steering wheels or inside trim and wiring. Vulcanization improves elasticity, hardness, tear strength, and resistance to organic solvents and abrasion. It also offers excellent resilience, low water absorption, and oxidation resistance, as well as making an excellent electrical insulator. In tire manufacturing, green tires are placed in a steam press, or autoclave. This press is a hot pressurized mold using steam at a set pressure causing vulcanization, a chemical reaction which transforms the tire from a weak rubber to a strong elastic material, a process that requires a constant temperature throughout, ideally a source of dry saturated steam between 260 and 250 psi. Steam is an ideal medium for this process not only for its temperature regulation, but also as a way to prevent contaminants from fouling the process.
Steam is also used in the painting process as part of a phosphate bath. Phosphating is vital in ensuring a proper finish of powder coated or painted parts, as well as ensuring proper adhesion of paint, a better appearance, and corrosion protection for metal parts. The phosphate coating that developed in this application requires a constant high temperature. If the bath temperature dips too low, your finished products will have poor coverage, resulting in a messy appearance and leaving the metal open to corrosion.
To maintain a constant temperature and high-quality steam, look no further than Clayton Steam Generators to provide you with high quality steam at greatly reduced operating costs.
Key Benefits
High Quality Steam
Clayton’s mechanical steam separator delivers consistent results, guaranteeing steam quality in excess of 99% dryness, ensuring no compromise on your product quality.
Compact Design
Clayton Steam Generators take up less than one third of the floor space of a traditional firetube boiler, leaving more space on your factory floor for your equipment and employees.
Lowest Cost of Ownership
Clayton’s high efficiency design is guaranteed to lower your fuel bills, with the savings our typically making up the cost of installation in the first few years of operation.
Key Benefits
High Quality Steam
Clayton’s mechanical steam separator delivers consistent results, guaranteeing steam quality in excess of 99% dryness, ensuring no compromise on your product quality.
Compact
Design
