Steam generator creates the 99.5% dry heat needed for effective shrink sleeve labeling
As the only vertically-integrated bever- age development, manufacturer, and marketing company in the United States,
Power Brands has helped hundreds of beverage startups across the world actualize their unique drink visions. A client simply comes to Power Brands with an idea for a beverage, and then their team of specialized experts help bring the client’s brand to life — aiding them through every step of the design, production, and marketing process. With a new production facility opening in Los Angeles, Power Brands needed to obtain additional manufacturing equipment, including machinery to help adhere client’s product labels to beverage contain- ers — i.e., equipment for shrink sleeve labeling.
Steam tunnels: an effective method for beverage labeling.
Steam tunnels are popular methods for shrink sleeve labeling owing to their low temperature settings (around 180°-200°F), their ease of use, and their ability to apply uniform heat around the entire product.
The process is simple. First, a shrink sleeve applicator attaches the sleeves to the drink containers. Next, the containers are passed through the steam tunnels on a conveyor, where consistent heat is applied to the entire vessel. With this consistent application of heat, the sleeves are able to uniformly contract, shrink, and adhere to the bottles – making for clean packaged finishes.
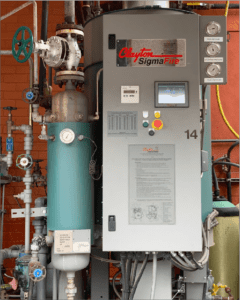
Another upshot of using a steam tunnel is that it can be utilized for diverse applications. To ensure client beverages are free from harmful microbes, Power Brands also needed equipment for pasteurization. A steam generator, with its heat treatment capacities, is a great way to sterilize liquids, along with other smaller applications. It was clear that a Clayton Steam Generator would be a propitious investment for Power Brands’ new facility.
Power Brands was in the market for a steam boiler.
The requirements for the steam generator were straightforward: they needed a boiler that could produce 550 pounds of steam per hour, with a steam pressure of 80 psig. This steam needed to be very dry, to allow the labels to properly cohere to the containers. Further, the boiler was going to be used every day starting at 4:30 in the morning. This meant that rapid and automatic startup capacities was crucial. And of course, obtaining a boiler with high fuel-effi- ciency and safety was of top priority.
Invited to assess the situation, the Clayton team led by Brian Dominici, determined the best equipment to meet Power Brands’ specifications was The Sigma-Fire SF50 Steam Generator 50 BHP with Low NOx FMB Burner and Super Economizer.
Advantages of Sigma-Fire’s once- through design.
Clayton’s steam generators, unlike typical steam boilers, utilize a once- through design where steam is creat- ed by using a positive displacement feedwater pump controlling water flow through a single helical coil tube. With this design, Clayton can fully modulate the water through the coil to match fuel and air ratios. The unit modulates up and down following desired steam-operating pressure.
This enables Clayton to be highly effi- cient throughout the entire operating range, regardless of firing rate.
The Clayton Steam Generator oper- ates with low water volumes, which allows them to start-up very quickly from a cold start. Clayton’s equip- ment also creates the ability to react very quickly to changes in steam demand. The unit can reach full steam capacity form a cold start in minutes rather than hours. This low water content fully eliminates any potential of a steam or water explo- sion — making it one of the safest steam solutions on the market.
Conveniently, this entire process can be started with a flip of a switch or with an automated startup option, allowing for minimal supervision.
Energy-efficiency of counter-flow design over firetube
Sigma-Fire’s unique counter-flow design inherently improves fuel efficiency over conventional firetube boilers, by at least 5%. And with the added economizer, this generator can utilize recovered flue gases to warm the boiler feedback water – decreas- ing the firing rates, and further maxi- mizing the fuel-to-steam efficiency.
99.5% dry steam ensured at all times By utilizing a steam separator that uses high-velocity, fixed vain mechan- ical separation, the Sigma-Fire gener- ator efficiently spins out excess mois- ture providing 99.5% quality steam to the process. The excess water is trapped back to the feedwater system saving btu’s. This method makes for a safer, more reliable operation as well as lowers blowdown rates.
And with Sigma-Fire’s versatile design pressures, which range from 15 psig to 500 psig (or in some cases, 3,000 psig), Brian saw it was a
cinch to meet Power Brand’s 80 psig requirement.
Clayton customer support
The Sigma-Fire steam generator is pre-certified with the South Coast Air Quality Management District. Thus, Power Brands did not have to go through the hassle of applying for or obtaining an air quality permit, only local permits. But Clayton assisted the local permitting process.
As CEO Darin Ezra attested, “I would say Clayton has by far the best service department I have ever
worked with when it comes to manu- factured equipment. No matter what day, what time or what circumstance, we can always count on Clayton to support us. They offer really amazing services above and beyond on every occasion.”
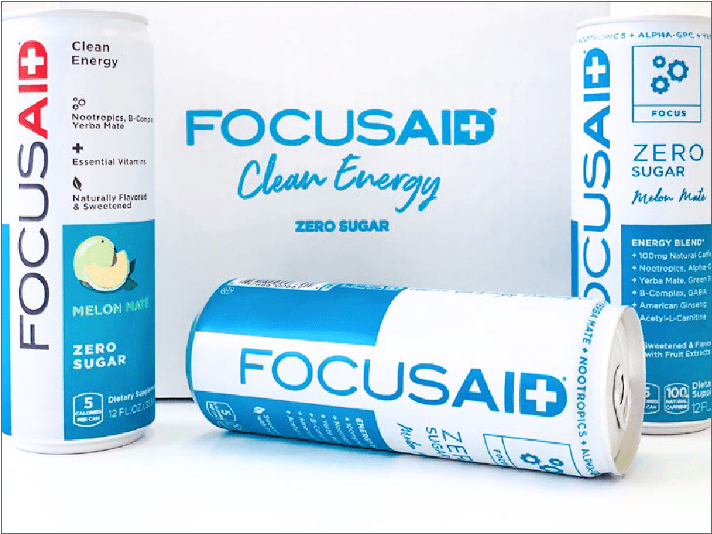