In biomedical waste management, the efficiency of the autoclave is everything. With Clayton’s recommended solution, Daniels Health began operating 25% faster.
Dan Daniels founded the company from a garage with nothing but makeshift PVC waste tubes and quest to reduce incidents of sharps injuries from medical waste handling in healthcare. Fast forward 30 years and Daniels Health is now one of the most influential healthcare service companies, boasting the safest sharps containers and medical waste management systems in the world. “Sharps” is a medical term for devices with sharp points or edges that can puncture or cut skin, such as needles and syringes. Daniels offers a full-service schedule for sharps, RMW, pharmaceutical, chemotherapy, RCRA Hazardous, and USP 800 classified waste.
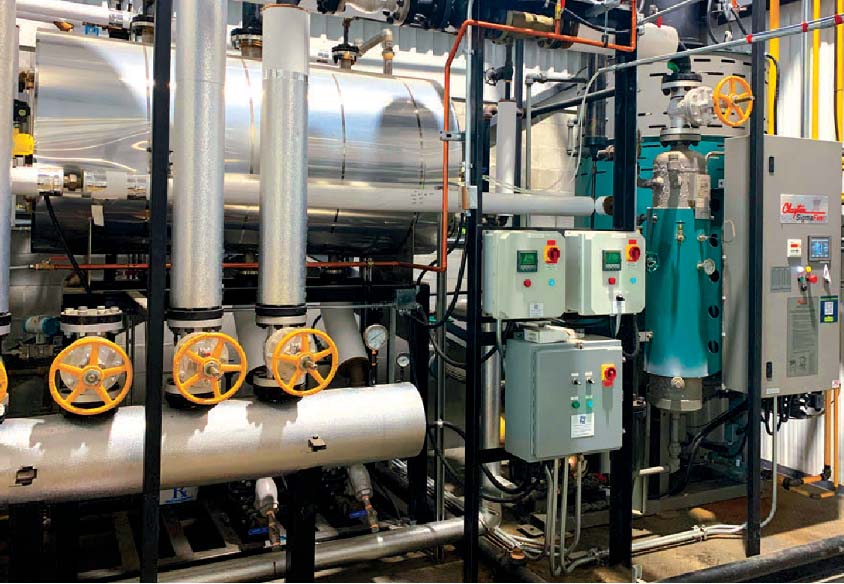
The old boiler that Daniels Health in Brampton, Ontario, Canada, needed to replace took up to 75 minutes to complete a sterilization cycle. After installing a Clayton SigmaFire SF200 Boiler with 200 HP and 300 PSIG, feedwater tank, and the accumulator, the autoclave cycle time was cut down to 55 minutes.
As the company added new plant locations across North America, it relied on used boilers to help keep capital expenditures in check. Usually, management wouldn’t call themselves fortunate when a boiler needs replacing. But for Daniels Health in Brampton, Ontario, Canada, the efficiency they gained made this a different story.
The time had come to replace the aging boiler. Daniel Kennedy, CEO of Daniels Health Canada, along with David Prince, VP Operations, reached out to a few of their trusted vendors and asked for proposals.
“After a diligent investigation that included site visits with each vendor’s customers, we ultimately chose Clayton because of their sales manager’s detailed response. [Clayton’s] Ron Polidori is an absolute pleasure to work with,” said Prince. “And Clayton has excellent equipment, ethics and integrity.”
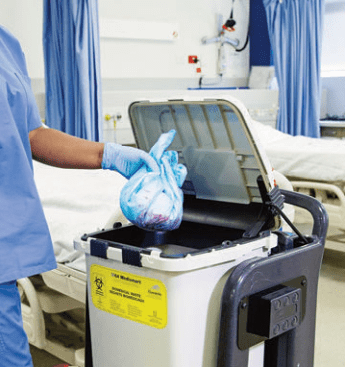
Daniels Health uses steam within the cleaning process for its propietary resuable sharps management system, one of the safest sharps and medical waste management systems in the world.
Polidori said, “Rather than just pricing out a replacement, I thoroughly evaluate the customer’s situation to see what Clayton can do to improve their operation. Arriving at the right answer starts with asking the right questions, like “How do you use the steam? What are you trying to achieve? How can we increase your efficiency?”
Daniels Health has a large pressure vessel where they sterilize biomedical waste. It requires a certain steam pressure and high temperature. The problem was that their current boiler – a horizontal coiled tube boiler – wouldn’t allow steam to come in fast enough to satisfy the autoclave, which resulted in the sterilization cycle time taking 60 to 75 minutes to complete. That was too long. As a result, productivity wasn’t where it needed to be. Plus, the long cycle time was taxing on the boiler, which meant high maintenance costs and expensive downtime.
The boiler is the company’s lifeline. No steam, no production. The boiler system has to be dependable and provide maximum uptime.
Daniels Health needed more than a boiler replacement. They needed a strategy.