Clayton Steam Generators take up less than one third of the floor space of a traditional firetube boiler, leaving more space on your factory floor for your equipment and employees.
Lowest Cost of Ownership
Clayton’s high efficiency design is guaranteed to lower your fuel bills, with the savings our typically making up the cost of installation in the first few years of operation.
Featured Case Study
Top 10 Reasons To Buy a Clayton Steam Generator
1. FUEL EFFICIENT:
The Clayton design produces higher fuel-to-steam efficiency, even when operated lower than the full firing rate.
2. COMPACT SIZE:
Clayton Steam Generators require only 1/3 the floor space of traditional boilers.
3. FAST START-UP:
The Clayton Steam Generator can go from cold to full steam in less than 10 minutes.
4. QUALITY STEAM:
The fixed-vane steam separator yields the driest saturated steam available in the industry today — typically less then
0.5% at all loads.
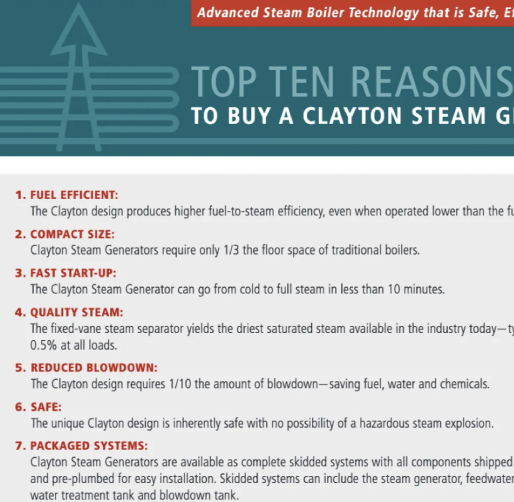
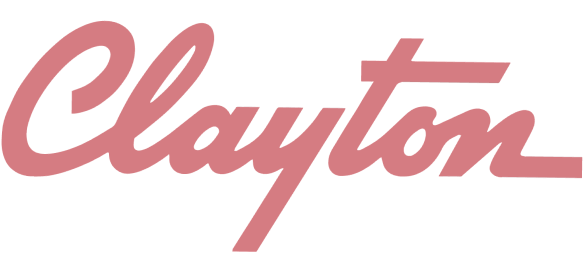
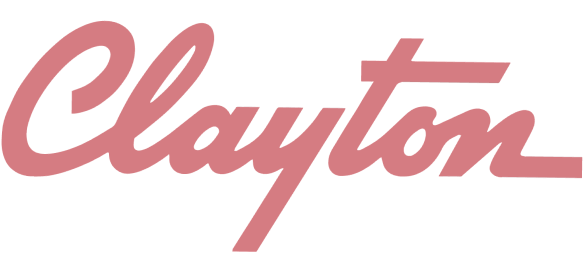
Contact a Clayton Representative

sales@claytonindustries.com

800 423 4585 or +1 626 435 1200 PST
Contact a Clayton Representative
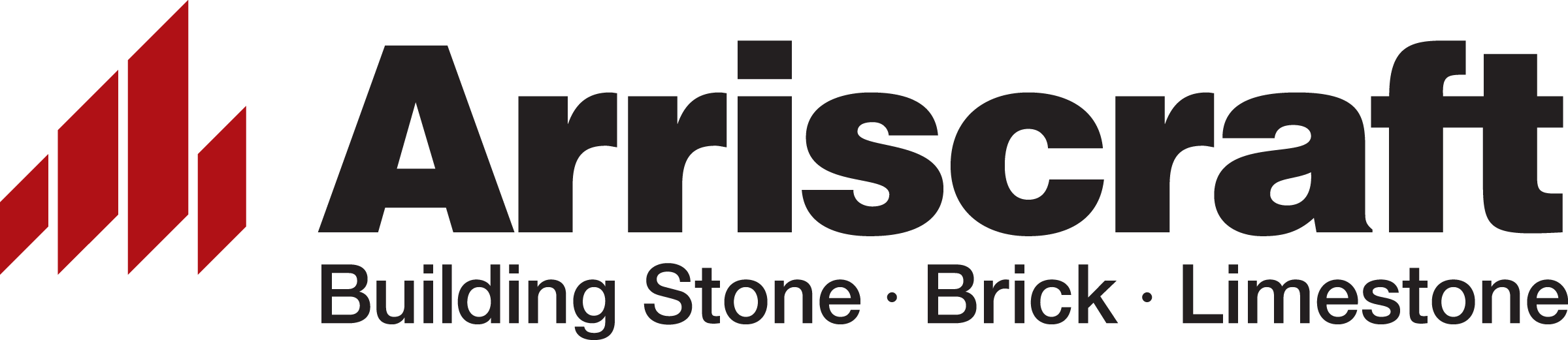

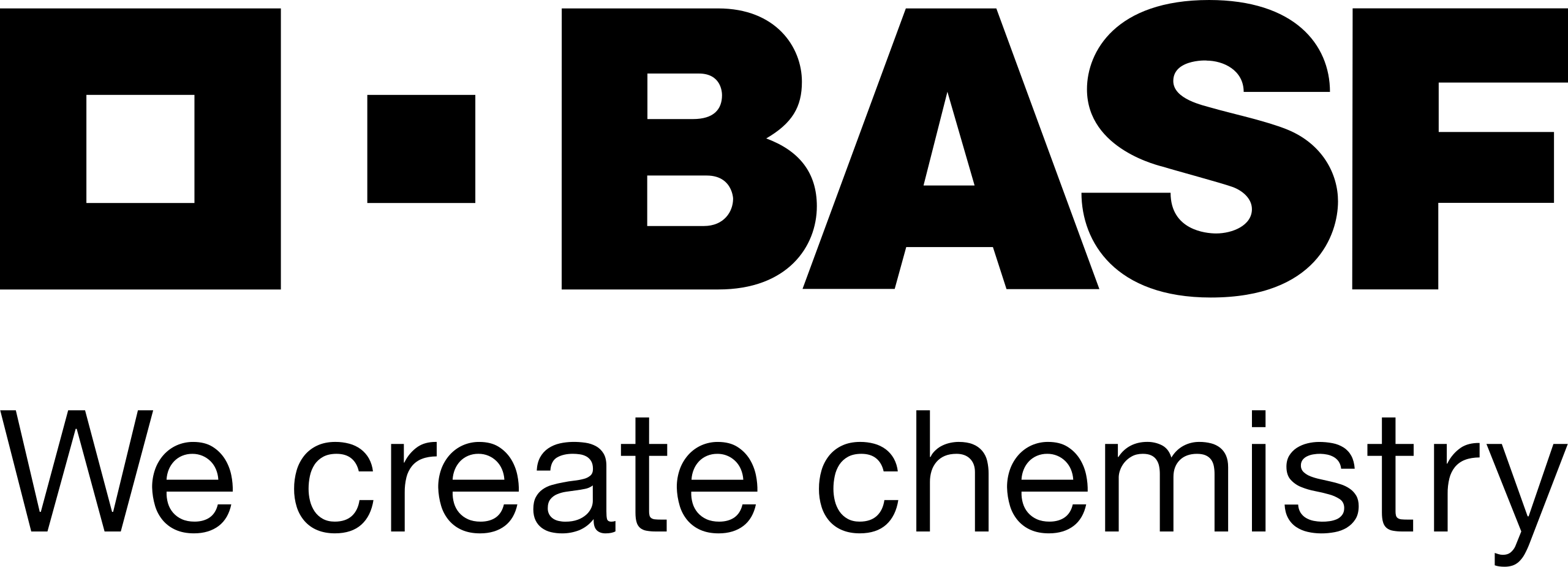
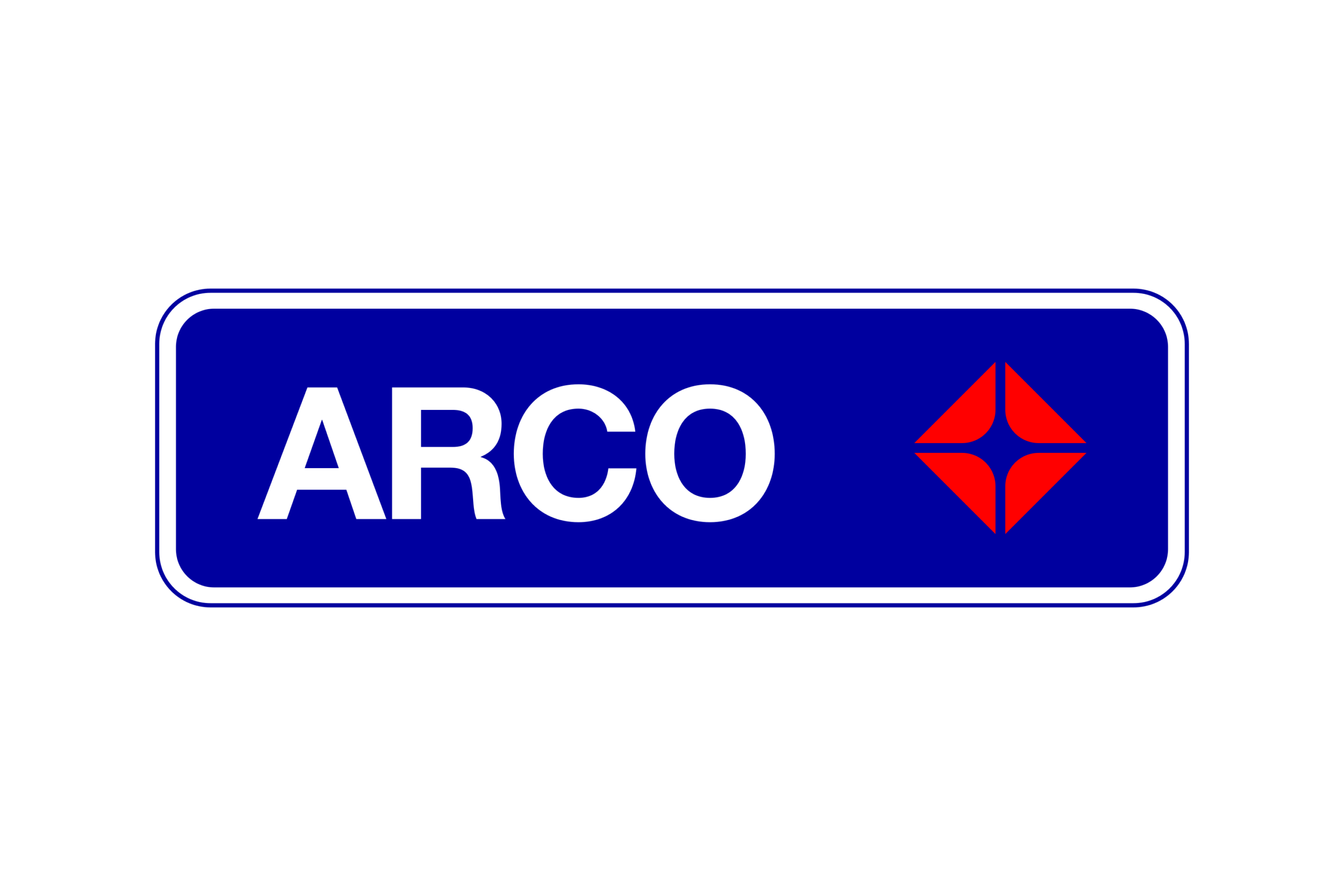
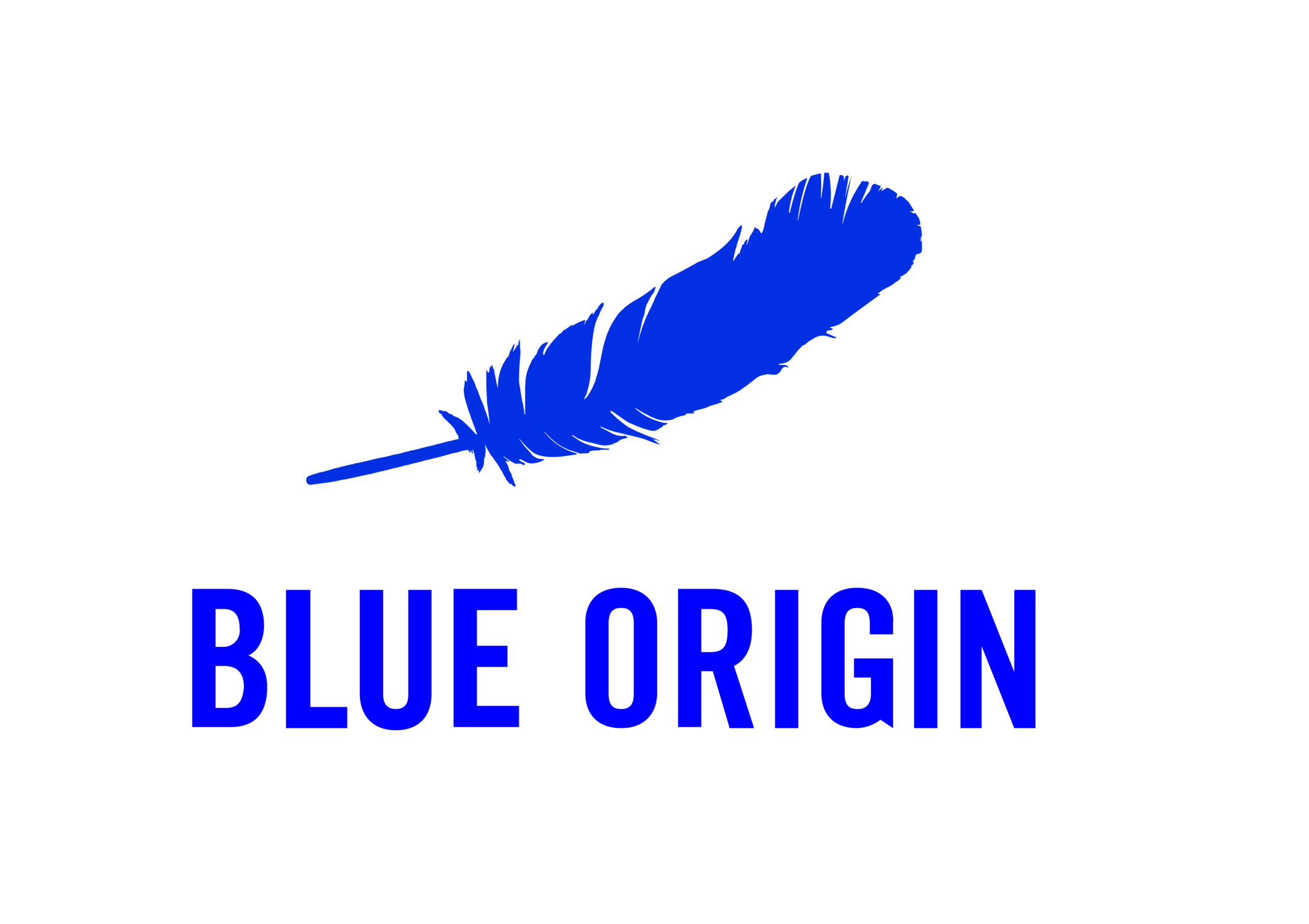
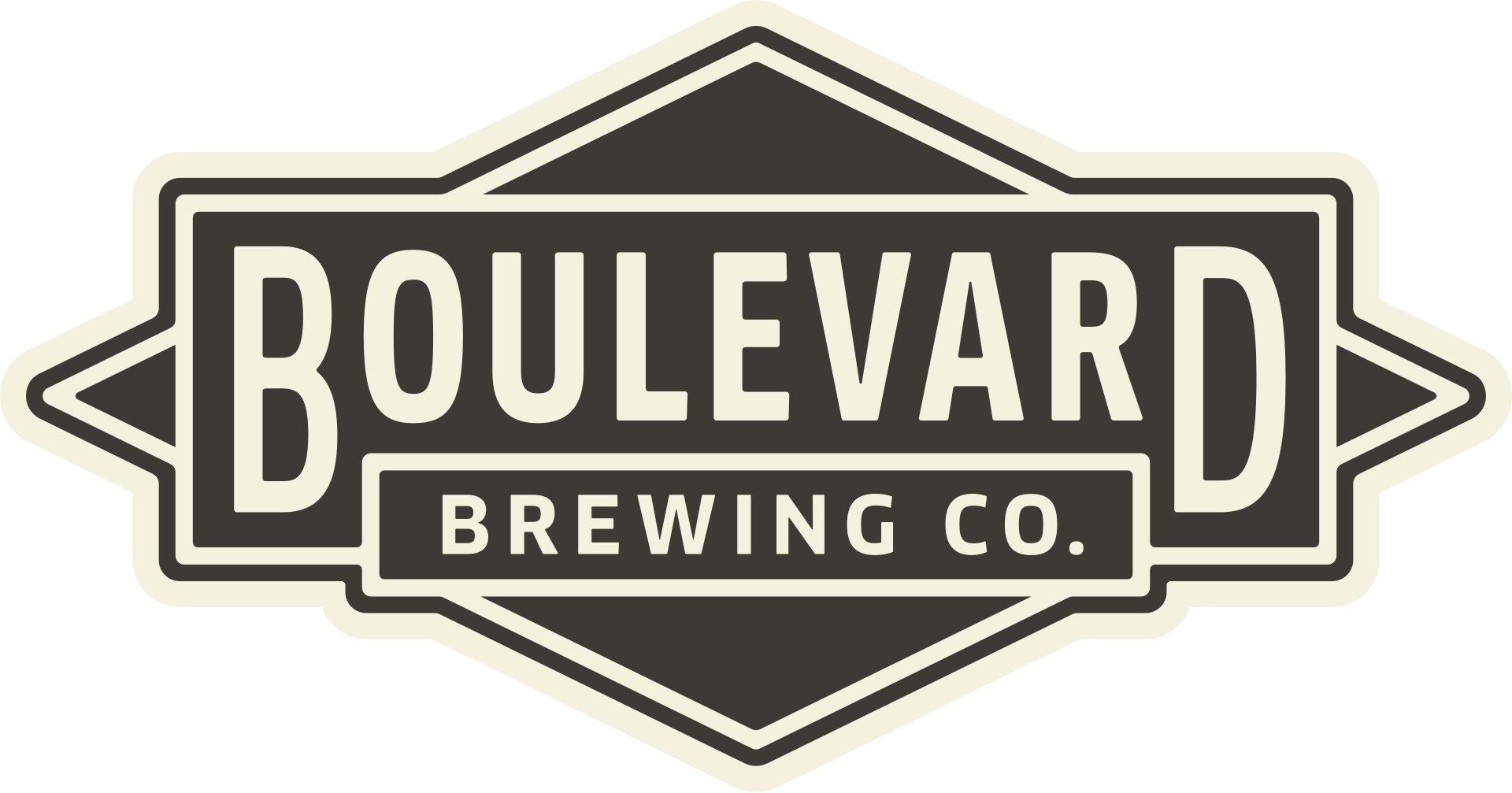
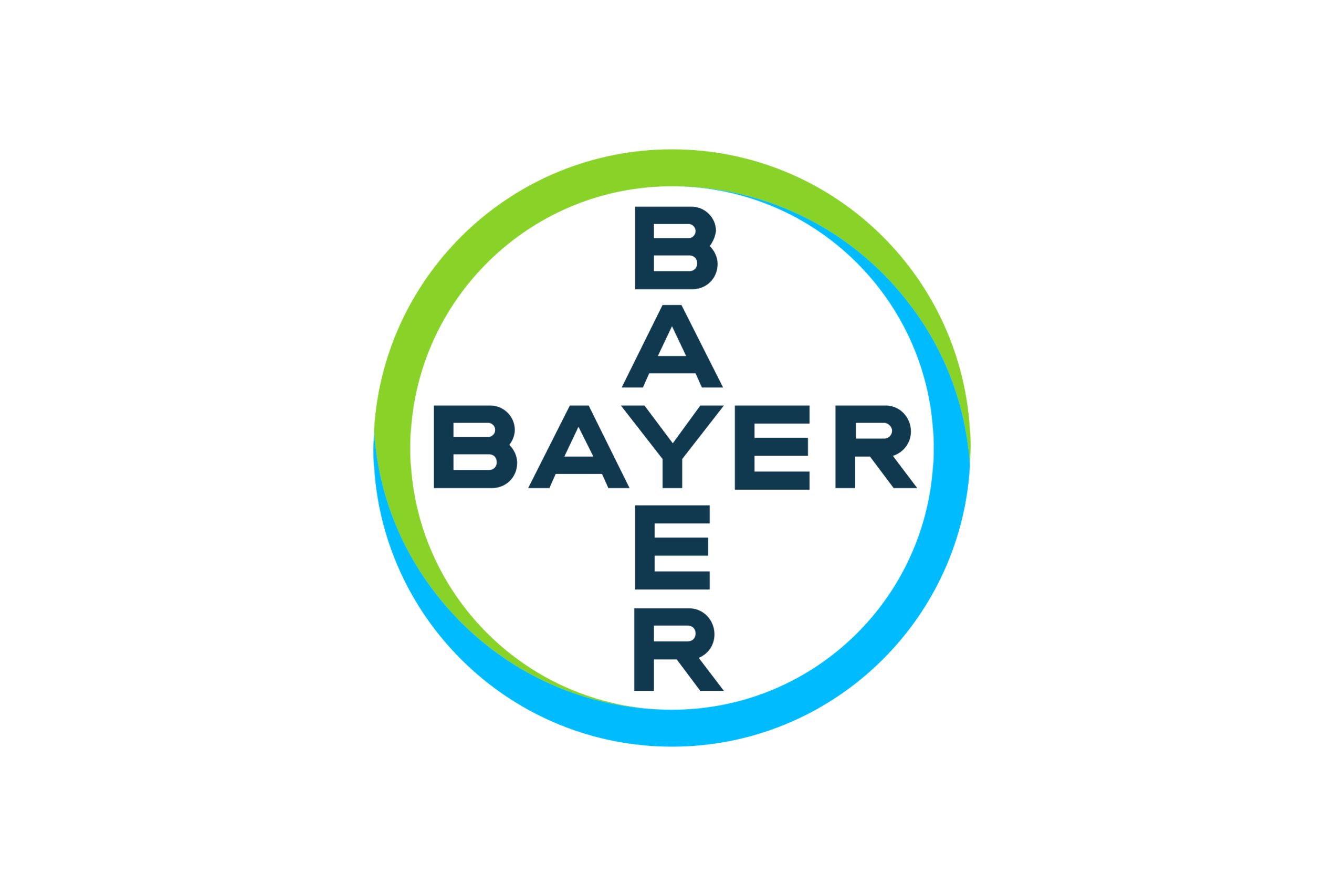
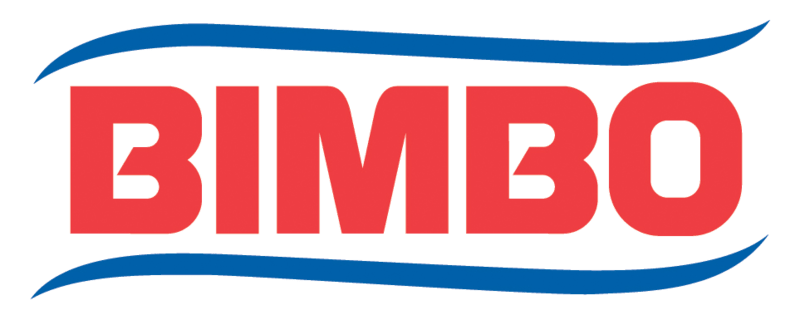
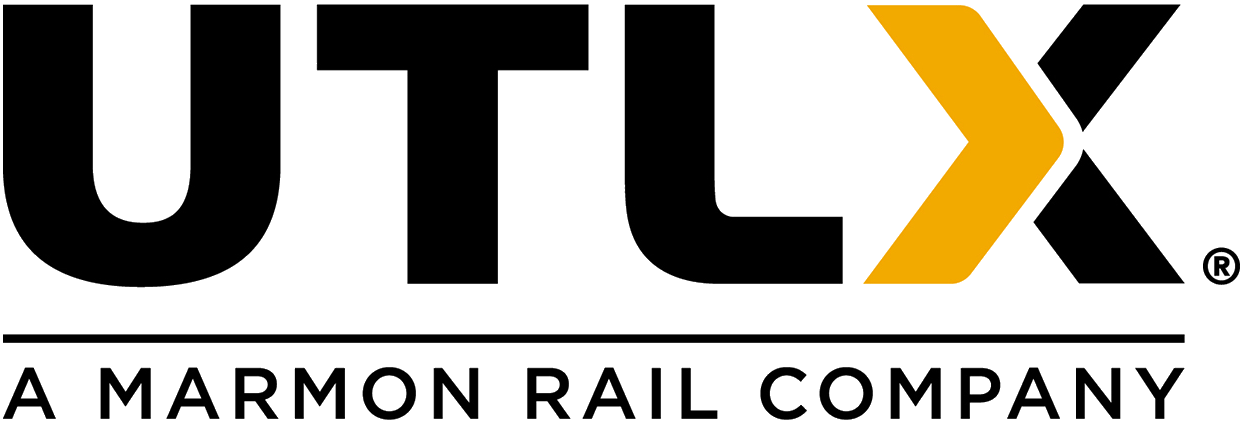
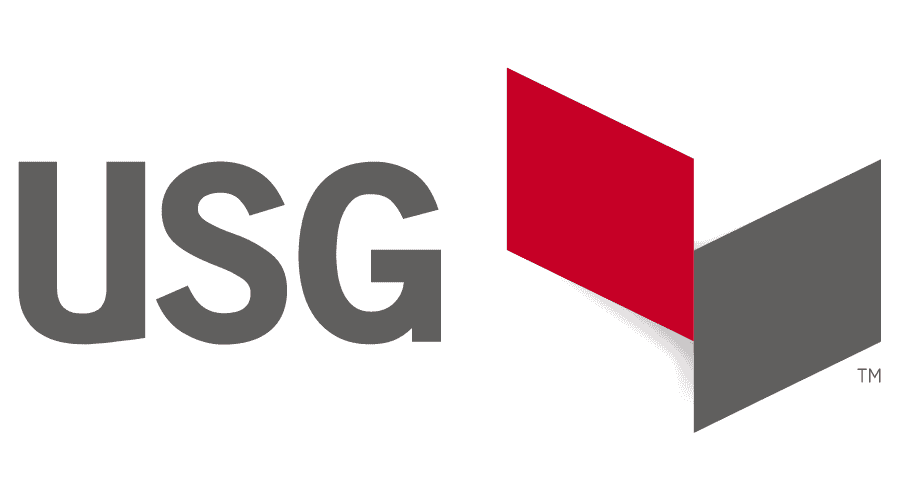
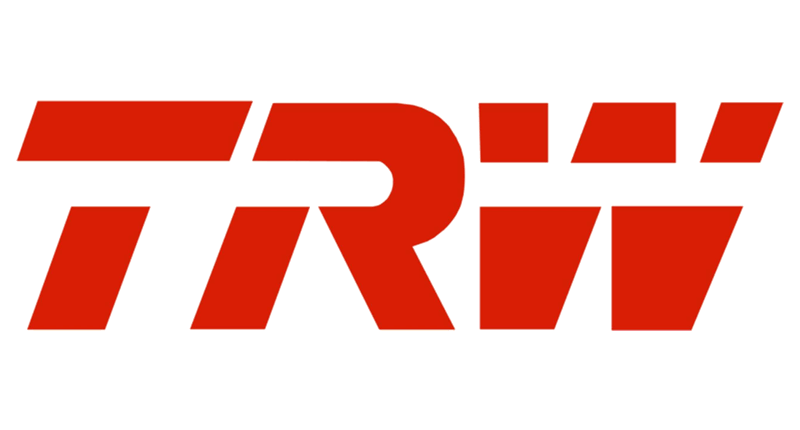
