Clayton Steam Boiler Heat Exchanger
Home > Clayton Steam Boiler Heat Exchanger
Clayton Steam Boiler Heat Exchanger
A counterflow monotube Heat Exchanger is at the heart of Clayton’s design. Heat is transferred from the combustion gases to the feedwater via this unique spiral-wound coil. The coil is designed to control the water flow inside the tubes and the air flow over the tubes. To maximize heat transfer, the coil’s design also allows for thermal expansion and contraction without thermal stress. The same basic design is used for both Clayton’s fired and unfired commercial steam generators (heat recovery). Additional economizer sections can be easily added to improve overall system efficiency.
The SigmaFire heating coil consists of two sections — the main generating section and a lower water wall section that form the combustion chamber. E-Series heating coils consist of three sections — the main generating section, an upper water wall section and a lower water wall section that form the combustion chamber.
The tube material is smooth ASME SA-178 carbon steel. Clayton Industries forms sections by welding layers (typically referred to as “pancakes” ) of spiral-wound coils in a continuous flow path. Spacing between the tube surfaces is maintained by welded clips that assure proper air flow and eliminate dead spots in the exhaust gas flow path.
The upper water wall section is a single wrap around the outer top portion of the generating section. The primary purpose of this section is to provide thermal insulation of the internal hot gases from the outer shell. The main generating section is typically comprised of 16 spirally wound layers. The coil diameter increases through the steam boiler heat exchanger to allow for expansion that occurs as the feedwater vaporizes. The layers of spiral-wound coils are staggered to provide disruptive combustion gas flow and proper velocity for good heat transfer. Lower water wall sections are a single outer wrap of coil around the main combustion chamber that provides thermal insulation and additional heat transfer surface area.
The flow of water in the coil counters the flow of hot gases. This counterflow design helps provide optimum heat transfer and is one of the factors that lead to the high efficiency of the Clayton fired and unfired steam generation systems. Pumping feedwater at a rate of 125%-133% of the steam demand helps ensure that there is liquid in all sections of the coil at all times to eliminate steam blanketing. This helps provide good heat transfer and protects the coils from overheating that can occur in superheat conditions.
The entire coil is encased in a mild steel inner jacket and insulated from the outer shell. Cooling air passes between the inner steel jacket and the outer carbon steel shell. Air is either provided by the combustion air blower with standard burners or by means of an external cooling air fan. This arrangement maintains a skin temperature to a maximum of 150°F.
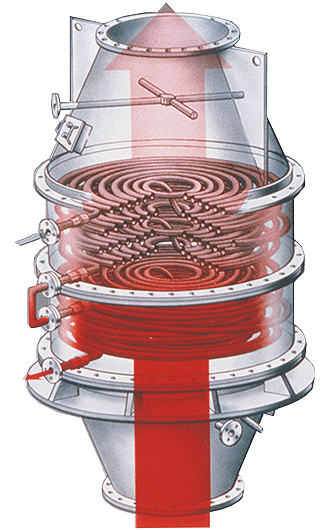
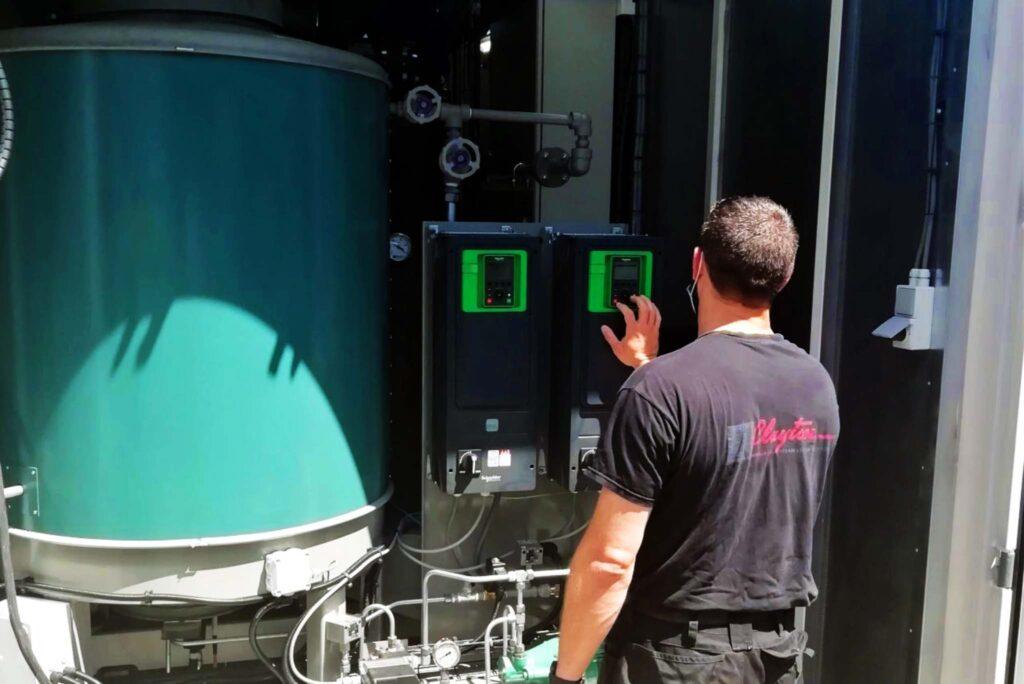
With 24/7 availability and extensive coverage throughout the United States and beyond, our skilled professionals are equipped to keep your steam generator operating at peak performance.
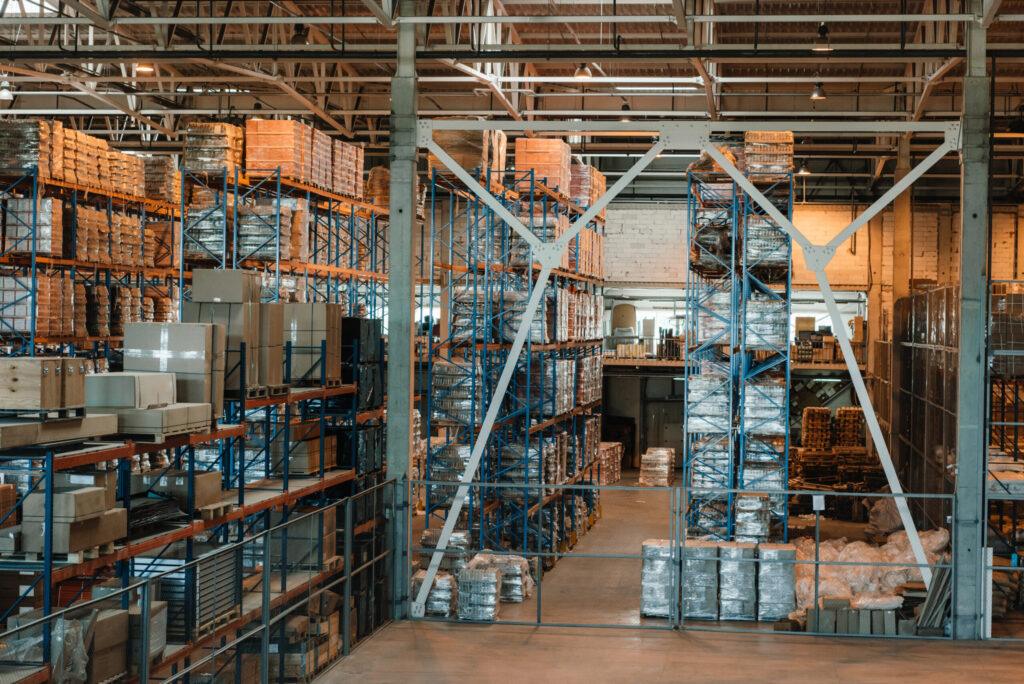
Looking for replacement parts? Clayton has you covered. Between our parts warehouses, manufacturing plants, and service centers located across the globe, Clayton can ensure a quick response to your steam generator needs.
