For 30 Years, Schooner Prints Has Produced World-Class Wall Coverings Thanks To Clayton Steam Generator’s On-Demand, Safe, Consistent Dry Heat, And A History With No Industrial Accidents
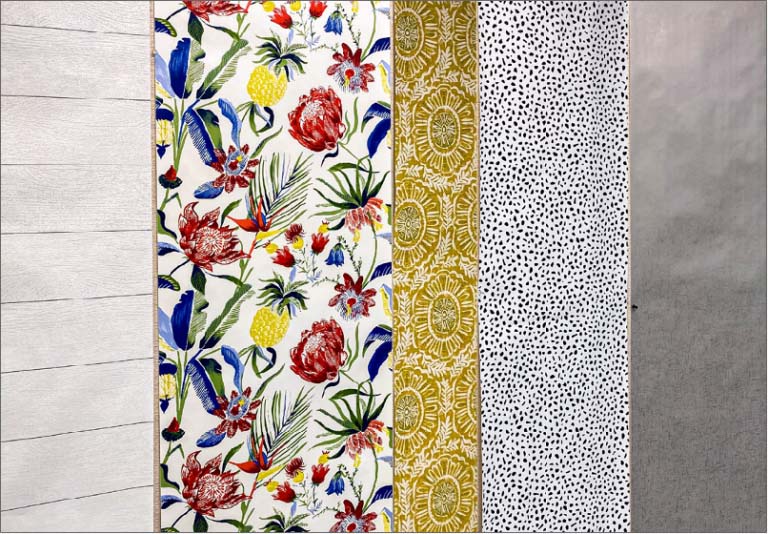
in over fifty countries.
Schooner Prints, Inc. has been a premiere force in the wallcovering industry for over thirty years with clients in over fifty countries. When Pat and Tim Bluett started Schooner Prints back in 1990 in Largo, Florida, they knew they needed Dry Steam. After asking suppliers for advice, Clayton was recommended as the go-to for Dry Steam. They were considering steam boilers and owner Pat Bluett, said they were told, “No, you need a steam generator and Clayton are the people to talk to.”
Will Brozowski, Clayton Senior Account Executive said, “Schooner needed high quality dry steam to create their premium wall coverings. The Schooner process entails running numerous custom batches during a shift. The Clayton Steam Generators can go from Hot Stand By (0 psi) to Full Steam Load 3,450 lbs/hr (100 psi) in 30 seconds. This represents significant time, and fuel savings.”
Pat went on to say, “That (consistent dry heat) is one of the reasons we’re one of the best wall covering producers in the world.”
Schooner is proudly family owned and operated. They’ve a dedicated green printing facility utilizing only the finest, non-toxic, water-based ink systems. They produce high quality Rotogravure printing on multiple presses with a wide range of printing widths utilizing specialty ink techniques using specialty metallic and textural puff inks.
They manufacture entire book collections and accompanying wallpaper stock printed, bound, packaged and prepared for direct global shipments. Upon demand, books are produced simultaneously while the wallcovering is packaged into bolts to specified sizes, allowing the wallcovering book collections and stock to be prepared for shipment anywhere in the world.
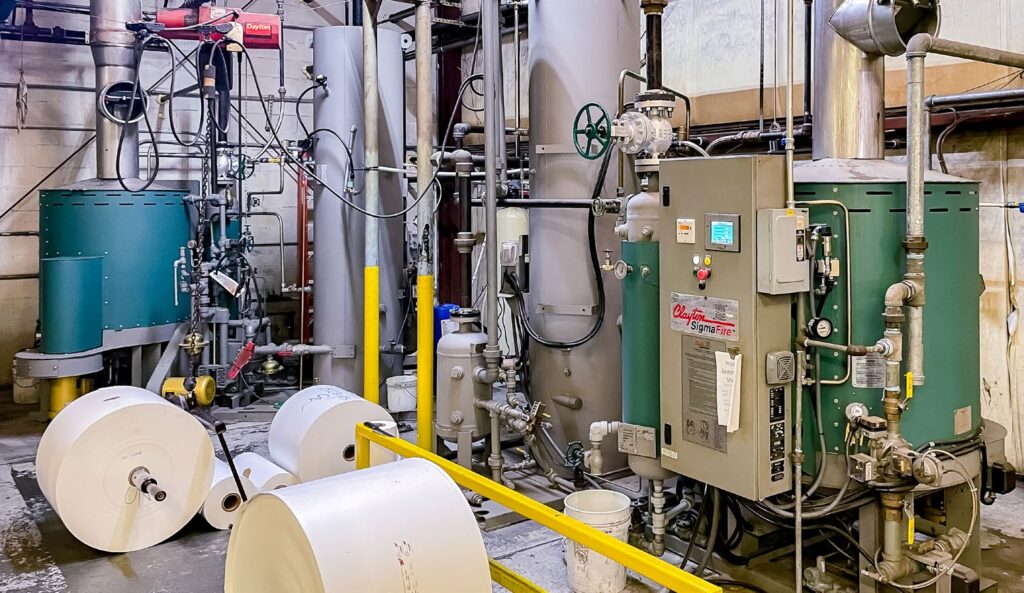
Clayton Innovative Steam Solutions Is A Key Player Helping Schooner Prints Deliver Their World Class Products
Schooner’s maintenance and opera- tions manager, Tim Bluett said, “In essence we run dry steam through what you’d think of as a radiator producing consistent heat. We need even, consistent, dry heat to dry our webs to make our wall coverings and the Clayton Steam Generators produce good quality dry steam”.