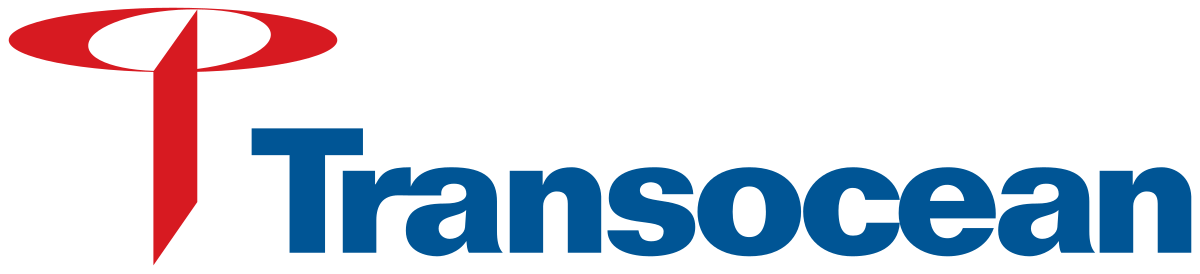

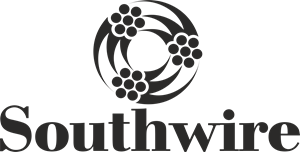
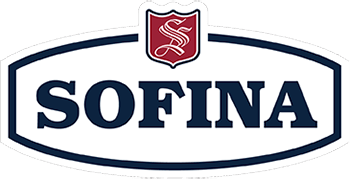
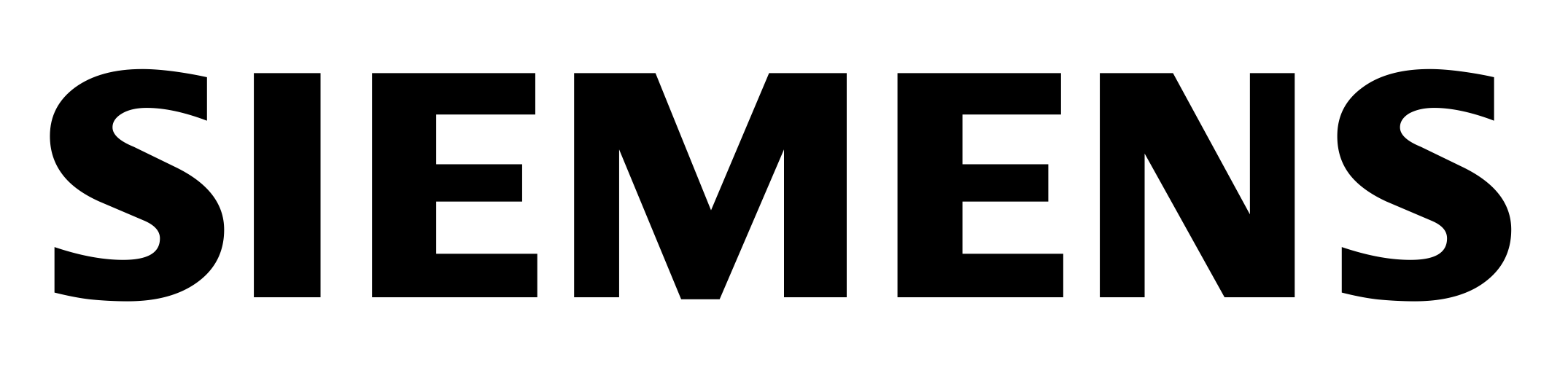
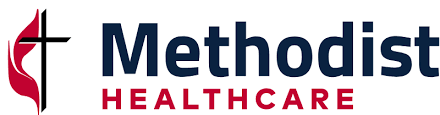
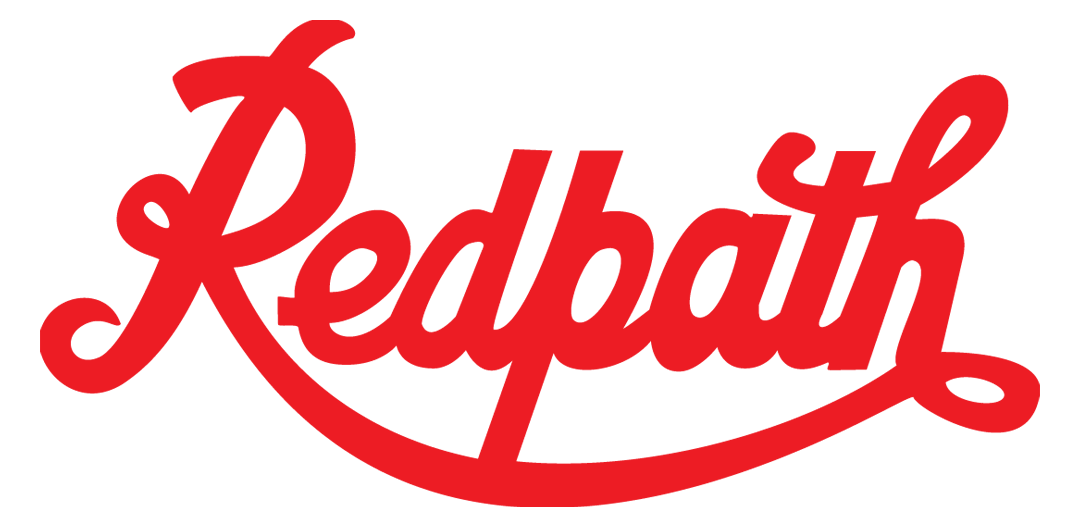
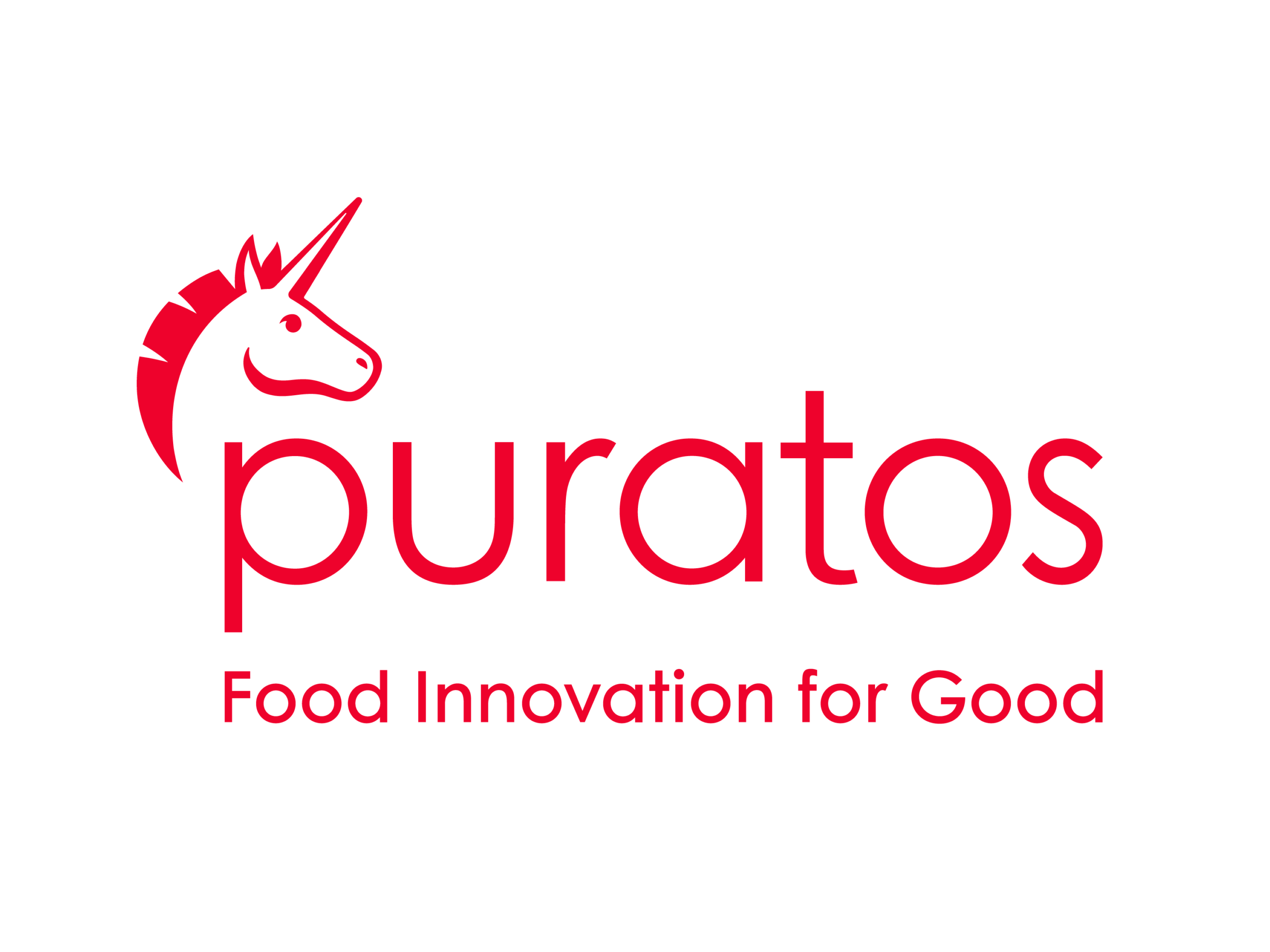
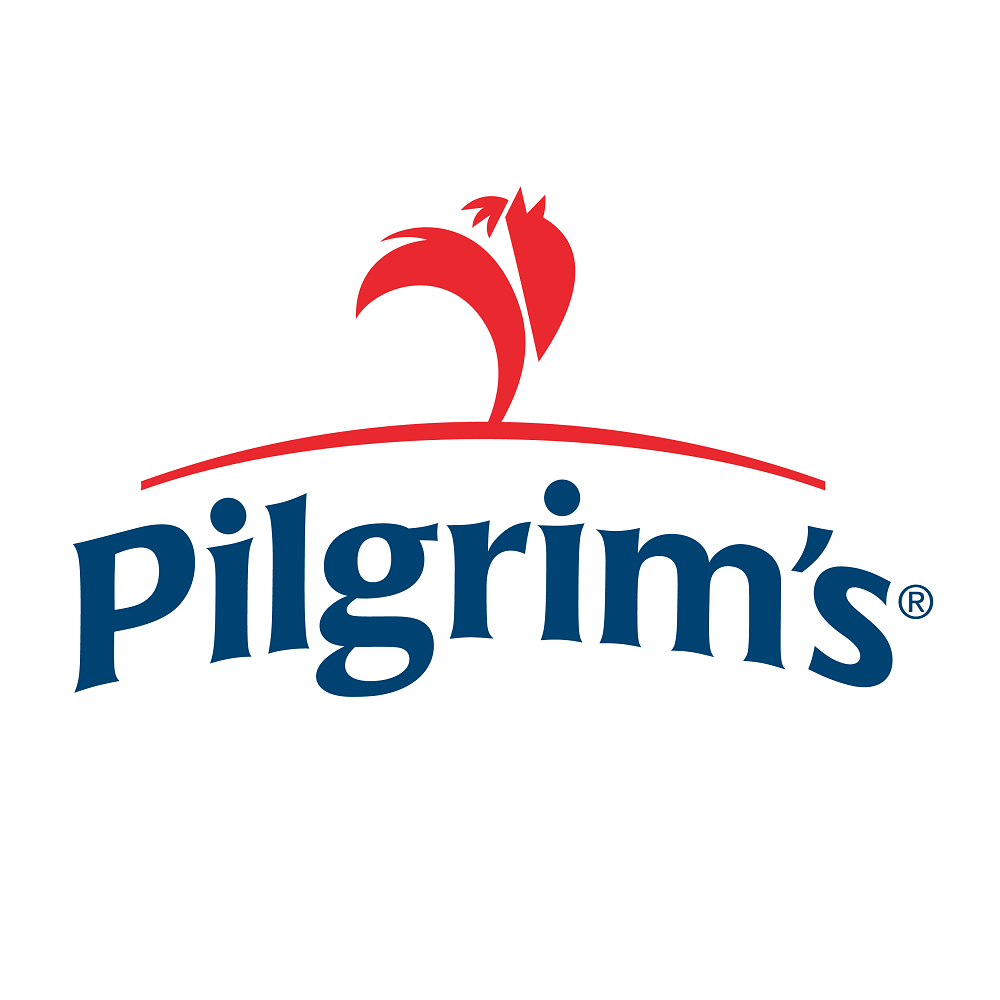
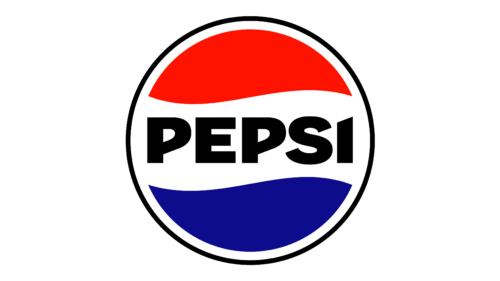
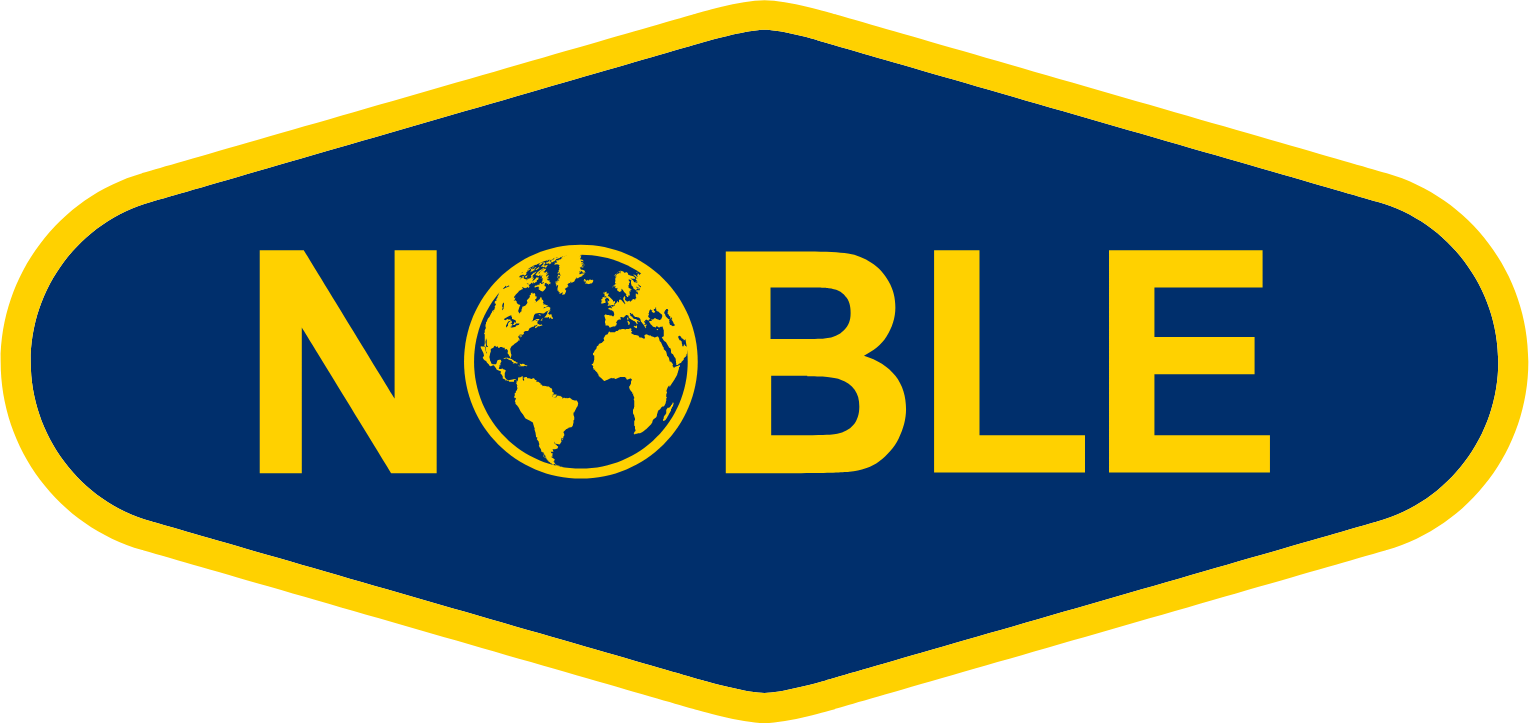
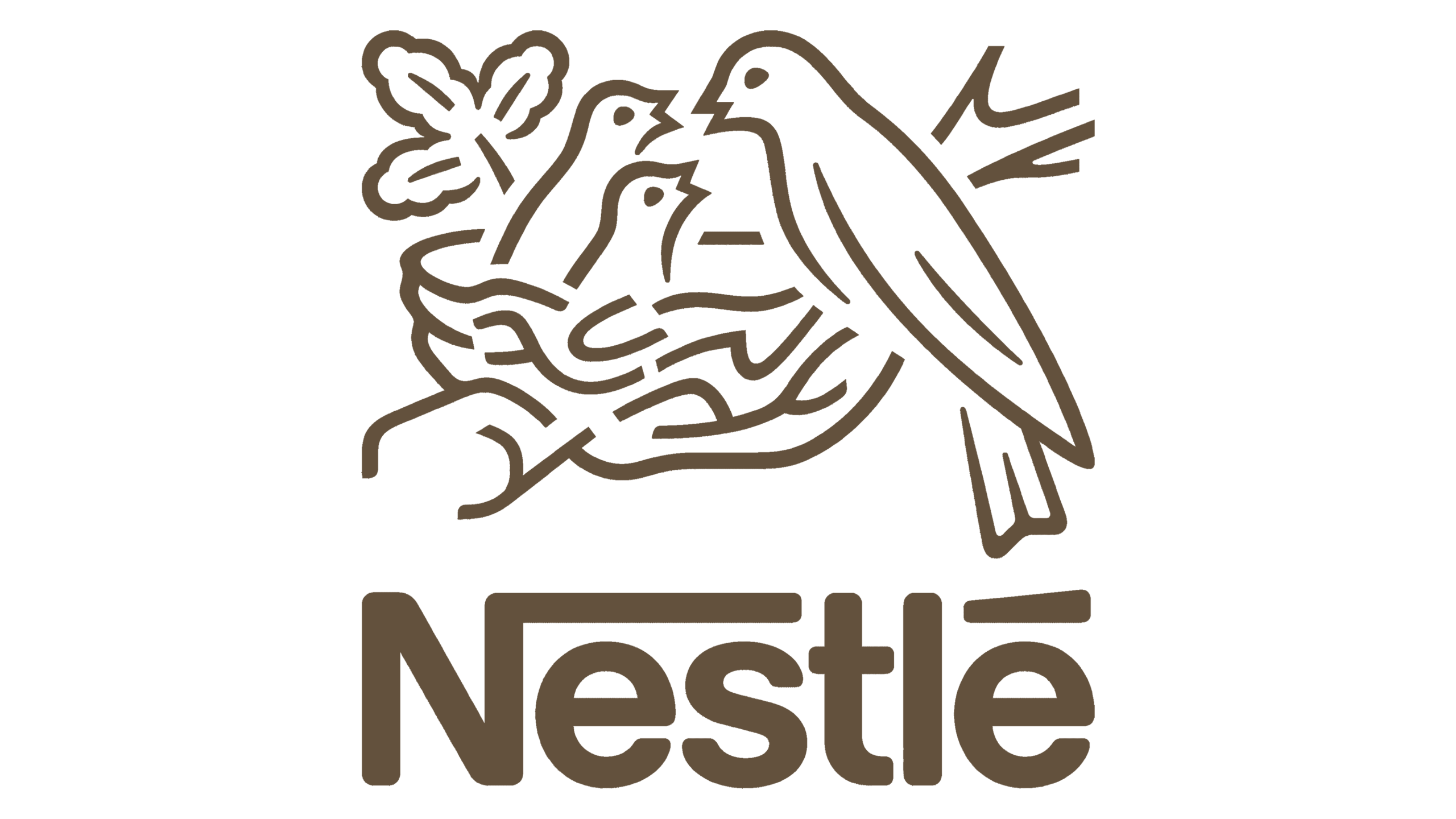
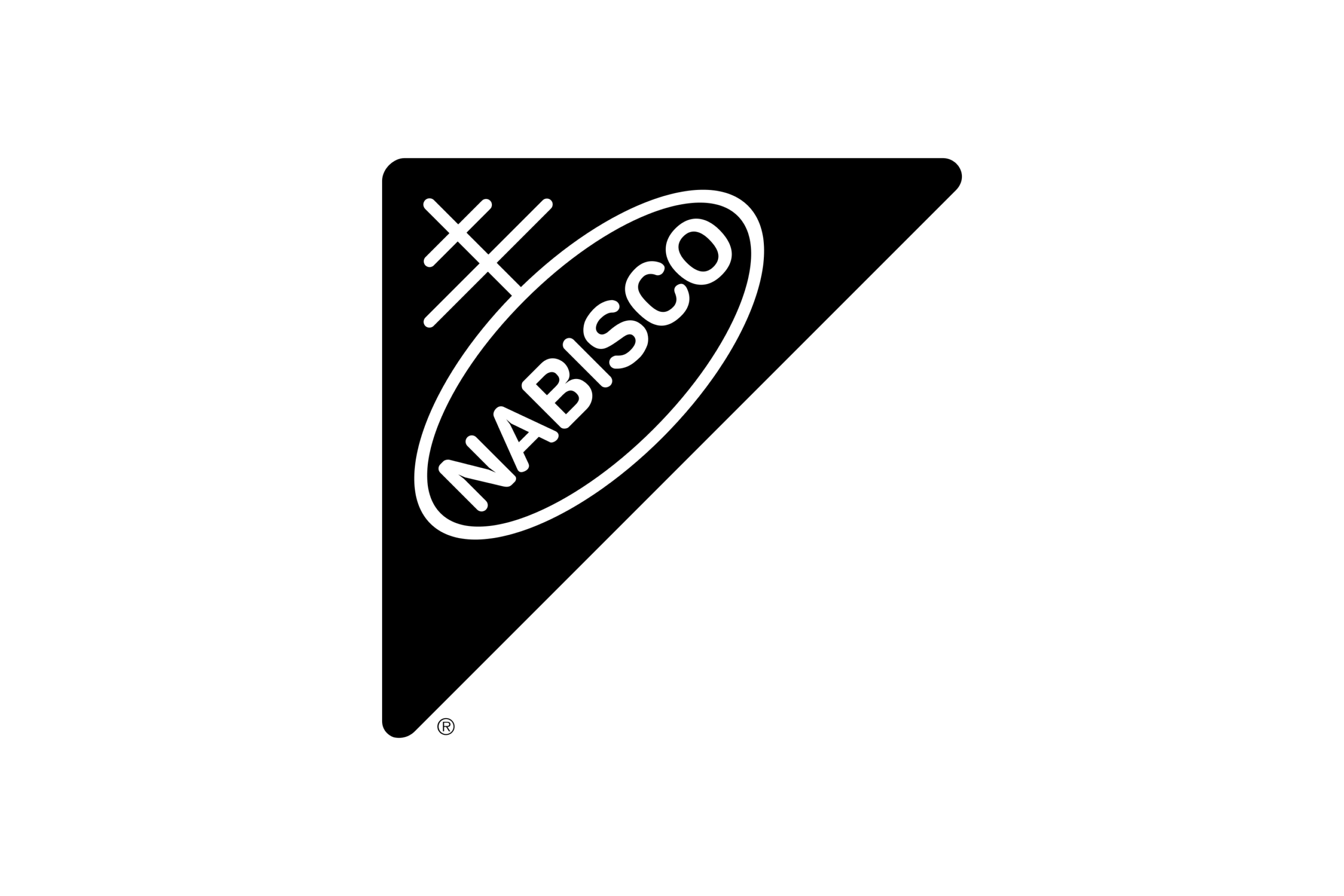
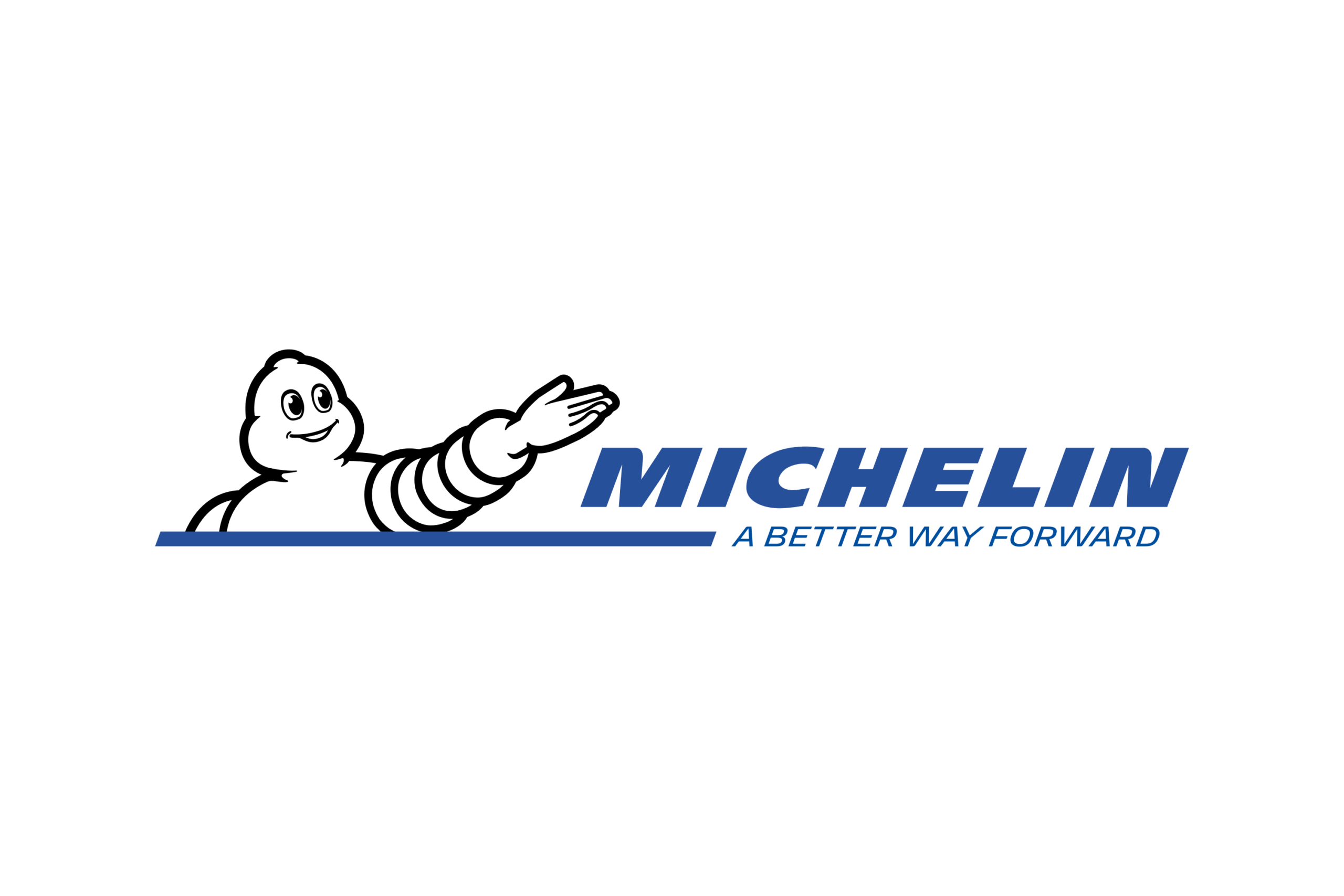
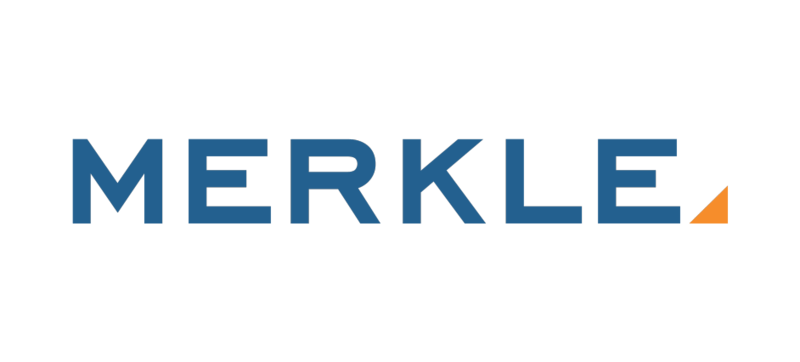

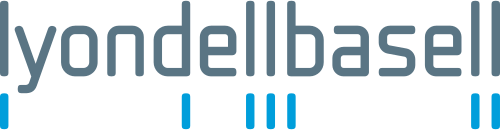
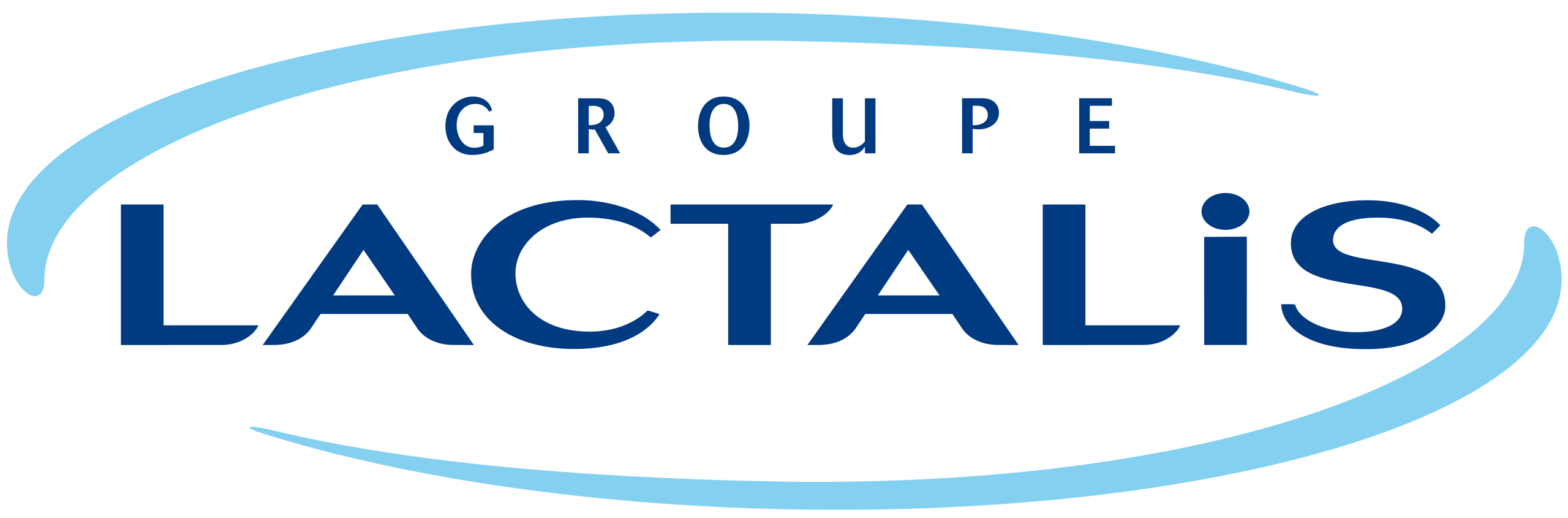
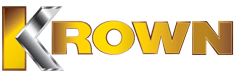
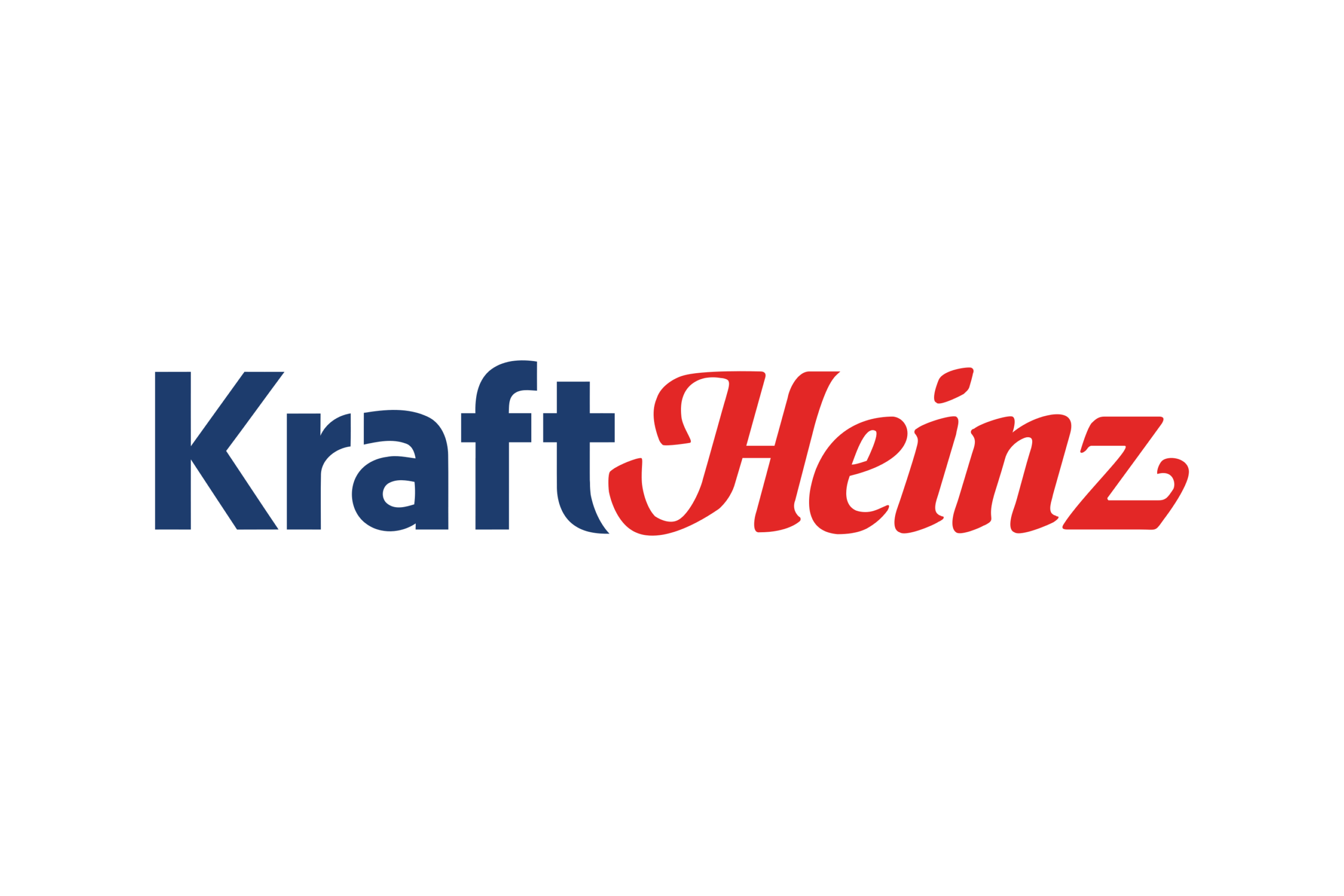
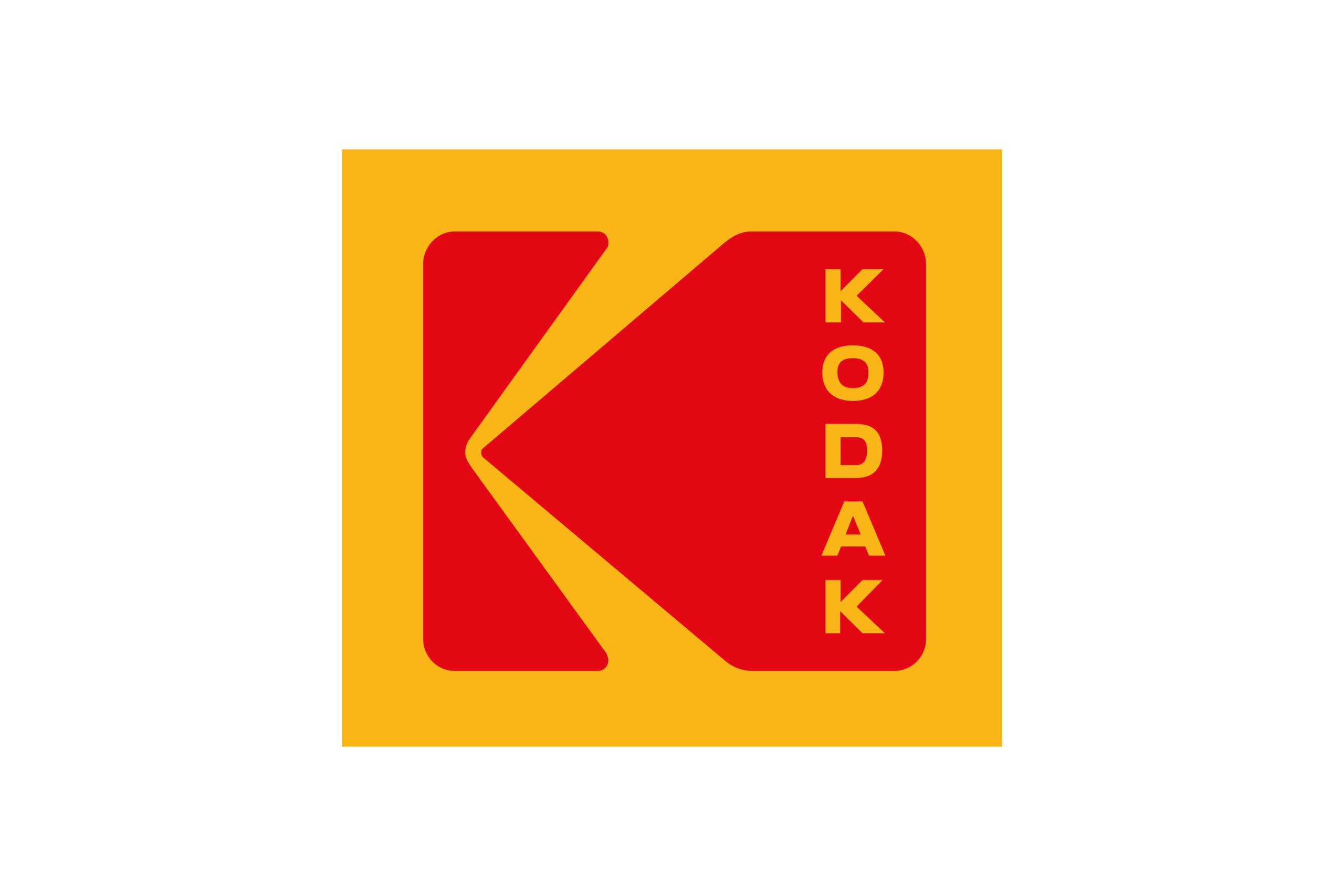
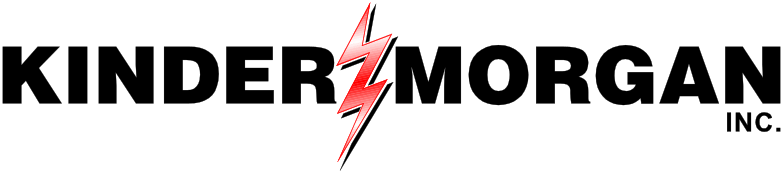