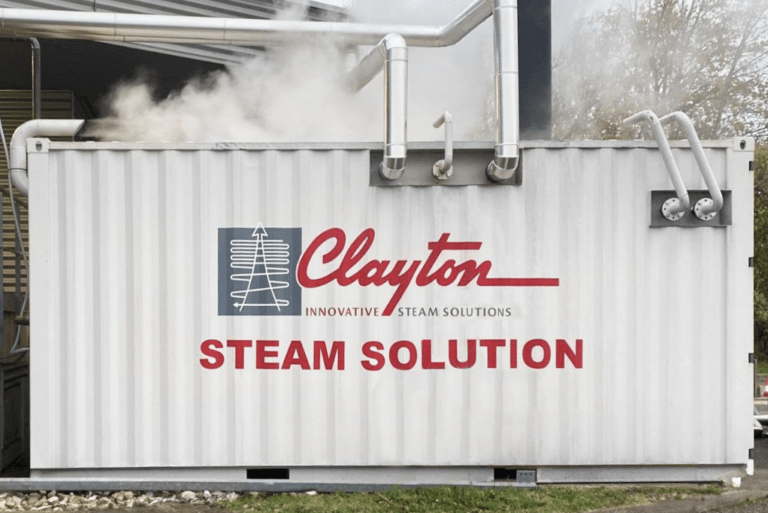
Are you looking for a temporary solution? Or has a shutdown forced you into an emergency situation? Regardless of your situation, Clayton offers a range of rental solutions that will keep you up and running, complete with all of the auxiliary systems required to bring your facility back online.
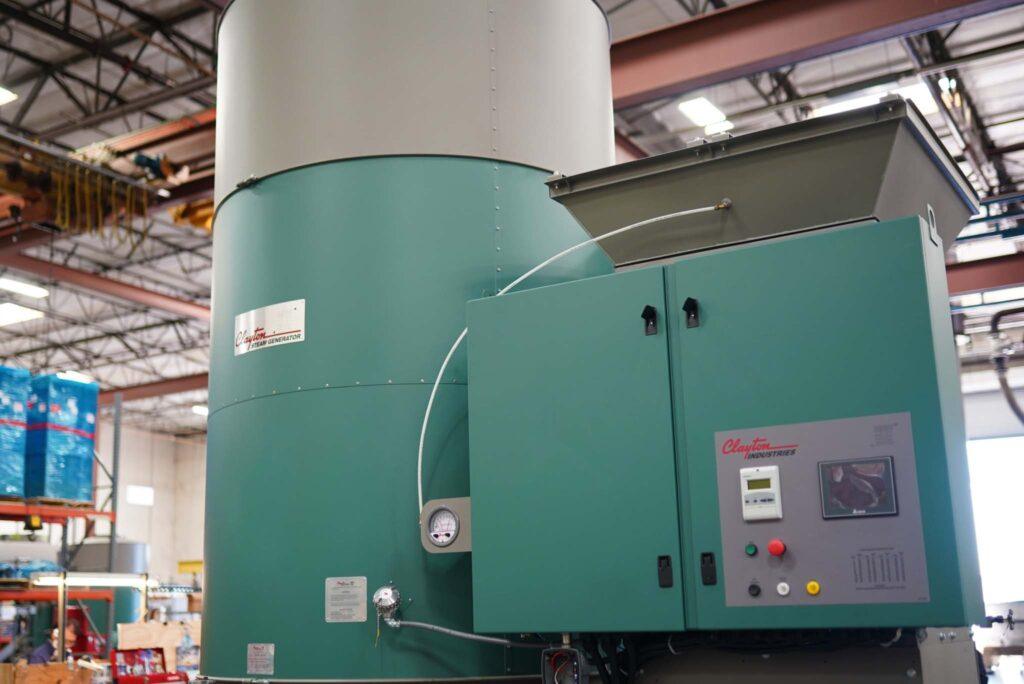
In addition to our production facilities around the world, Clayton also offers a refurbishment program, providing a quality source of rebuilt units available for sale.
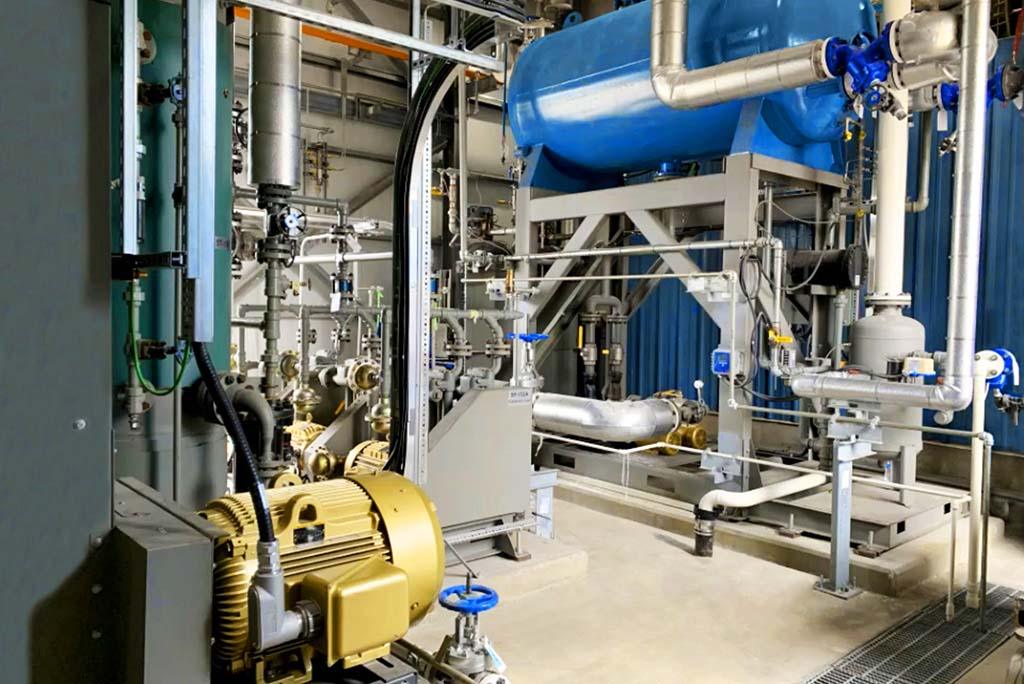
Why wait for an emergency shutdown to schedule maintenance? In addition to our regular and emergency services, Clayton offers extensive Preventive Maintenance programs, tailored to your needs, to ensure your steam generator continues to perform at optimal efficiency.
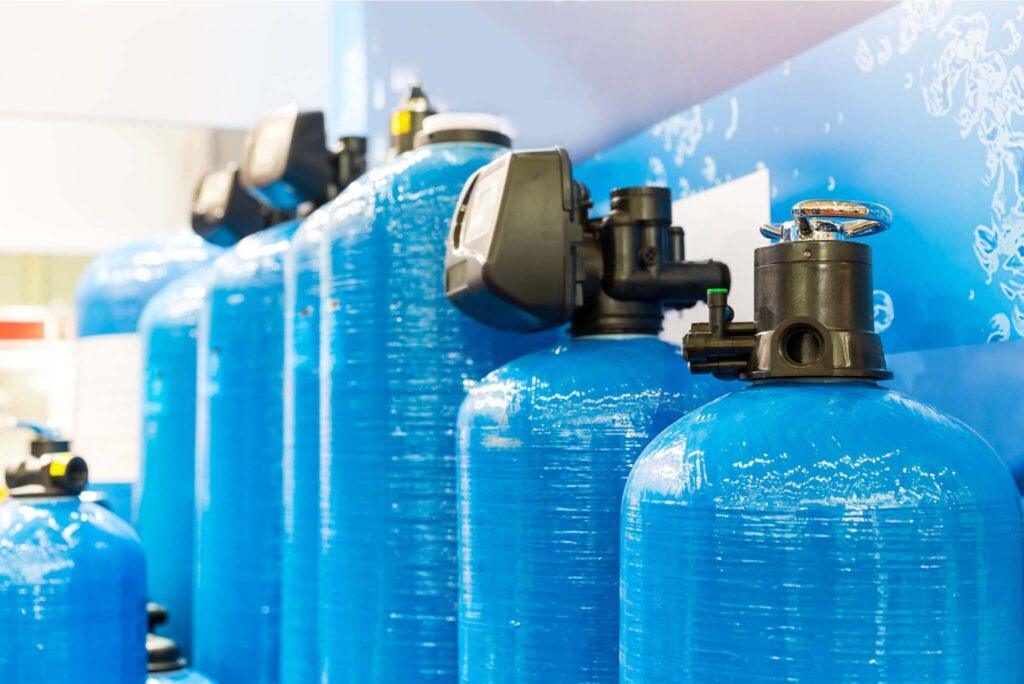
Feedwater quality is absolutely critical to boiler operation. Keep your system running smoothly with support from Clayton’s Chemical Water Treatment division, which allows you to take full advantage of your steam generation system.