Will Brozowski added, “Schooner runs two shifts a day. When they leave at the end of the day, they shut the steam generators down. Every morning they can start cold and be ready to work in 10 minutes. A traditional boiler can take 60-90 minutes to start from cold. As I mentioned earlier, this represents significant fuel and time savings.”
“Shipping from California was expensive, and we were a more expensive solution upfront, but more cost efficient over the lifetime of the unit. Those savings in time and fuel add up over time.”
Pat continued, “We chose Clayton and their steam generators because they are safe, reliable, and efficient. And specifically, because they have a history of no industrial accidents.”
Will continued “Our products are guaranteed to NEVER have a steam explosion.”
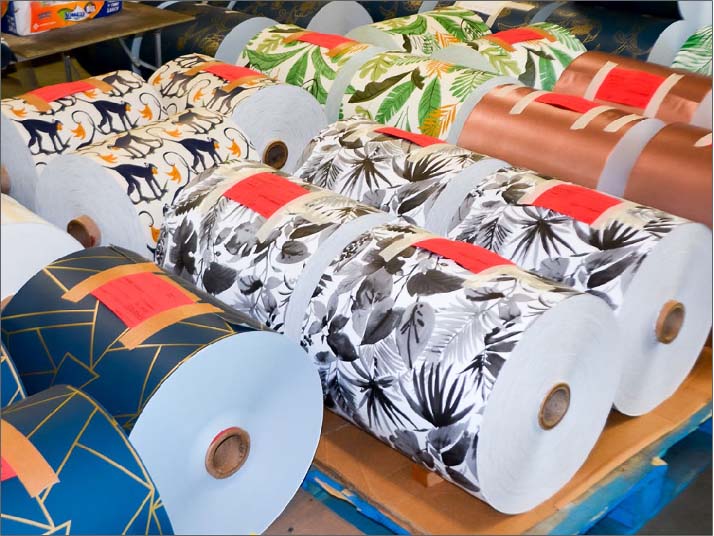
Tim continued, “Originally, we had two 60 BHP steam generators. After 28 years we decided to replace one with the 100 BHP model. We figured if the 60 went down we could run both presses with the big one. The original installation was seamless, and the replacement went even smoother. We thought, let’s be proactive, so, we replaced the other steam generator as well.”
When Will was asked why he thought Schooner chose Clayton this time around he said, “Schooner has been using Clayton products since their inception. The Schooner folks know our products. We trained their staff and they have worked with us day
in, day out for 30 years. And they know how to find us when they need us. We offer on call service, but I do not remember their having had an emergency in the 10 years I’ve been here. It’s this ease of operations and serviceability they value.”
“They (Schooner) are very detailed people. Their detailed attitude made the transition from the old unit to the new easy. We all knew what to expect and the new installation went off with no surprises.”
Will continued, “Clayton and Schooner are a team. We help them succeed and they help us succeed.”
Tim echoed Will’s assessment of Schooner’s relationship with Clayton, “I’m responsible for maintenance. I watched the Clayton people and learned. And whenever I haven’t known what to do, I’ve called, and their support people have walked me through what I needed to know. Other than a coil replacement, we’ve never been down for a day. They’ll fly a part in if needed.”
Will said: “To produce 30 years of world-class wall coverings, Schooner needed on-demand, safe, consistent dry heat and Clayton equipment enabled what was needed since day one.”
Using their unique counterflow design and controlled circulation system technology Clayton steam generators bring forced and circu- lating feed water to the combustion gases and leads to optimum heat transfer allowing for rapid start-up. That accounts for the labor, time and fuel savings.
But Clayton’s contribution to Schooner’s printing quality is the dry steam. Clayton’s fixed vane steam separator produces 99.5% High Quality Dry Steam with a consistent absence of water or any other form of liquid. This is the driest saturated steam available in the industry today.
In addition, Clayton’s steam generator water treatment chemicals and coil guard technology maintain the highest quality steam while protect- ing the machinery. The technology also ensures longer life for the equipment and less downtime for maintenance and repairs representing more savings and greater productivity.