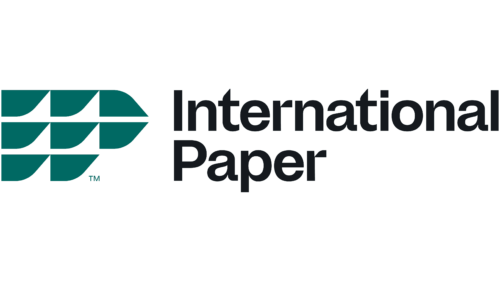
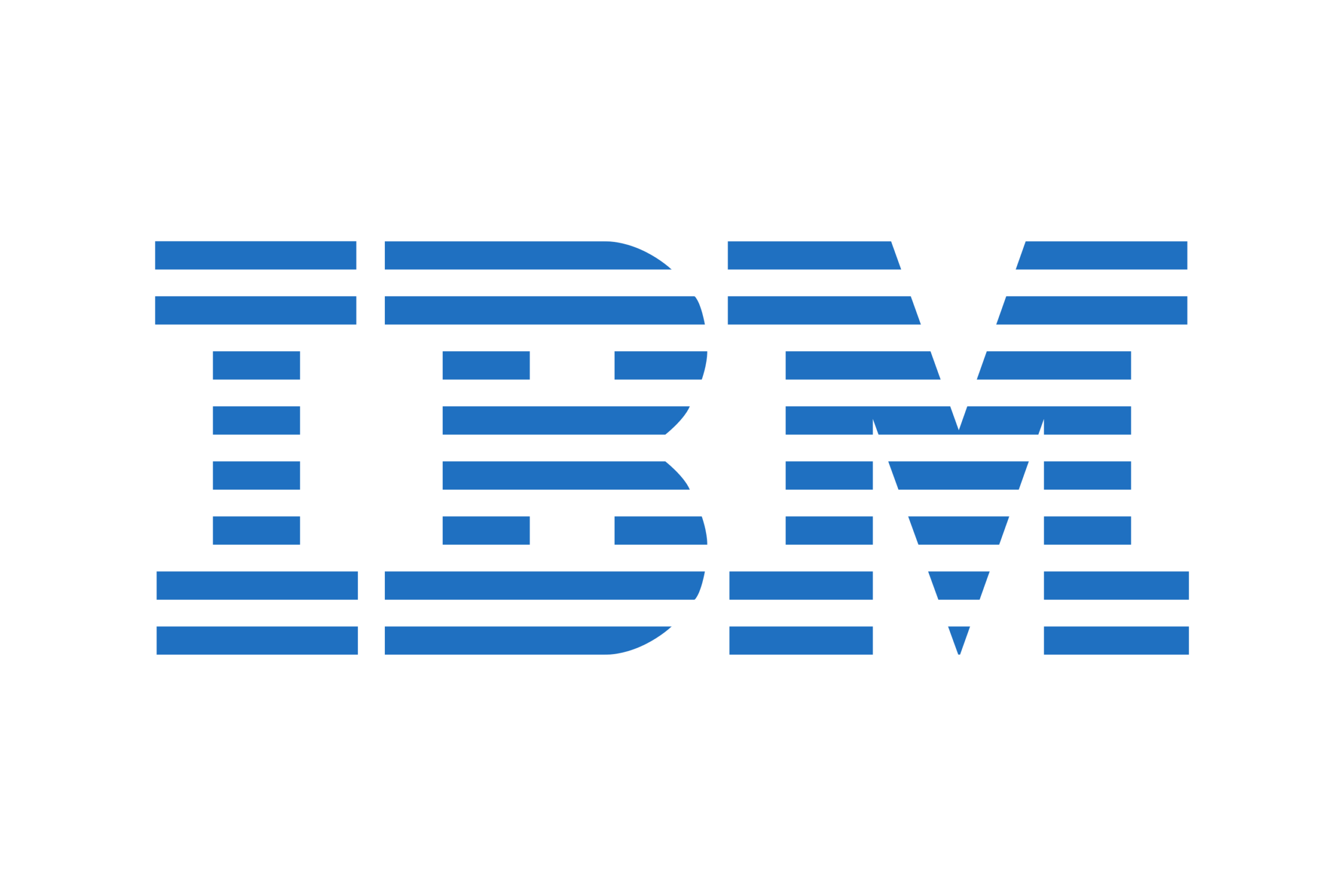

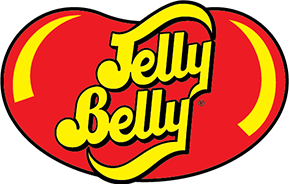
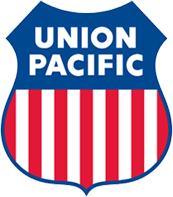
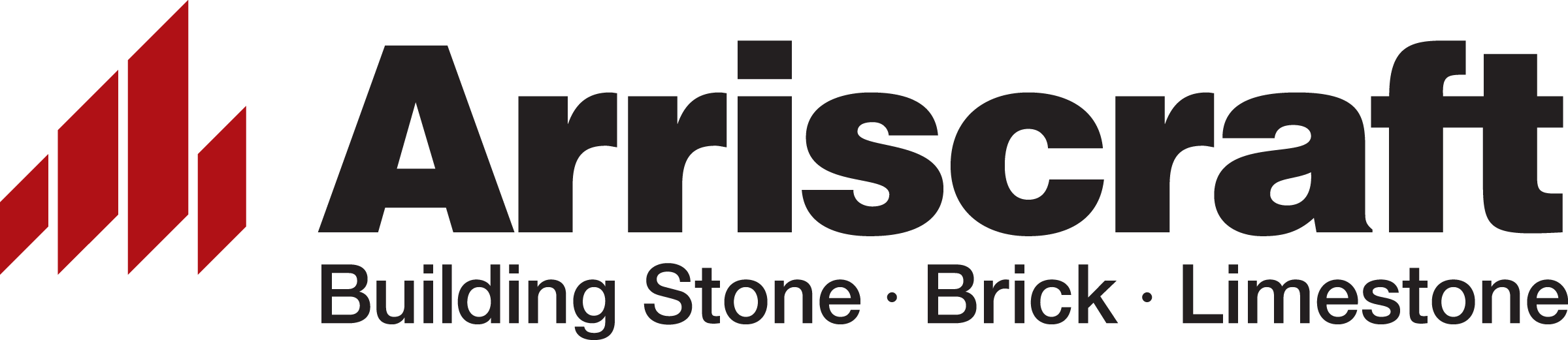

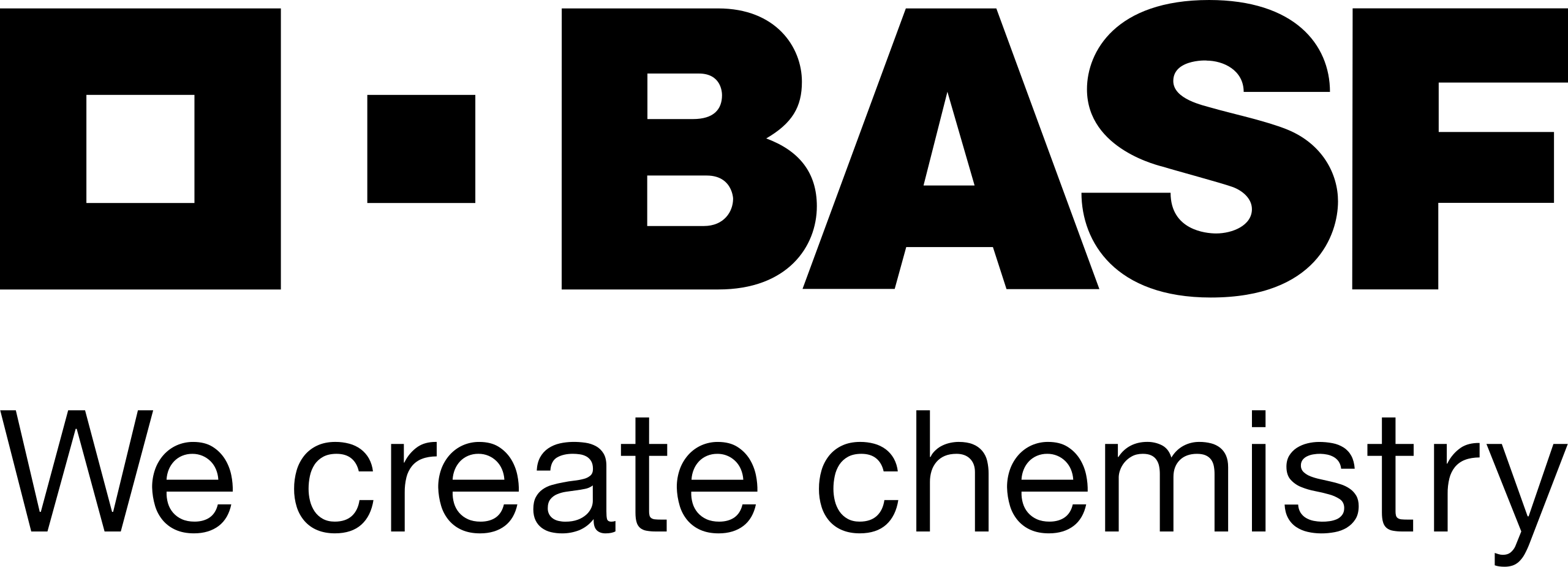
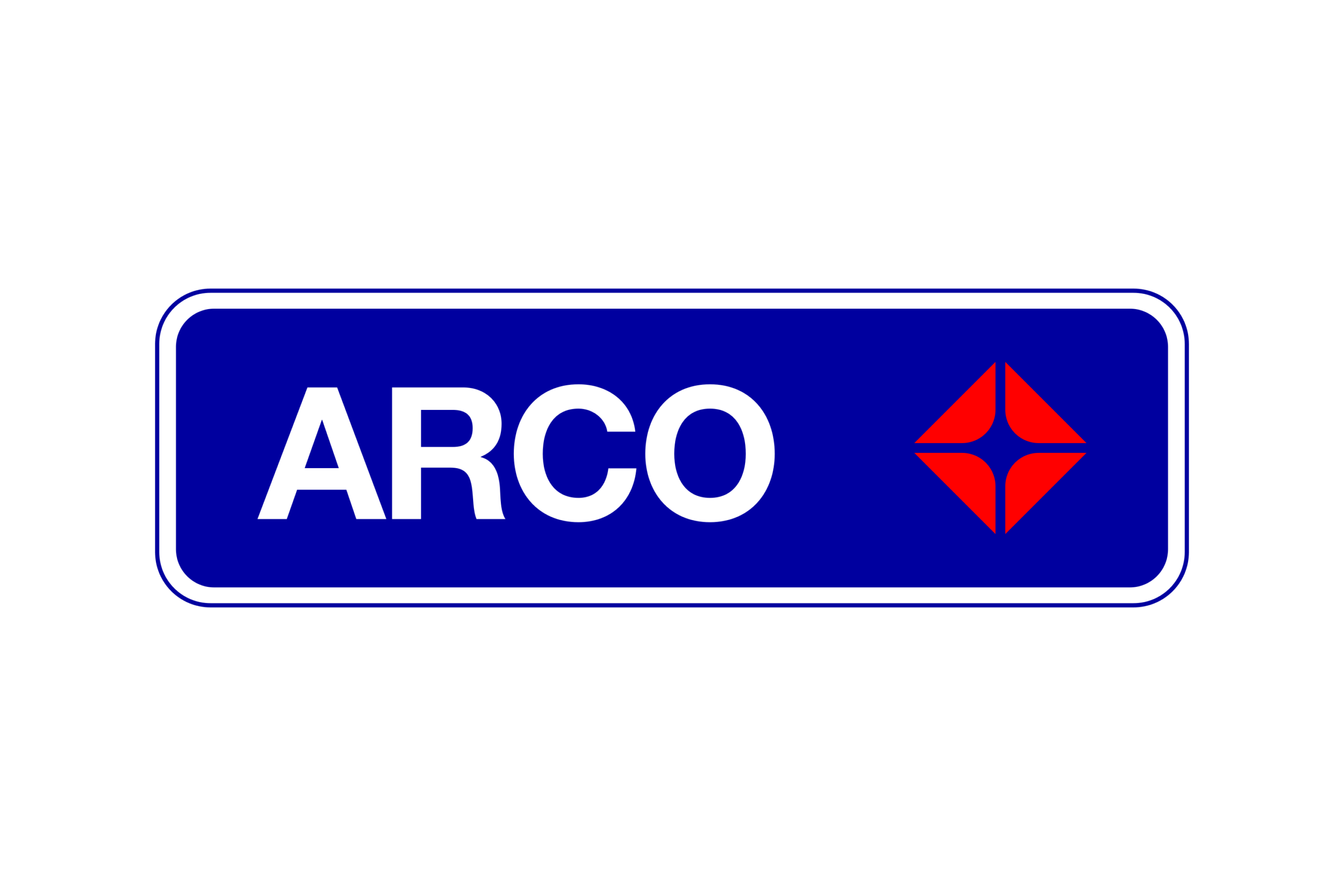
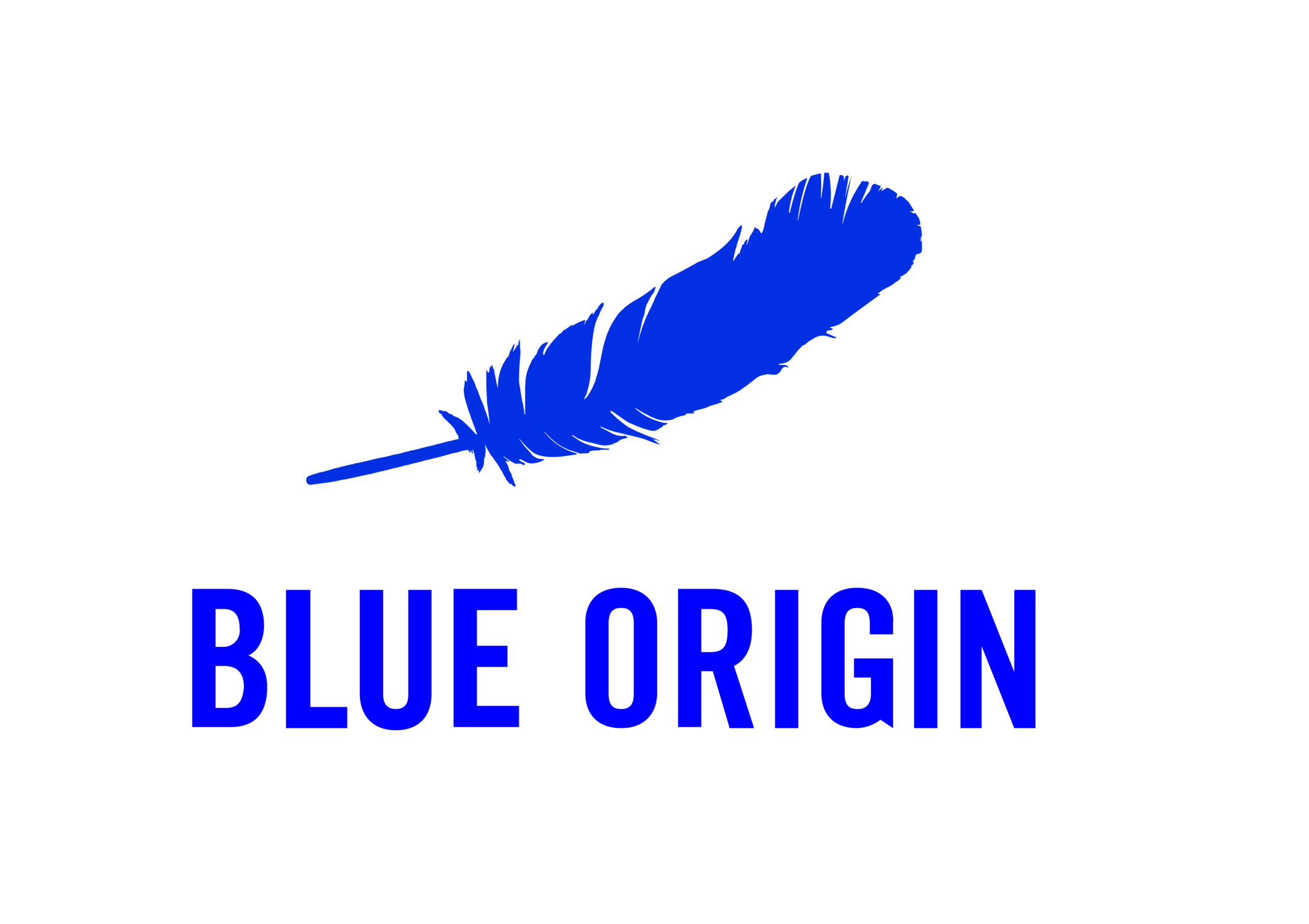
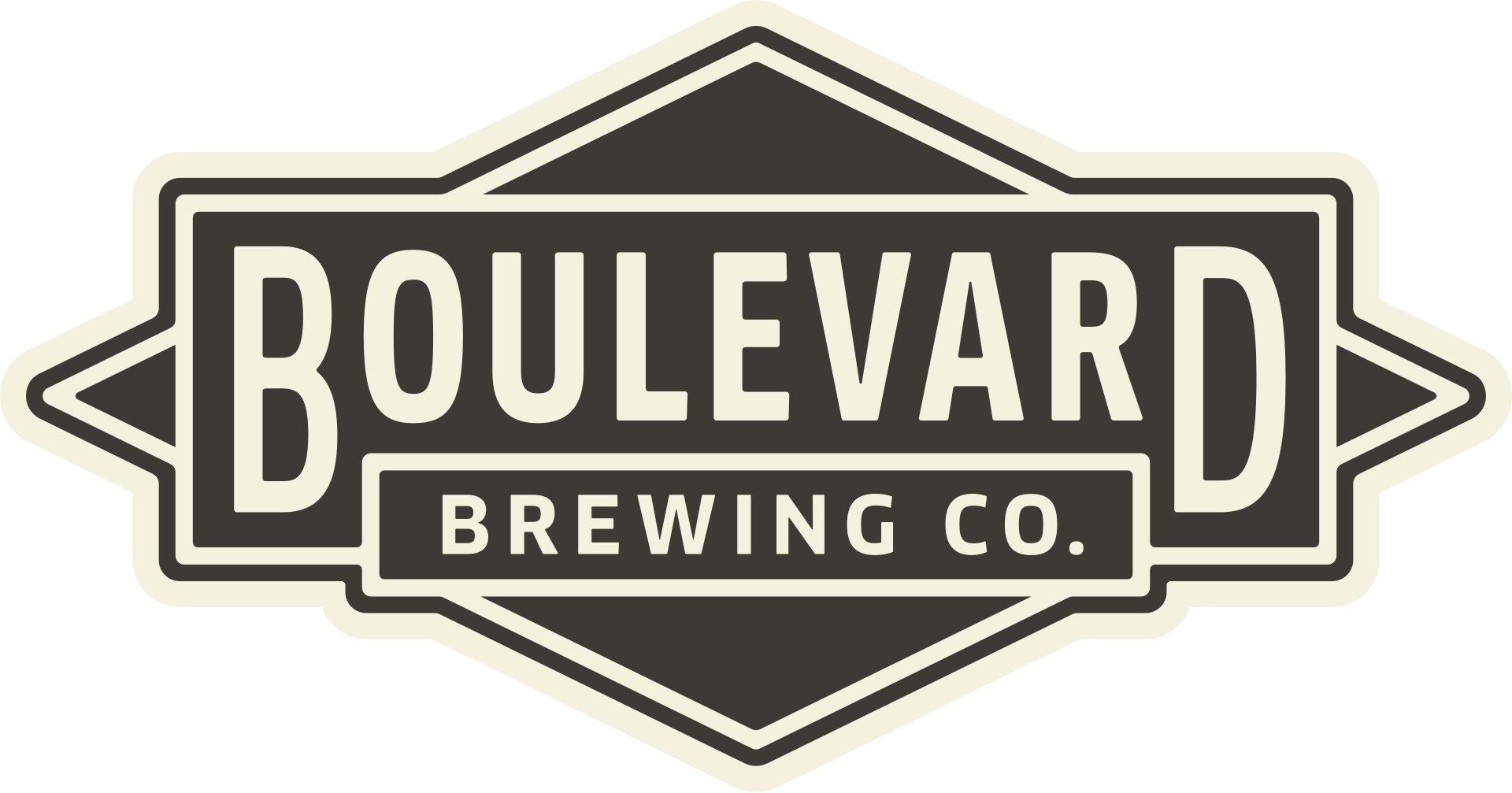
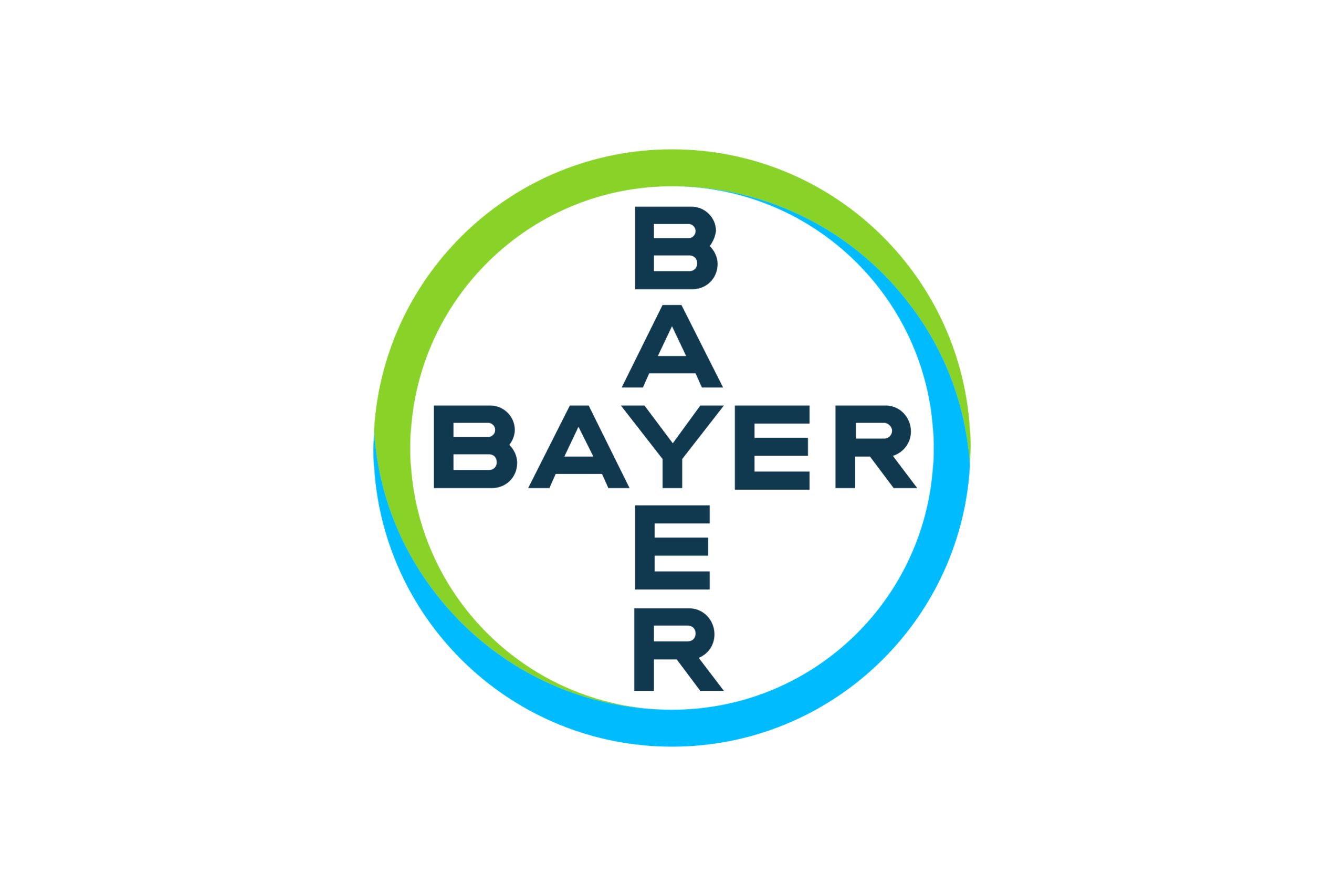
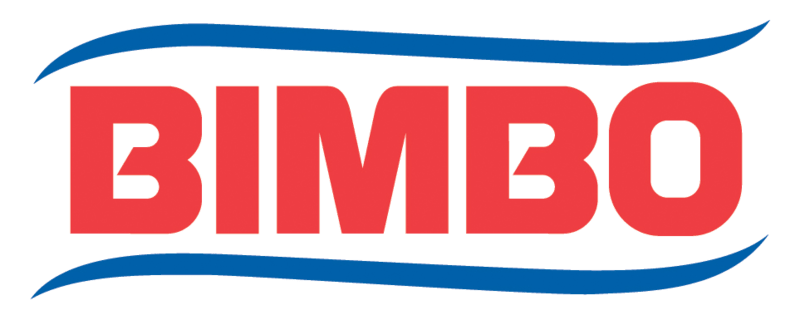
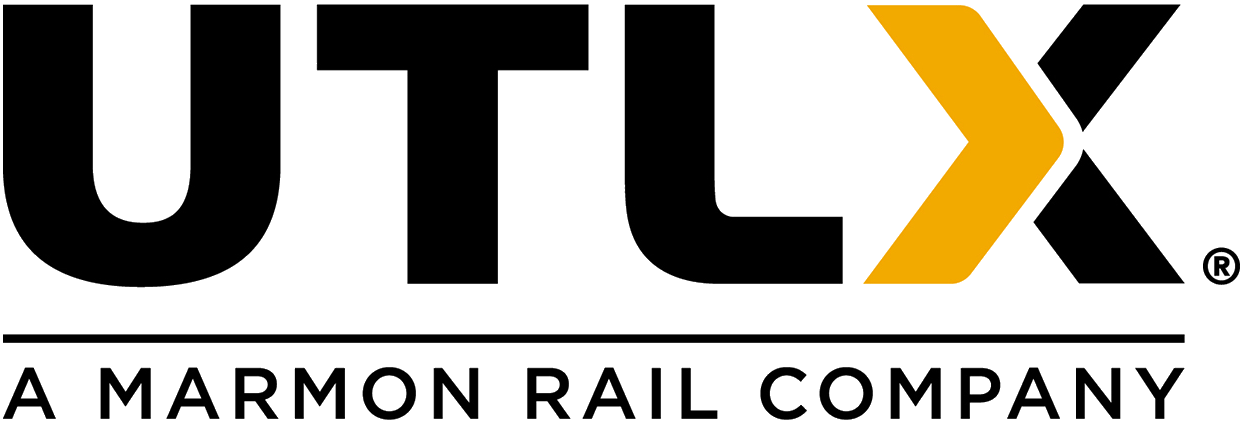
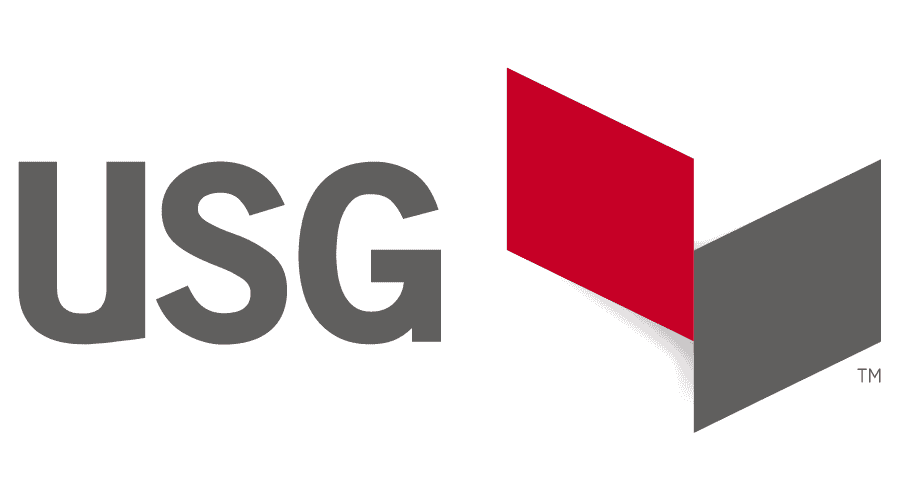
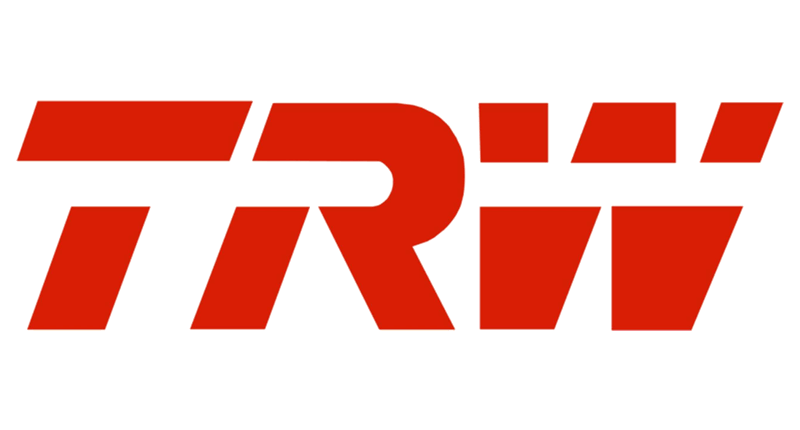
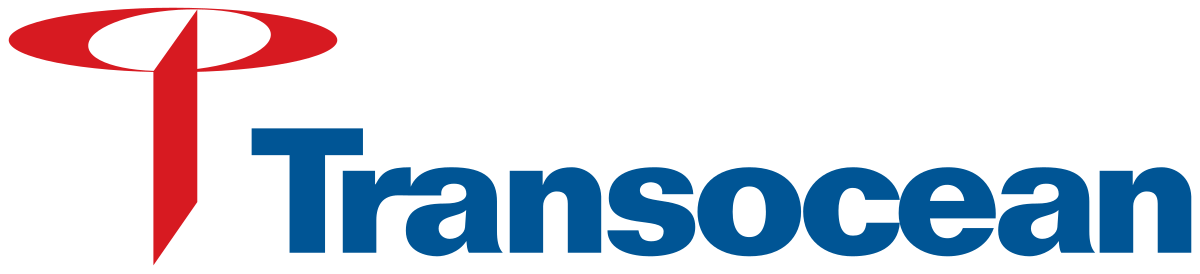

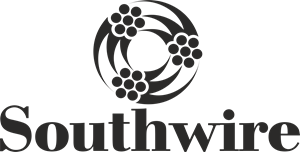
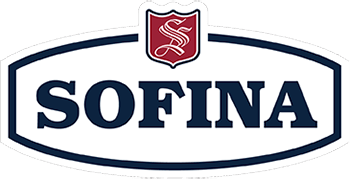
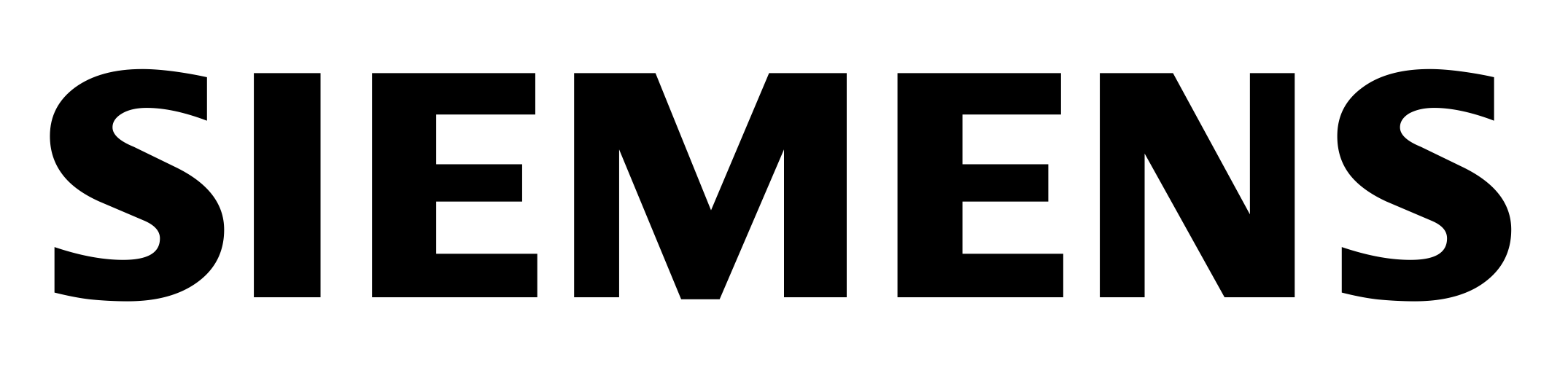
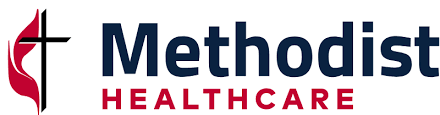