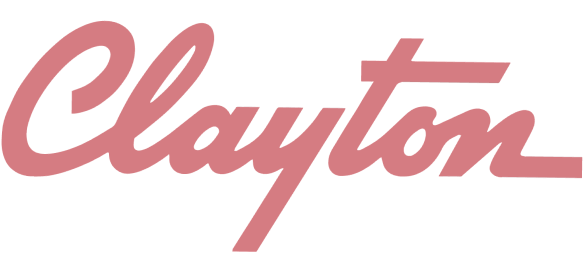
Contact a Clayton Representative









Resources
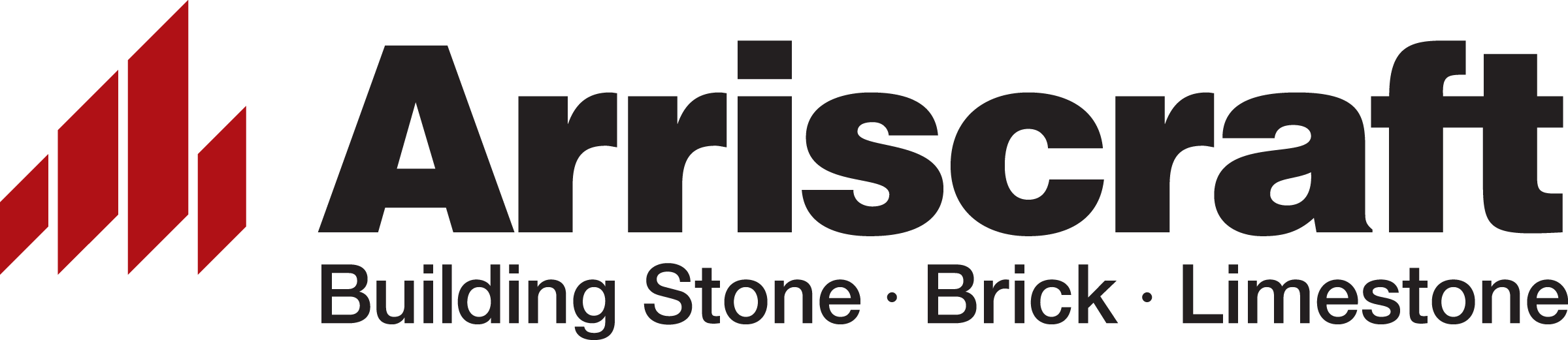

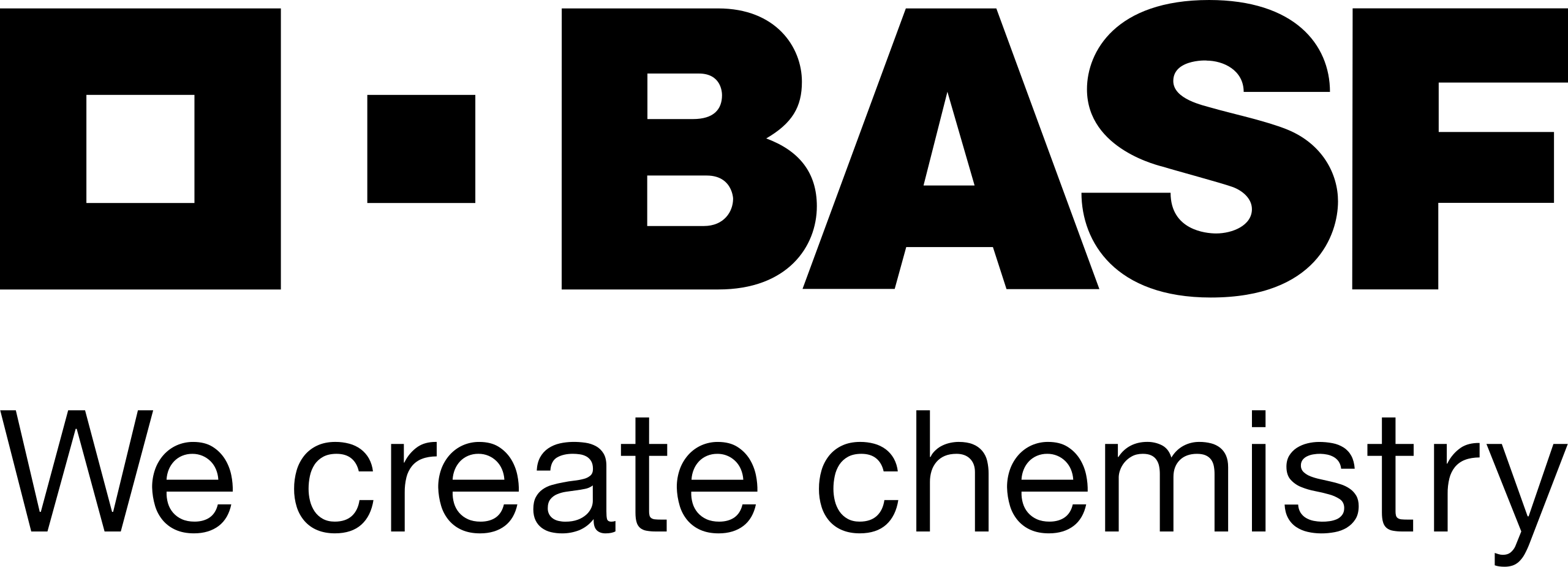
