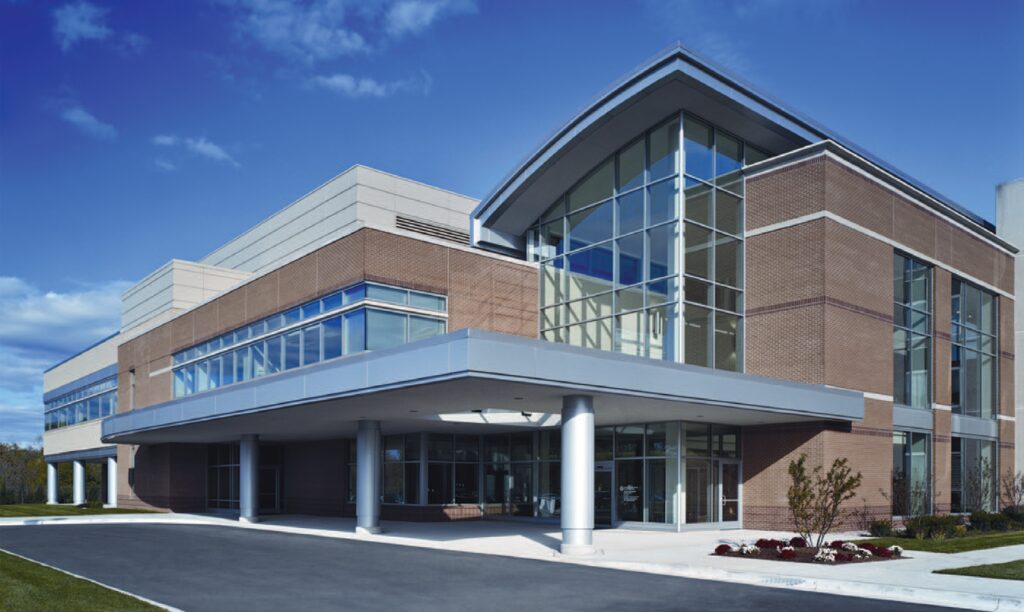
For 65 years, Mount Clemens Regional Medical Center has been a staple in Macomb County, Michigan, not only as a premier healthcare facility, but also as the area’s top employer. The Medical Center has grown from 40-bed facility, with about as many doctors on staff, to a 288-bed acute care hospital with a number of offices and medical buildings and more than 460 physicians and 2,600 employees. It is a major part of the community it serves and its teaching program also attracts hundreds of students from around the country.
But, like other hospitals throughout the United States, in order to stay solvent, Mount Clemens needed to find ways to improve performance and cut costs. So, in 2006, it looked to Siemens Building Technologies and its Integrated Performance Solutions Program to audit and find ways to contain energy costs.
Significant Savings Realized
The program provides a comprehensive building plan customized to meet the needs of the individual client. In this case, Siemens experts focused on energy efficiency. Nearly four years since the audit, the energy makeover has amounted to a huge savings for the hospital, thanks to major changes to the physical plant’s power, lighting, HVAC and water systems.
“Prior to the audit, Mount Clemens Regional Medical Center boiler plant consisted of four high-pressure steam boilers; two 400 HP units that provided wintertime heating load and two 300 HP units that provided the summer thermal loads,” explained Keith Miller, Director of Facilities Management at Mount Clemens.
Siemens experts knew this system needed to be replaced with something that ran cleaner, simpler and more consistently. They looked to Clayton Industries to replace the old boiler with a vertical steam generator. The two existing 300 HP Johnston gas-fired boilers and burners were removed, as well as all of their accessories and accompanying equipment to accommodate the new gas-fired steam generators. The new units were a 300 HP generator and a 500 HP one.
Miller said almost immediately after the installation, Mount Clemens enjoyed an improvement in overall plant efficiency.
“After the installation of the Clayton Steam Generators, we measured the monthly steam flows from the generators and compared those to what would have been the actual amount of gas used —and billed for—had we stayed with our old boiler systems,” Miller said. “What we saw was that the medical center’s total gas savings was roughly 50,000 MCF for the first year for a cost savings of over $433,312. The gas savings came from an improvement in the plant’s overall efficiency.”
According to Siemens Energy Engineering Manager Keith Kazan, Mount Clemens saw dramatic increases in energy efficiency. Plant efficiency rose from about 47.2 percent with the old boiler system to 84.2 percent with the steam generators.
“With the proper applications and requirements, it definitely makes sense to change over from a traditional boiler system to a steam generator, like those manufactured by Clayton Industries,” Kazan said. “I would absolutely make the same recommendations to other facilities, like these two hospitals.”
Steam Generation Saves Time, Energy, and Dollars
So, what makes a steam generator that much more energy efficient? First, these units heat up faster, within about 15 minutes as opposed to a conventional boiler, which takes between two and three hours. They can also be turned on and off when needed without the risk of damage to the system.
Hospitals are required to have back up generation, which when the plant is run with a conventional boiler, it is generally kept in hot mode so it comes on-line quickly, if need be. That means that even if the hospital is not currently using the back-up boiler, it is consuming energy, just in case it is needed.
According to Miller, because the steam generator starts so quickly, it can be kept turned off until needed. “With the steam generators, steam production is nearly instantaneous. It allows us the ability to not have a fire tube boiler on standby in case of an emergency. If we were to have an issue with our primary system, the operators are able to get the second system up to full steam in less than 15 minutes.”
In addition, hospitals have fluctuating, seasonal loads and under conventional boiler methods sometimes operate in low fire or low load for a considerable time—a very inefficient process. Clayton’s operating efficiency averages 85 percent, no matter what the load or firing rate. The generator’s design creates less heat loss and chemical loss. What’s more, the steam generators are explosion-proof, providing the highest level of safety in the boiler industry.
Miller said another major benefit using steam generation is minimal maintenance. He said as long as general maintenance procedures are followed, preventive maintenance is fractional, compared to that of traditional fire tube boilers. “Overall, the steam generators have been a valuable addition to the Mount Clemens Regional Medical Center in our mission to reduce energy consumption and costs,” Miller said.