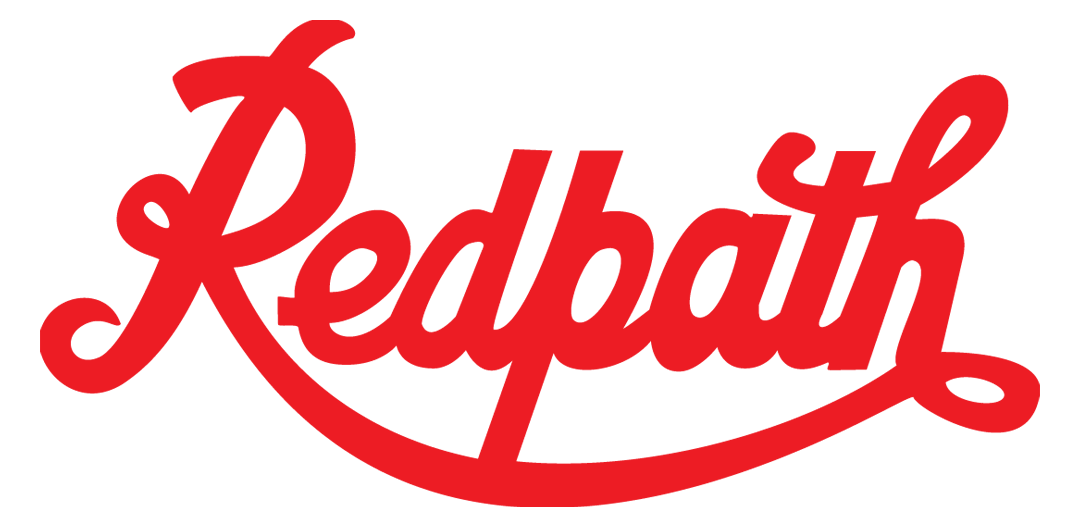
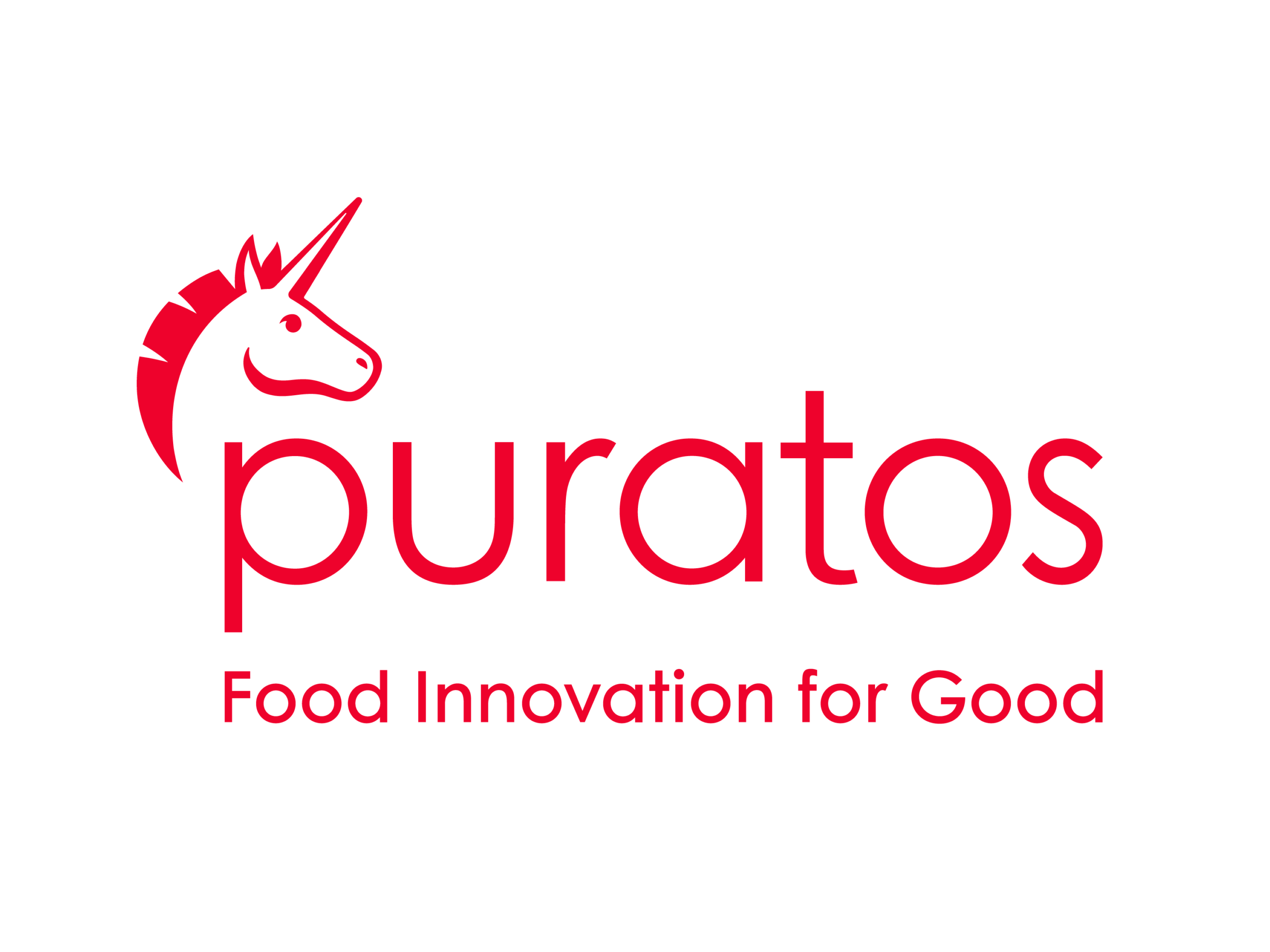
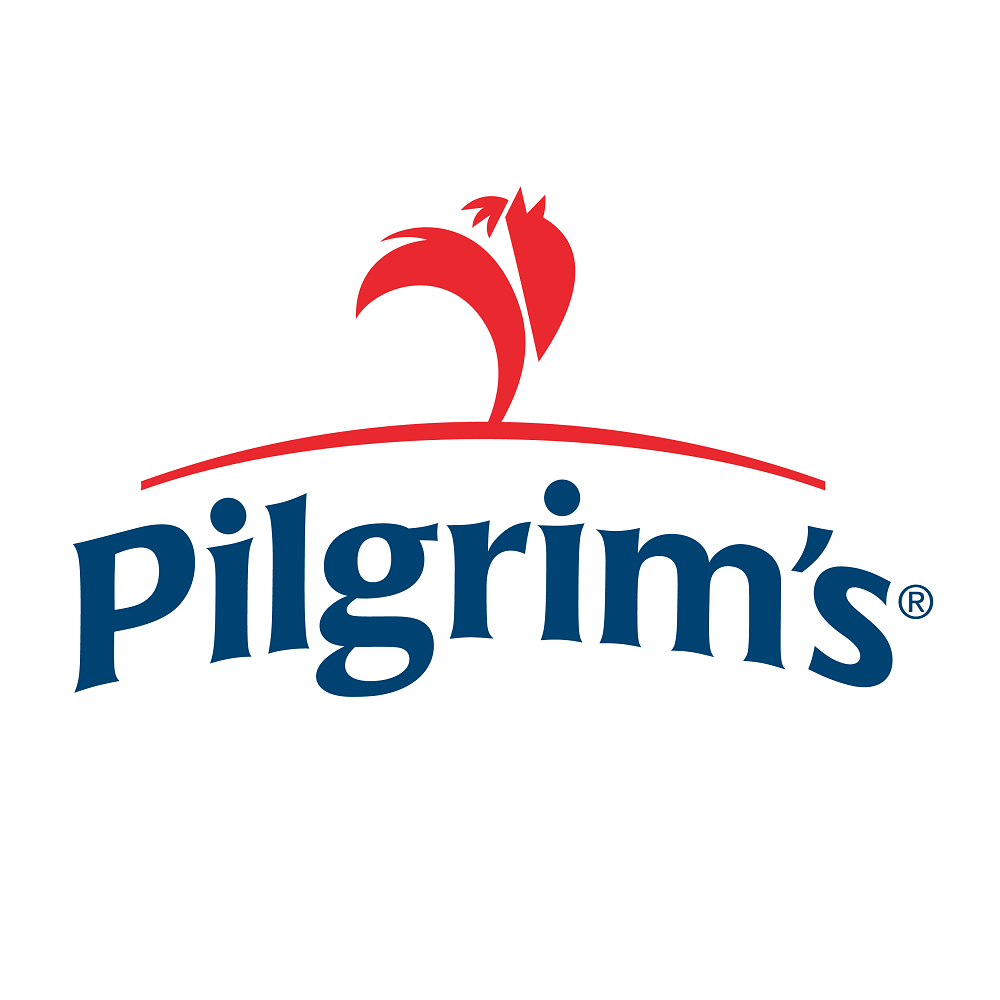
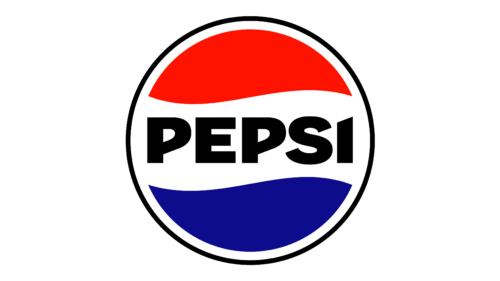
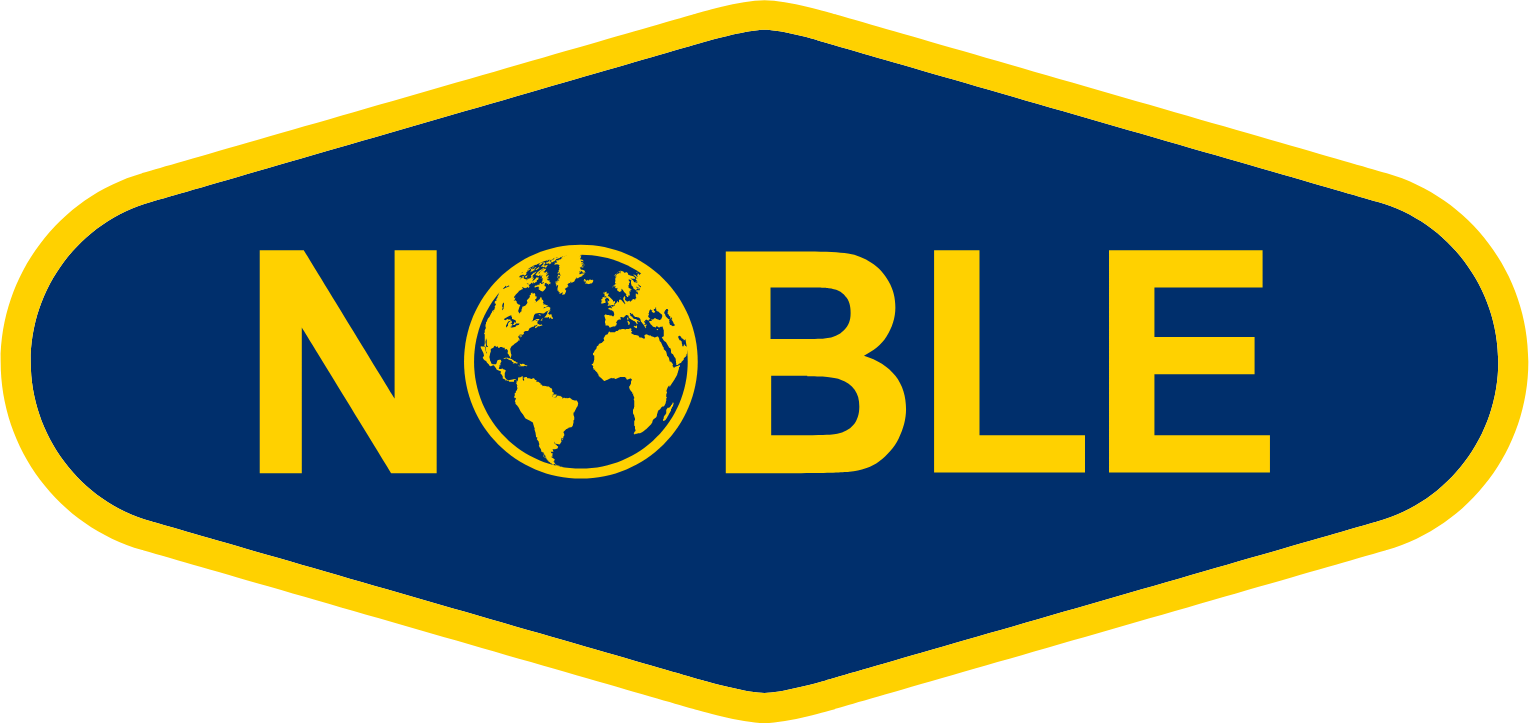
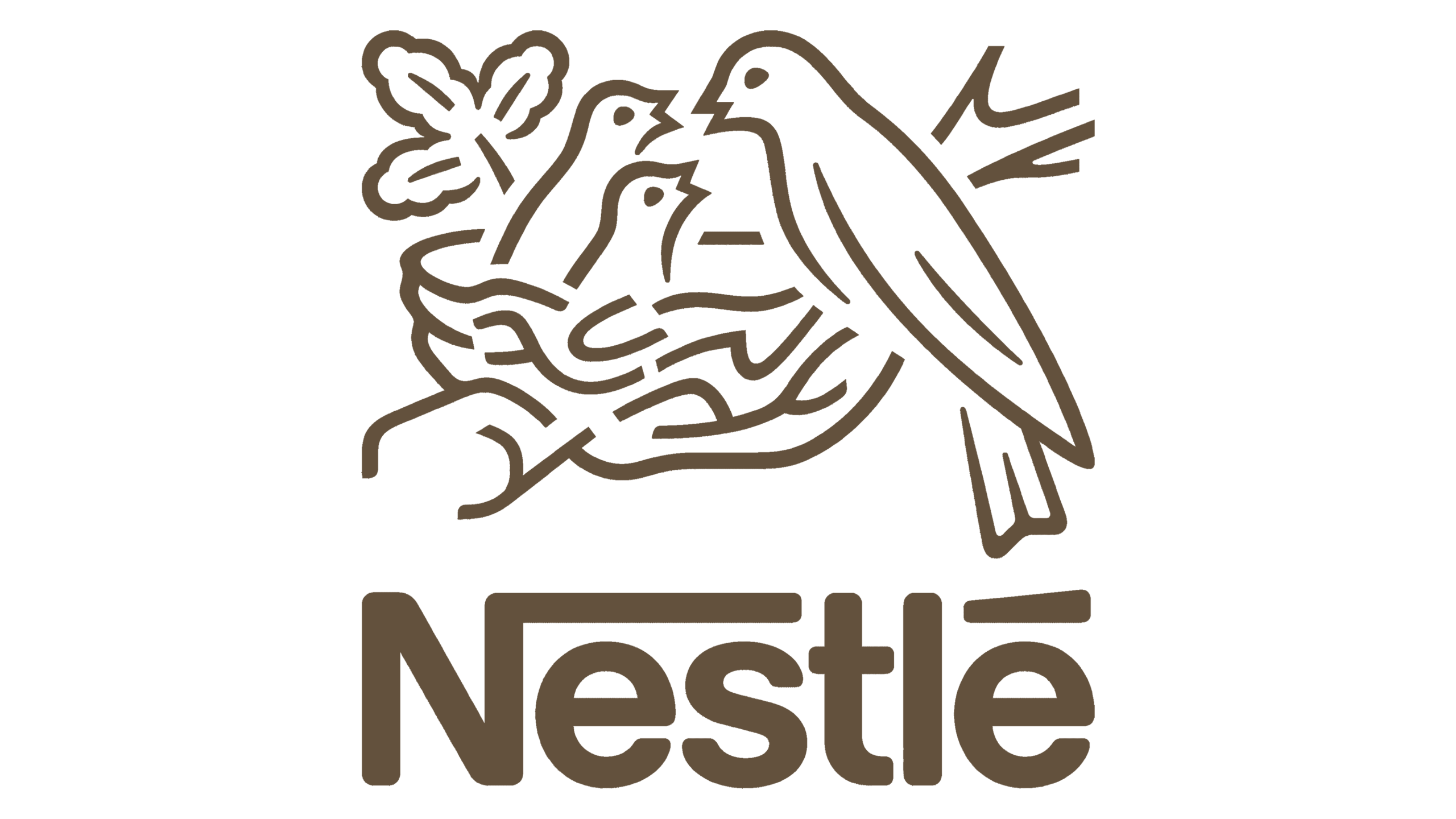
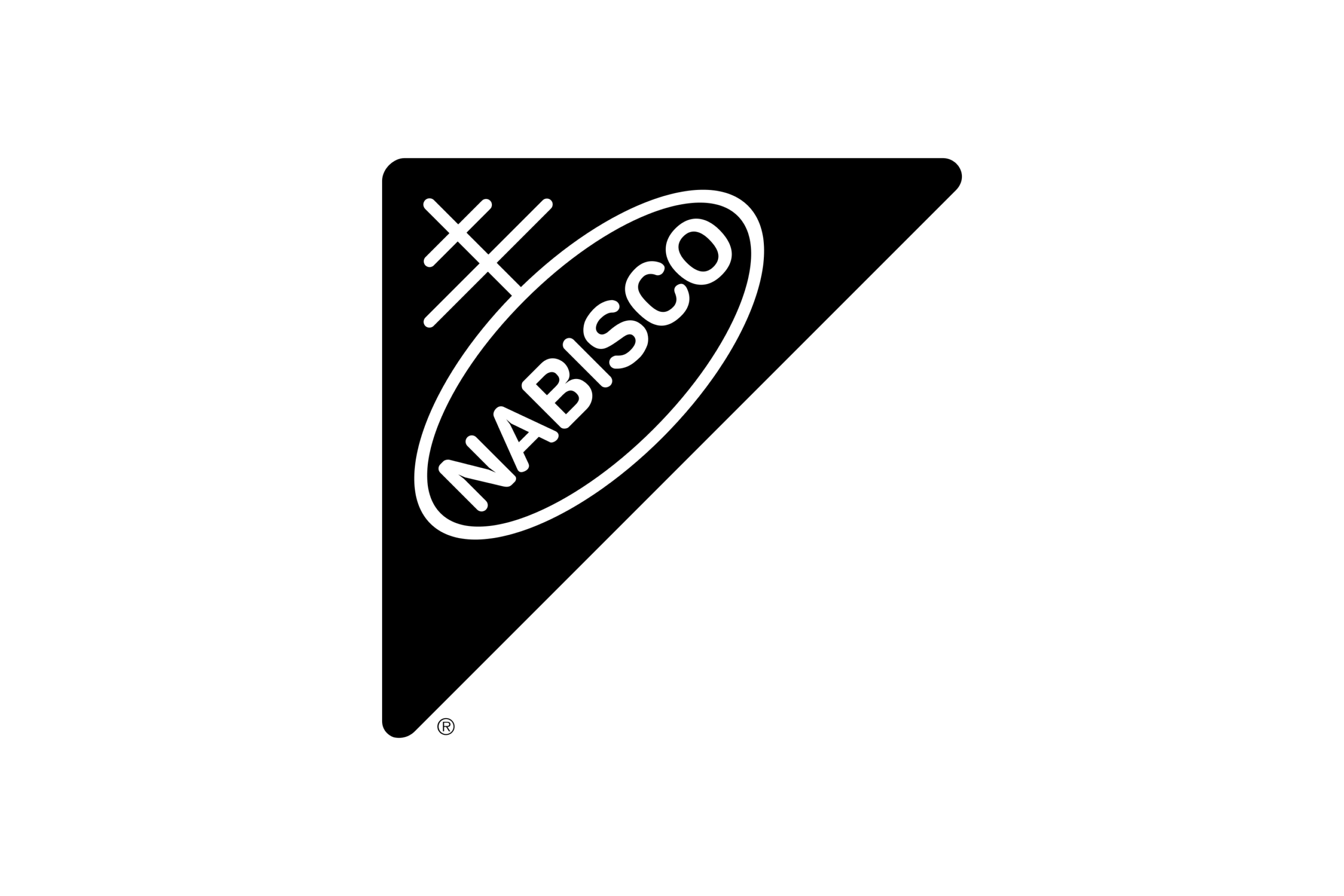
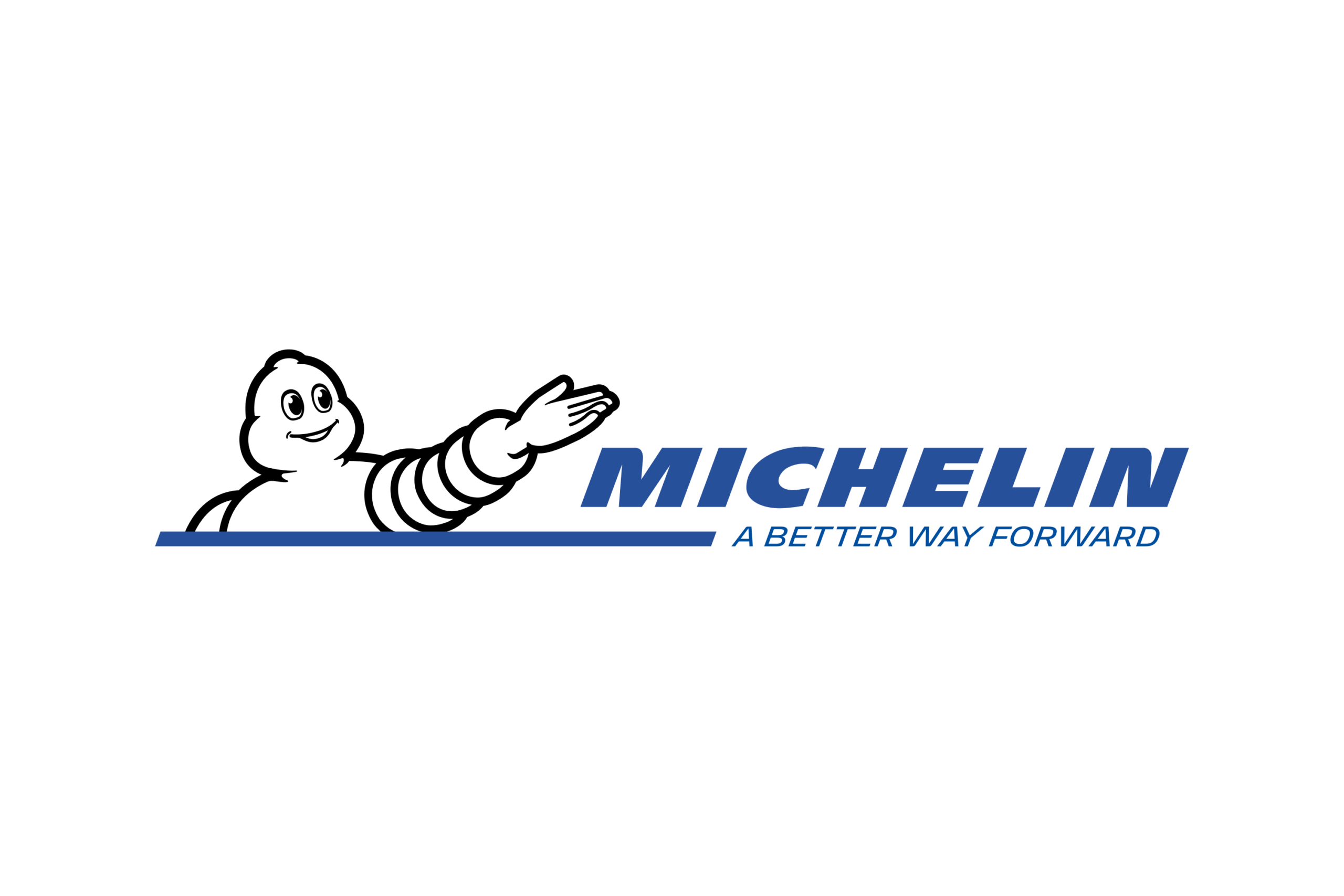
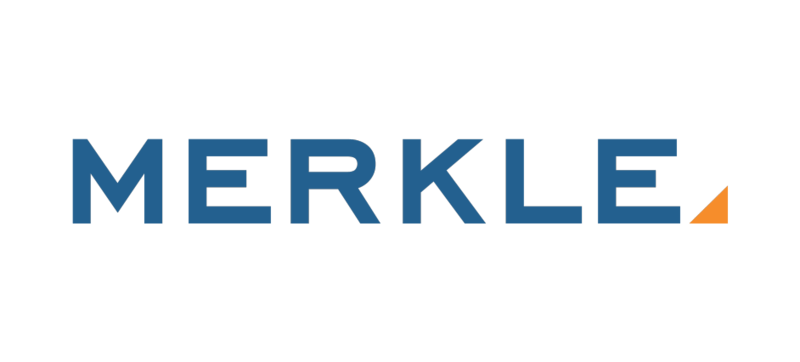

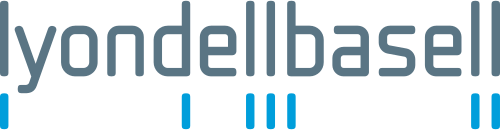
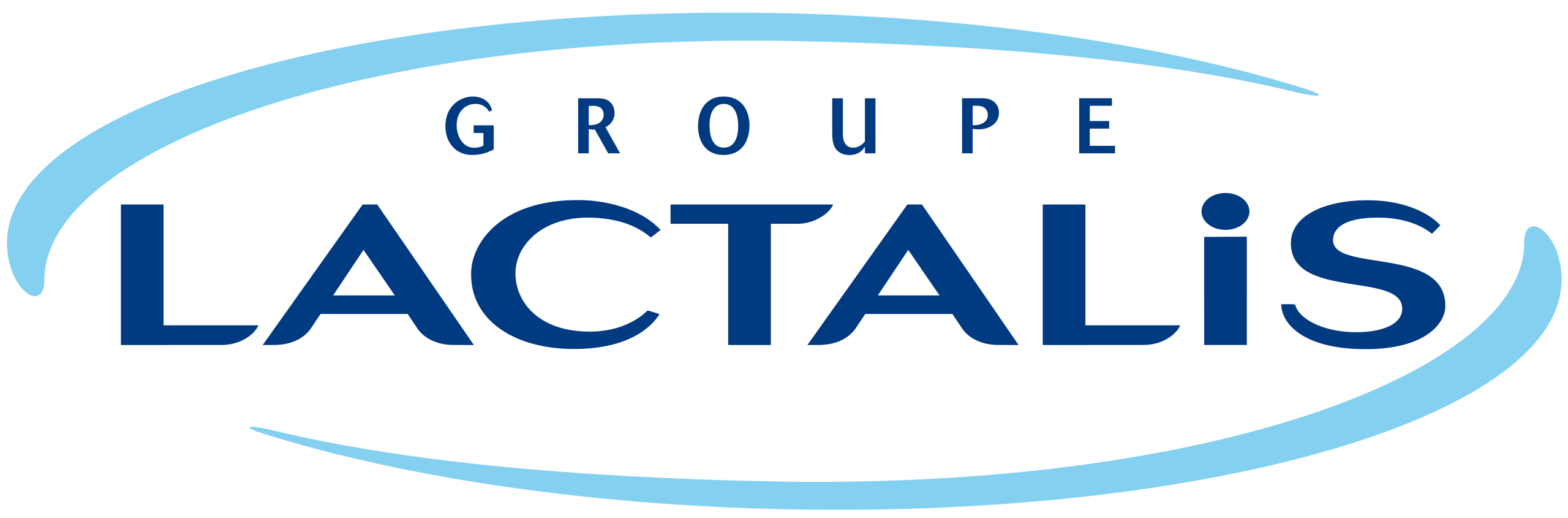
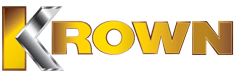
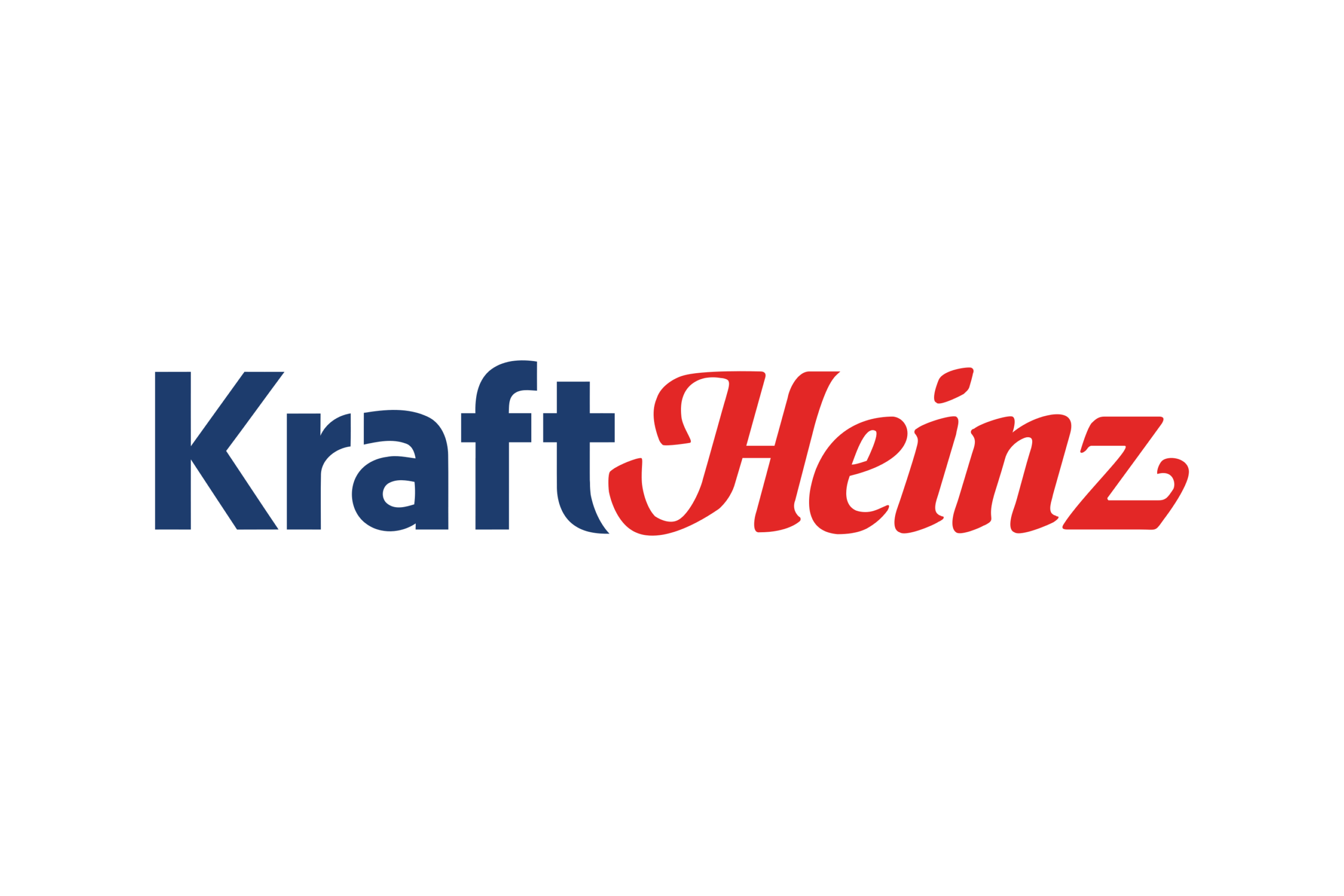
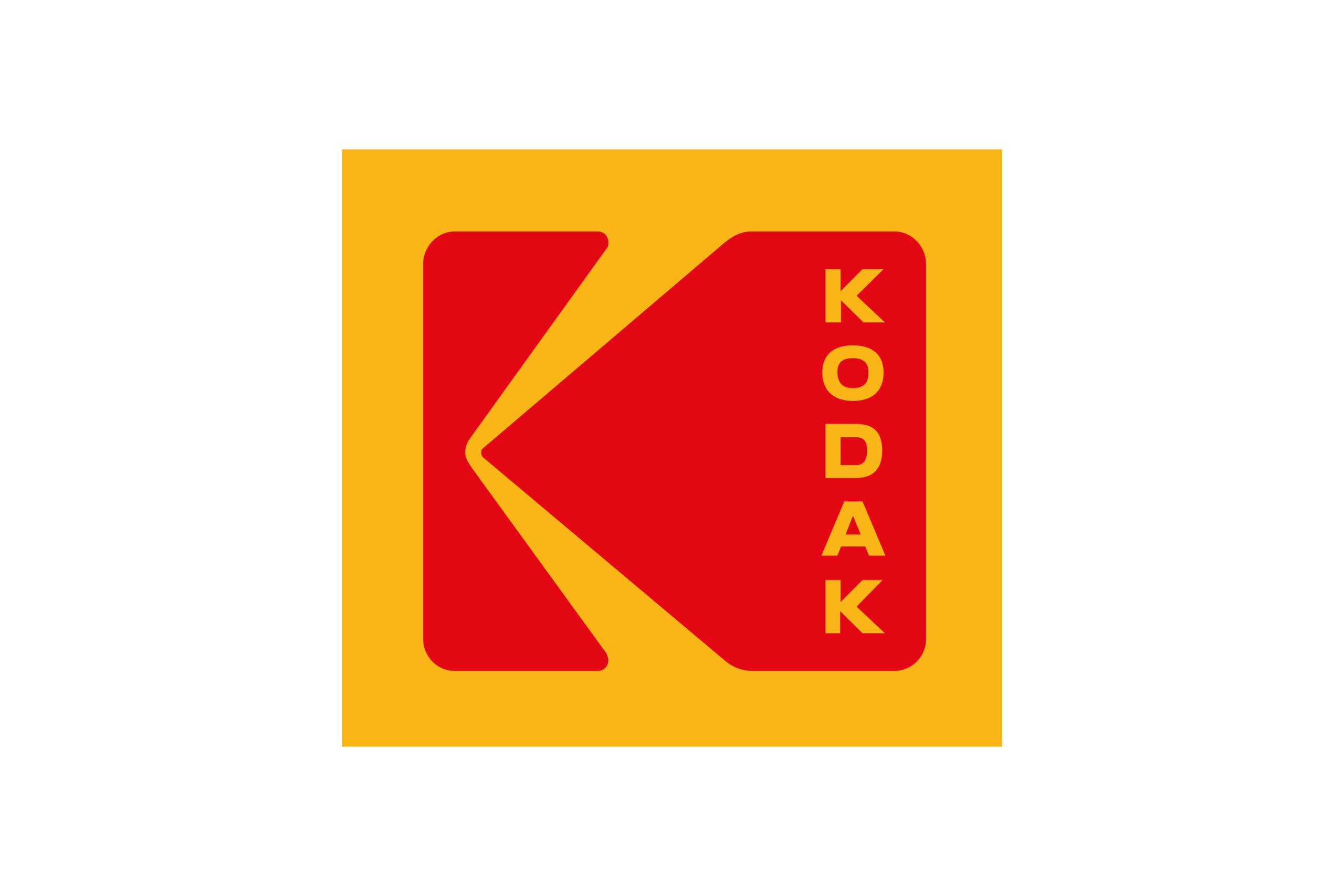
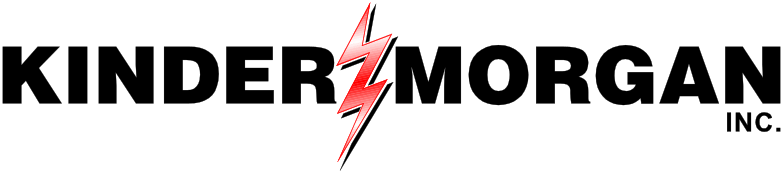
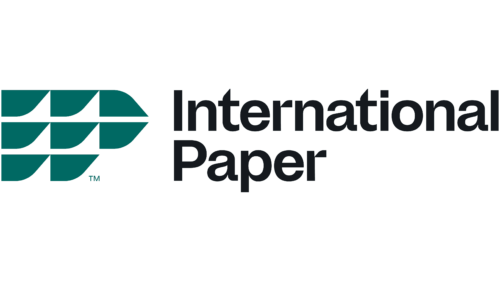
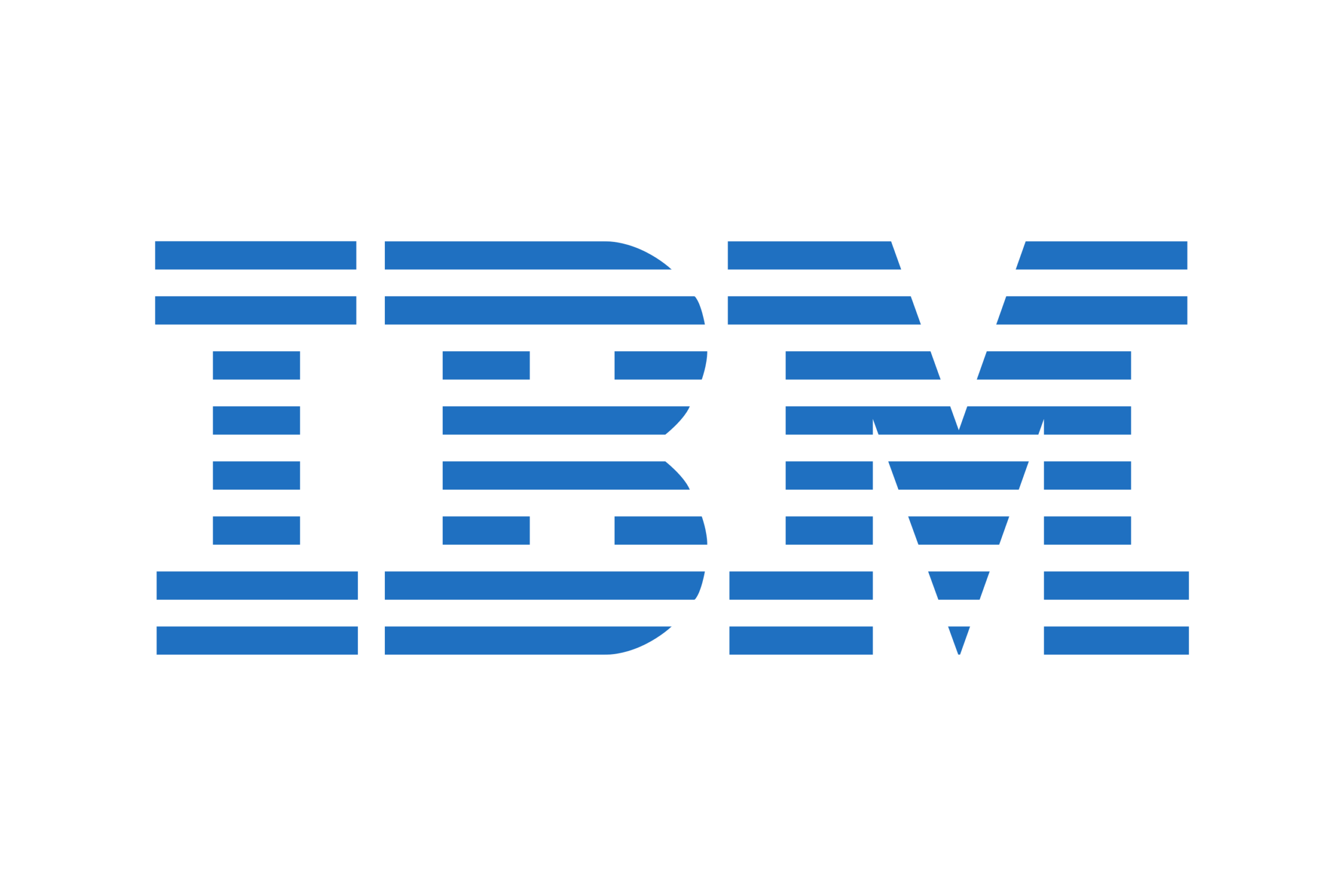

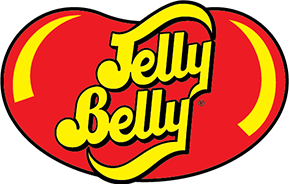
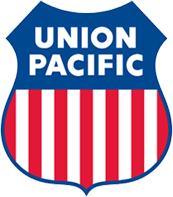