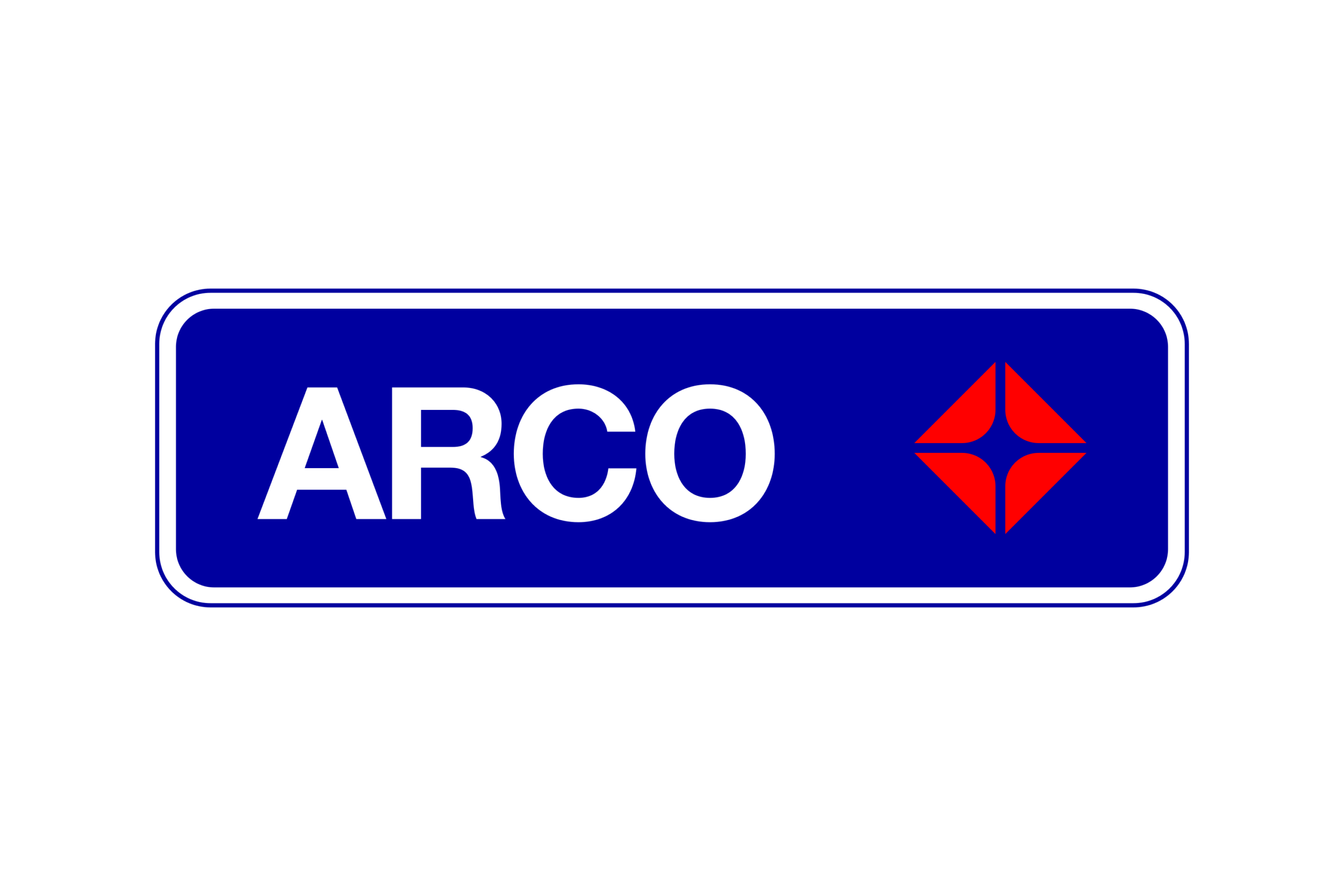
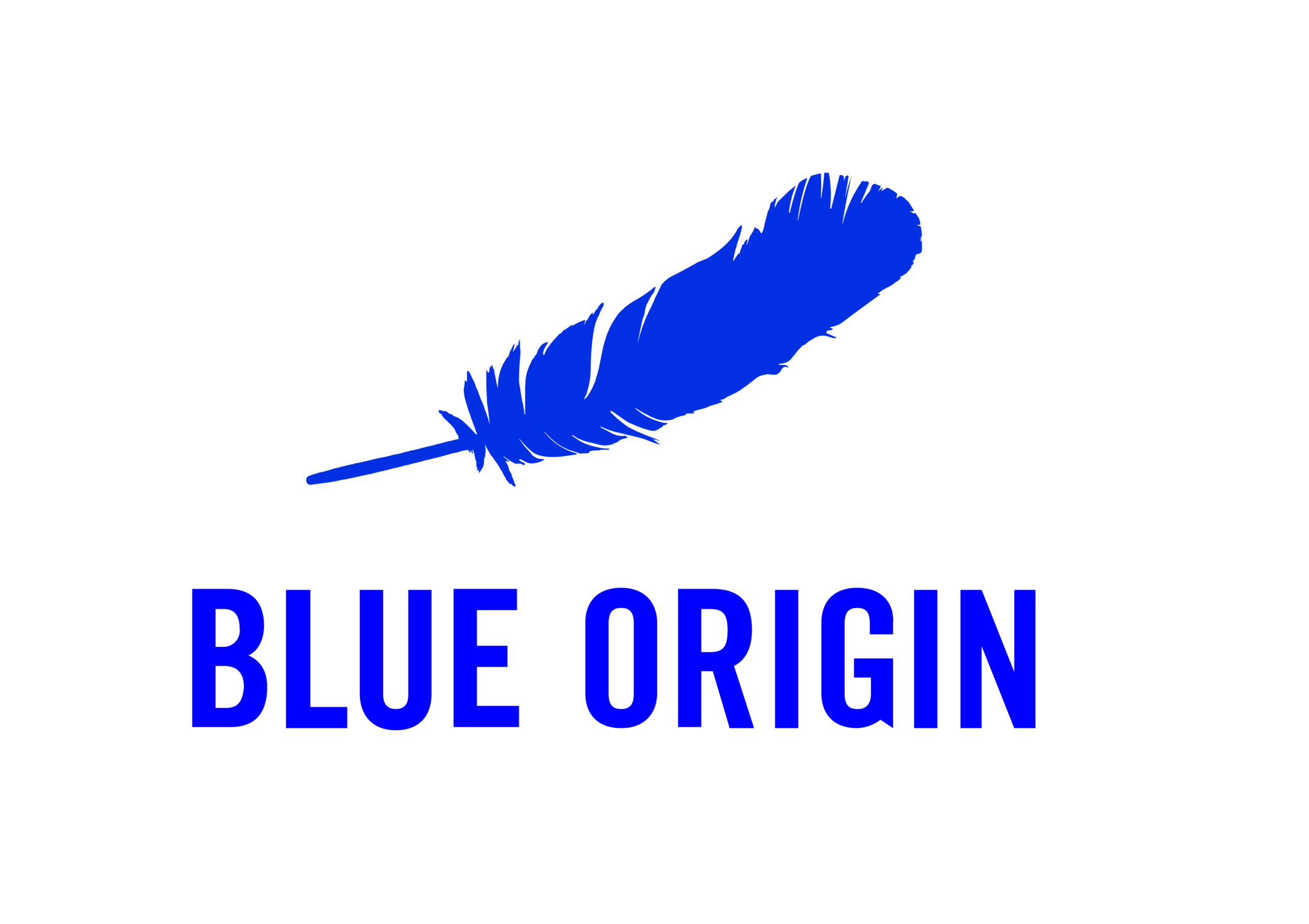
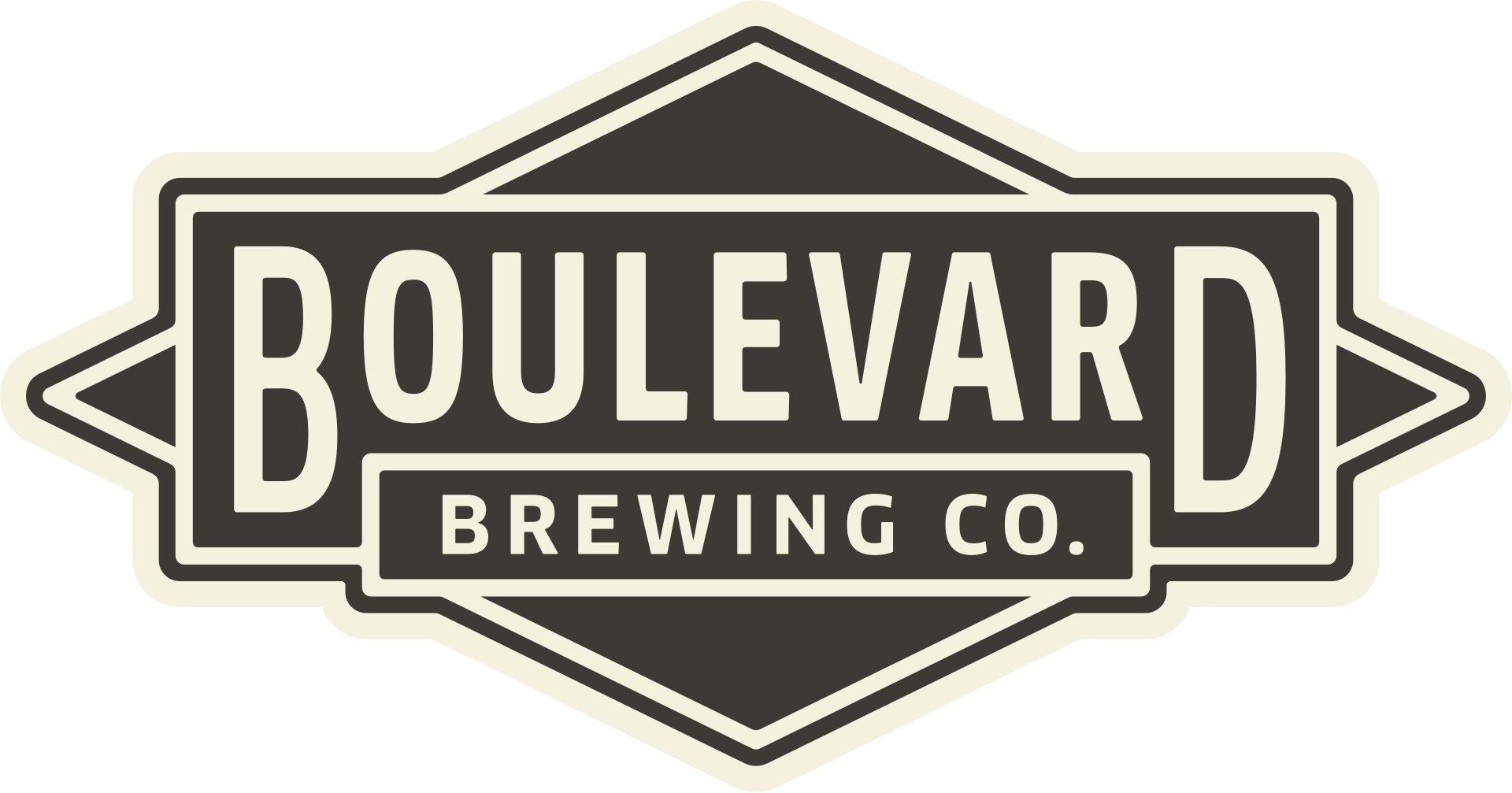
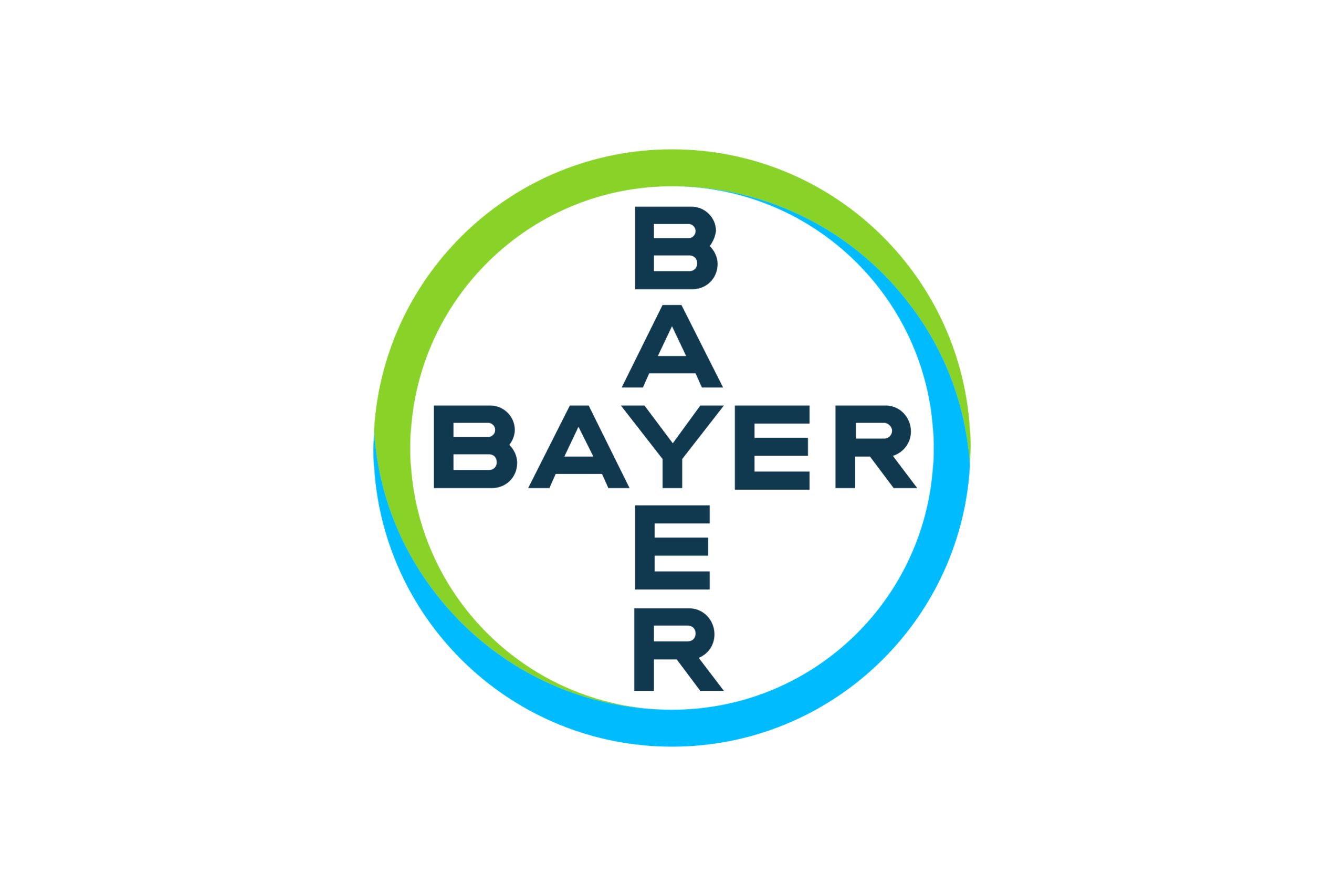