The Clayton team determined Daniels needed a boiler and a steam accumulator that would produce maximum steam in the shortest time possible. The accumulator stores energy in the form of water, which flashes to steam quickly. Polidori explained, “With the accumulator being ’charged and ready, ’ it can provide the autoclave with steam on-demand as needed, literally in seconds.”
Kennedy expressed reservations because they had tried accumulators in the past and had mixed and inconsistent results.
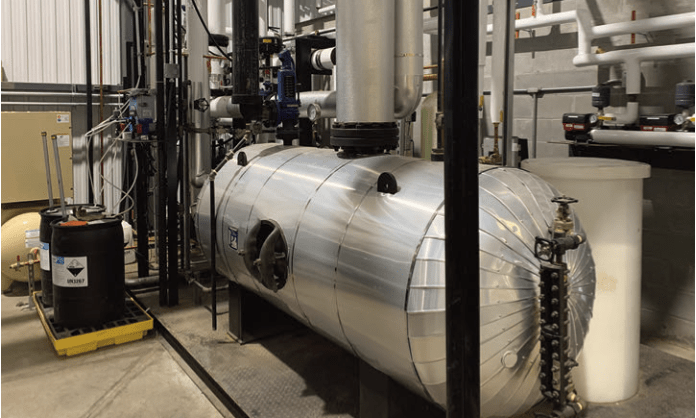
Powered by the new, more efficient Clayton Industries boiler and specially designed accumulator, the autoclave at Daniels Health in Brampton, Ontario, Canada, began operating a whopping 25% faster.
But Clayton knew it was the right answer. They just had to find a custom solution that would ensure optimal operation. Clayton’s steam expert, industry partners, and the engineer from the accumulator manufacturer met and designed a system they knew would work.
Their solution? A Clayton SigmaFire SF200 Boiler with 200 HP and 300 PSIG, feedwater tank – and the accumulator they had evaluated and approved. The cycle time with the old boiler took up to 75 minutes. With the efficiencies of the new boiler and accumulator, the autoclave cycle time was reduced down to 55 minutes.
Kennedy said, “The Brampton location is the busiest in North America volume-wise. We just recently secured a very large contract. Had we still been operating with the old boiler system, running 20 autoclave cycles a day would’ve pushed it beyond capacity. That would’ve created another big issue: transferring waste to other locations, which is costly.
“Clayton’s solution shaved off 10-15 minutes from each cycle. Multiply that by 20 cycles a day, and it frees up 5 hours a day, which gives us the capacity to handle increased volumes without the need to transfer waste.”
There are more than 20 Daniels Health locations in North America, and the U.K. Kennedy says they continue to work with Clayton Industries because of the quality of equipment and because they believe it’s the best value.
“Like Clayton, we’re not the least costly, but it’s what you get for the cost that equals the value,” Kennedy said. “The bottom line is, our customers want the waste to go away but in a way that complies with their health and safety standards. We are a heavily regulated industry. Daniels makes a significant investment in what we do and where we do it. We’re just a better choice.”
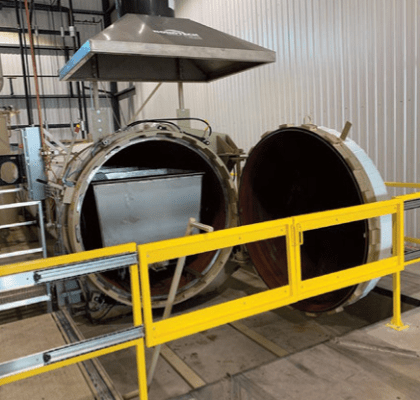
Clayton’s team designed a solution that shaved 10-15 minutes off each autoclave cycle. Multiply that by 20 cycles a day, and it frees up 5 hours a day, giving Daniels Health capacity to handle increased volumes of biomedical waste.
Daniels Health safe practices have become the benchmark of global standards, its robotic washing and treatment technologies have achieved benchmark levels of decontamination, and its products are esteemed industry-wide to be unrivaled in protecting the safety of healthcare workers.
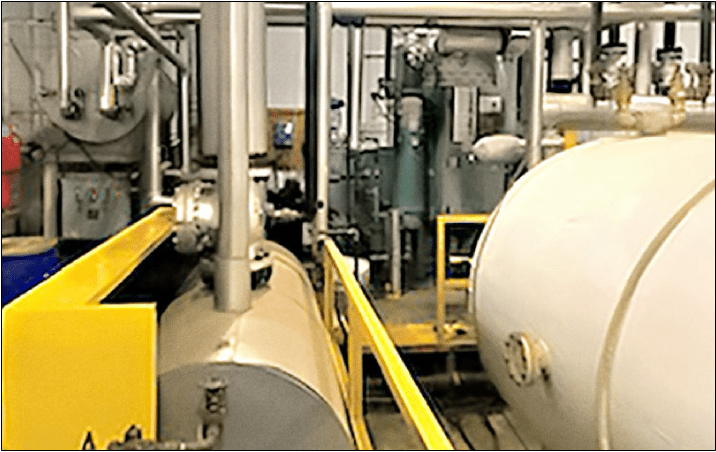