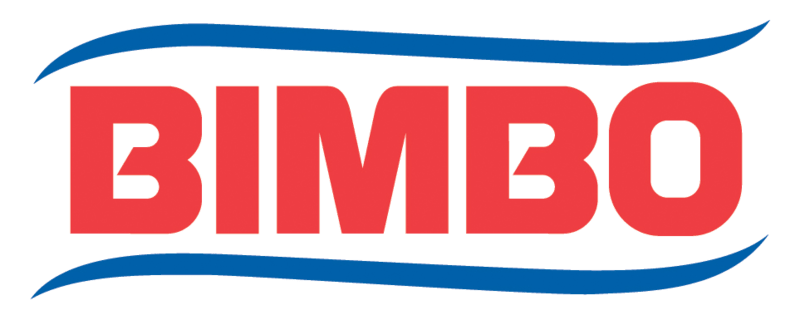
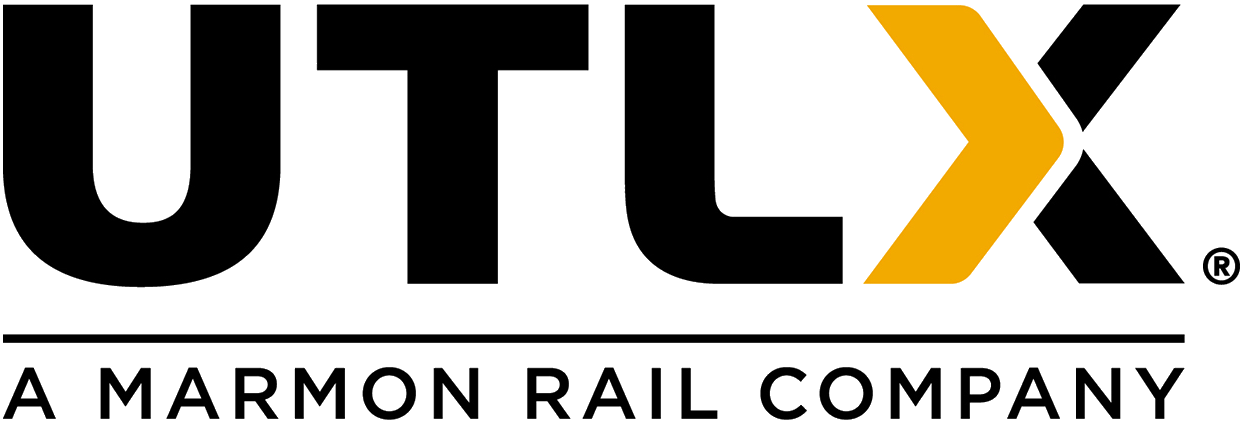
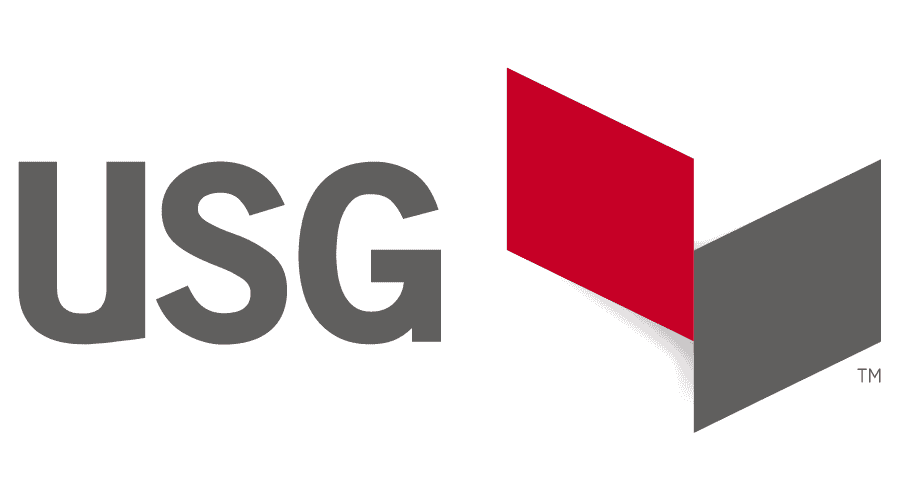
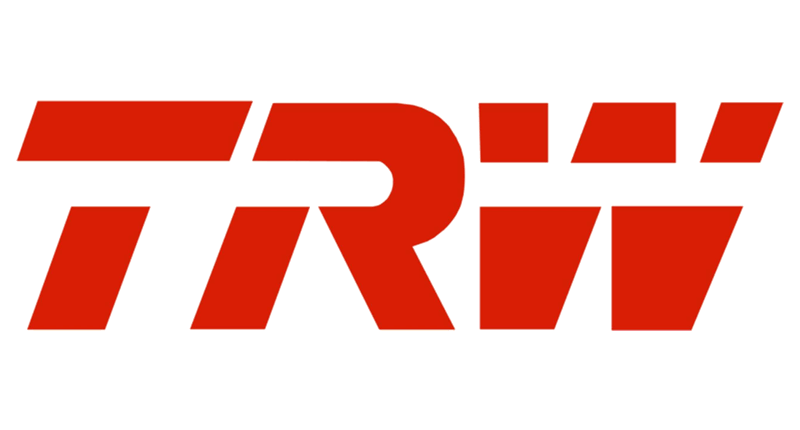
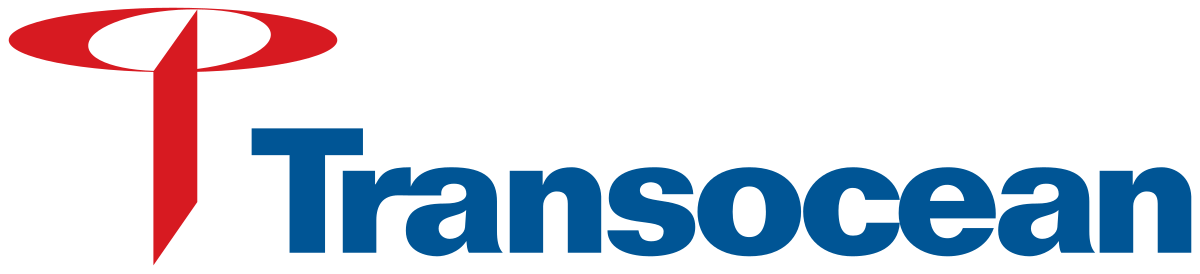

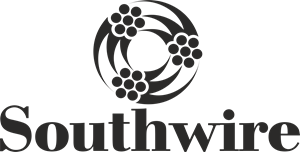
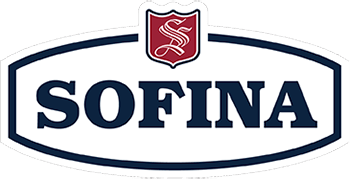
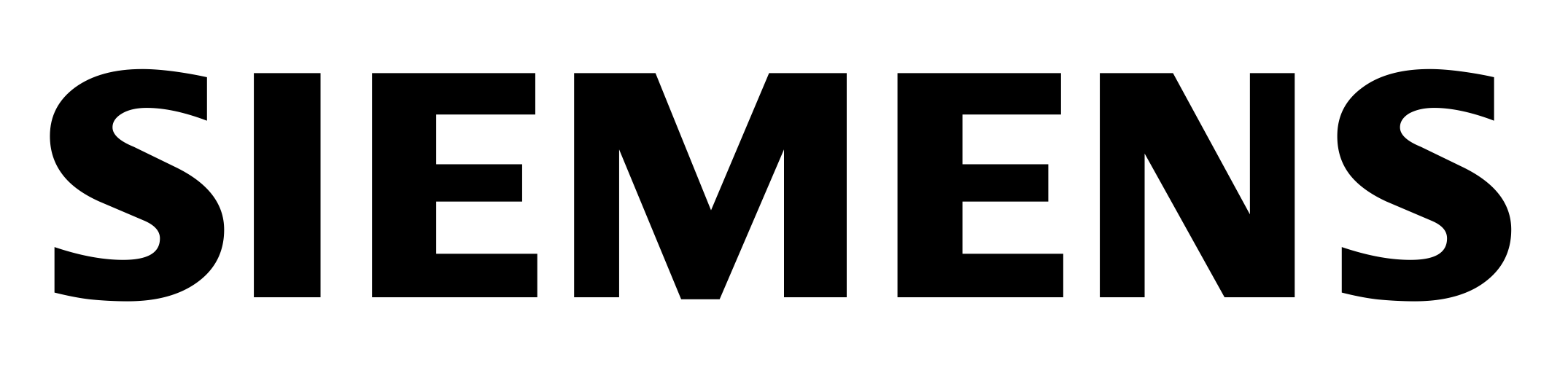
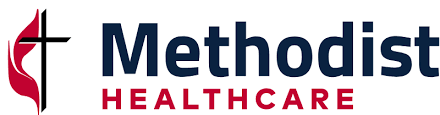
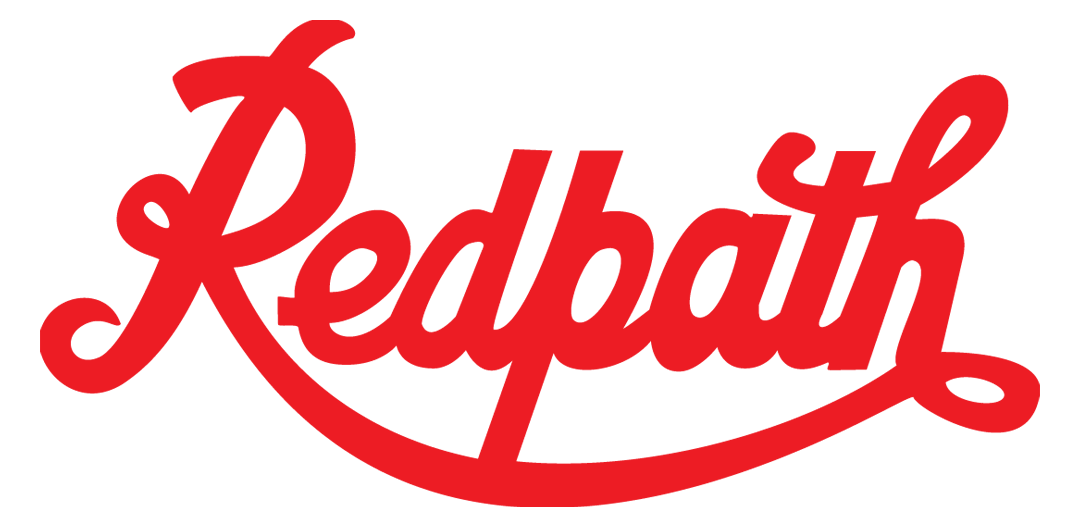
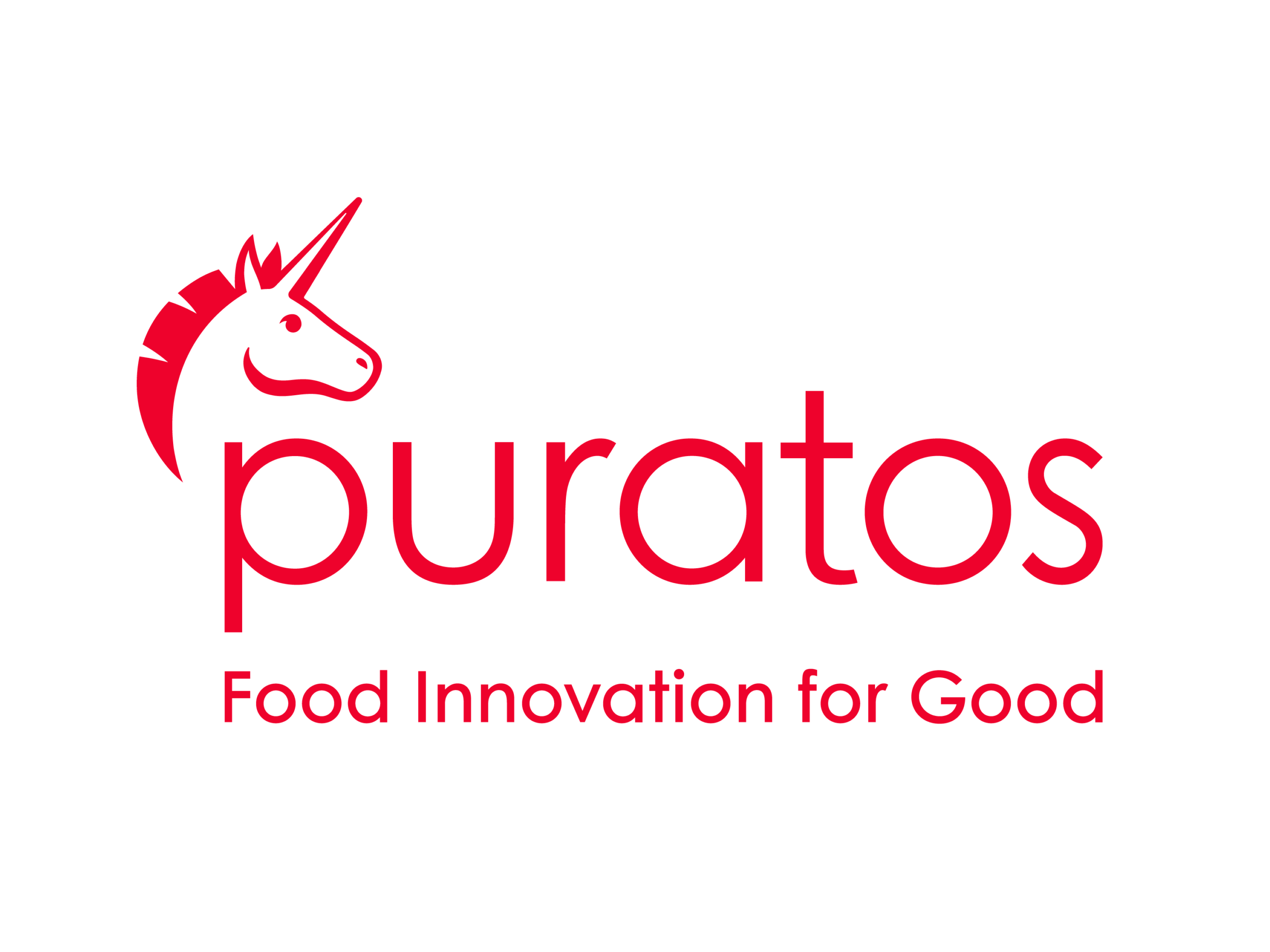
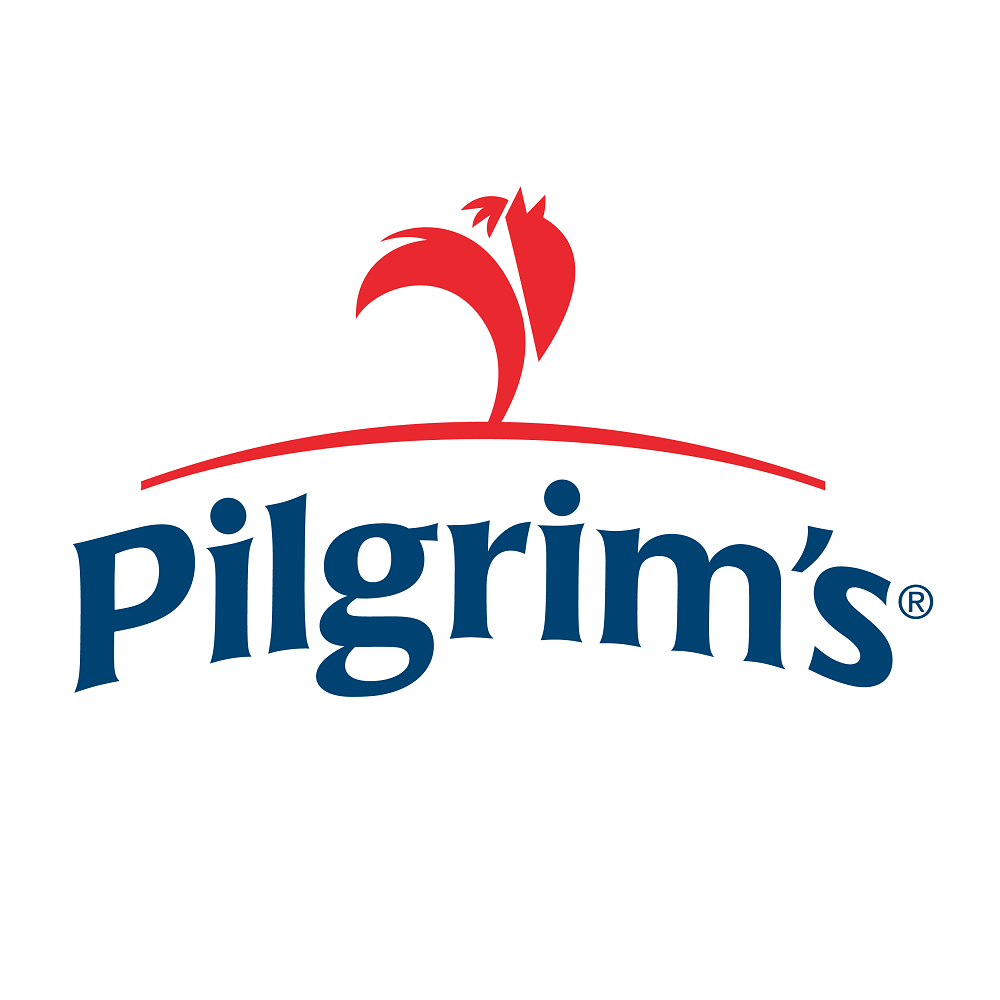
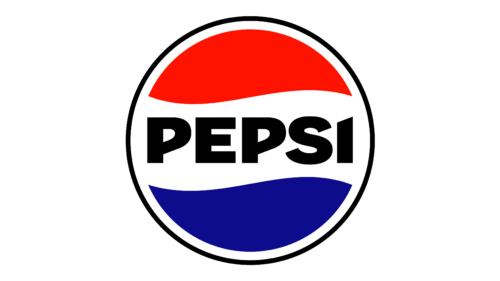
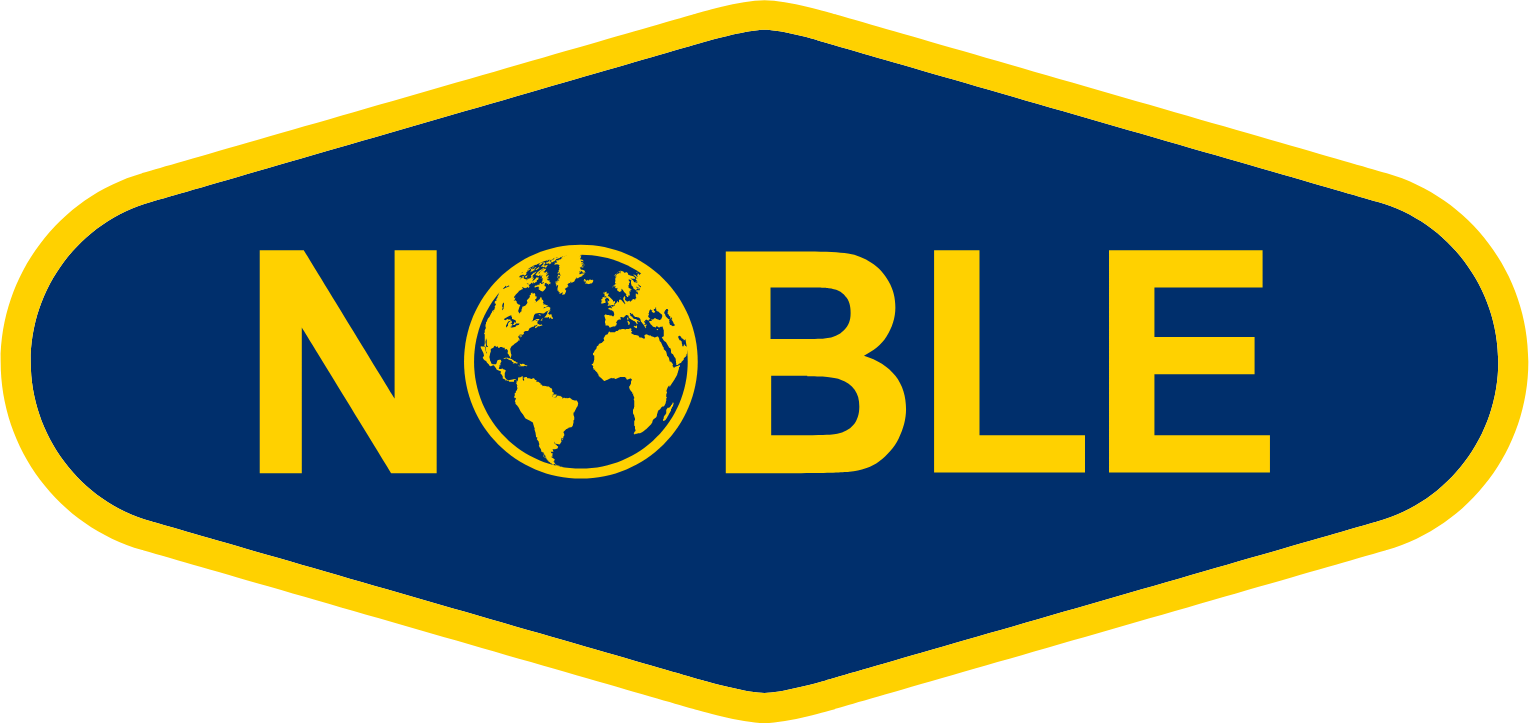
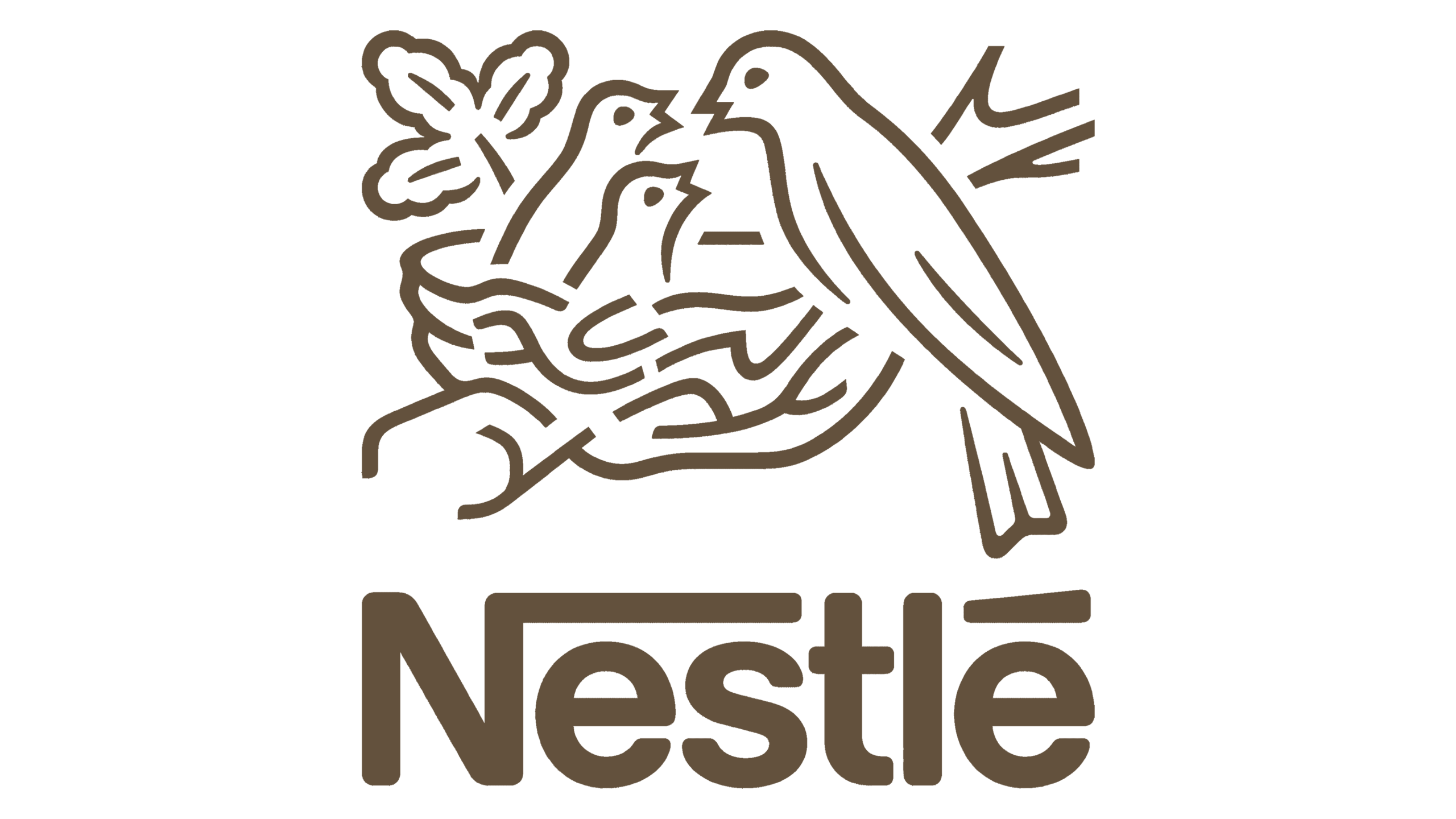
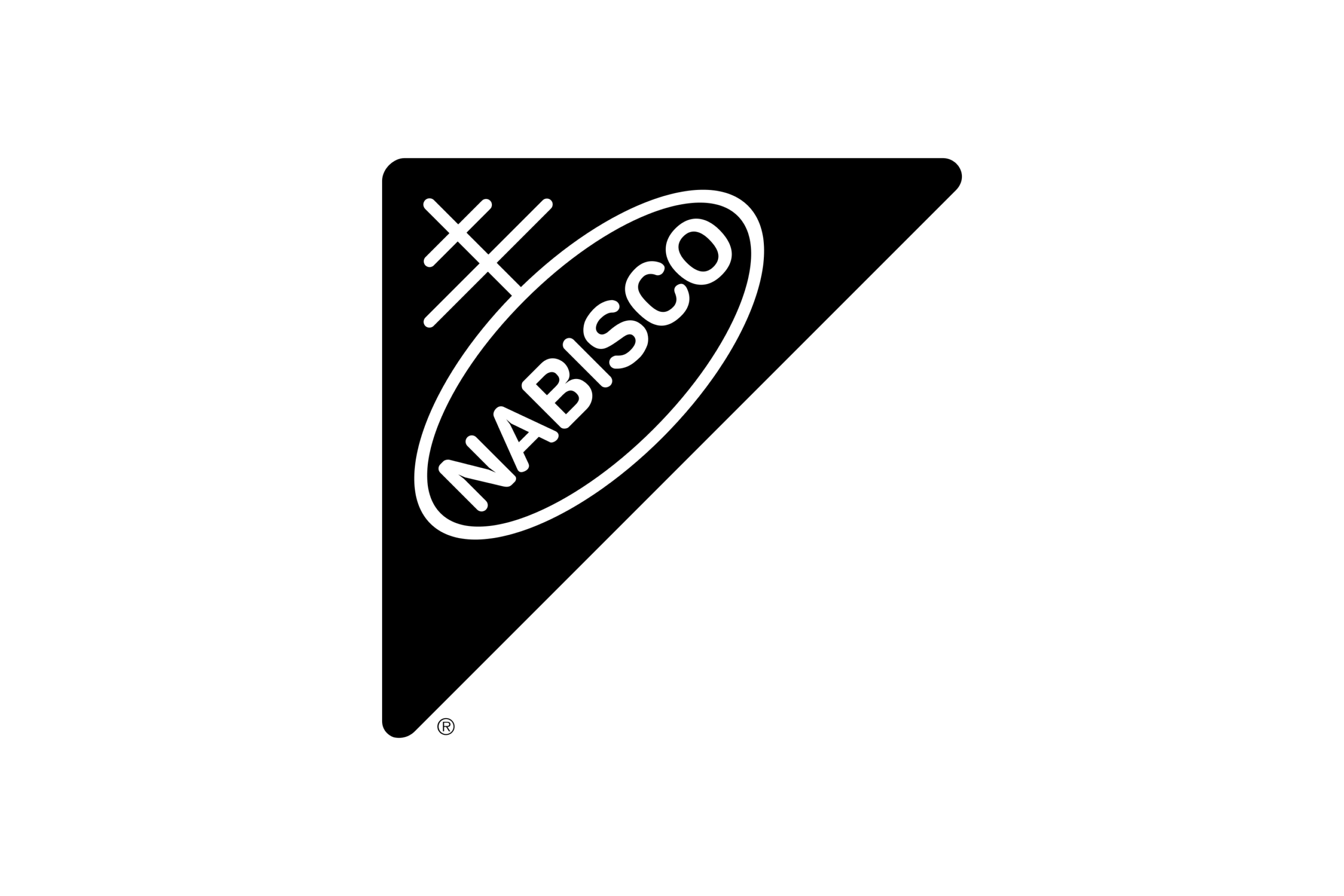
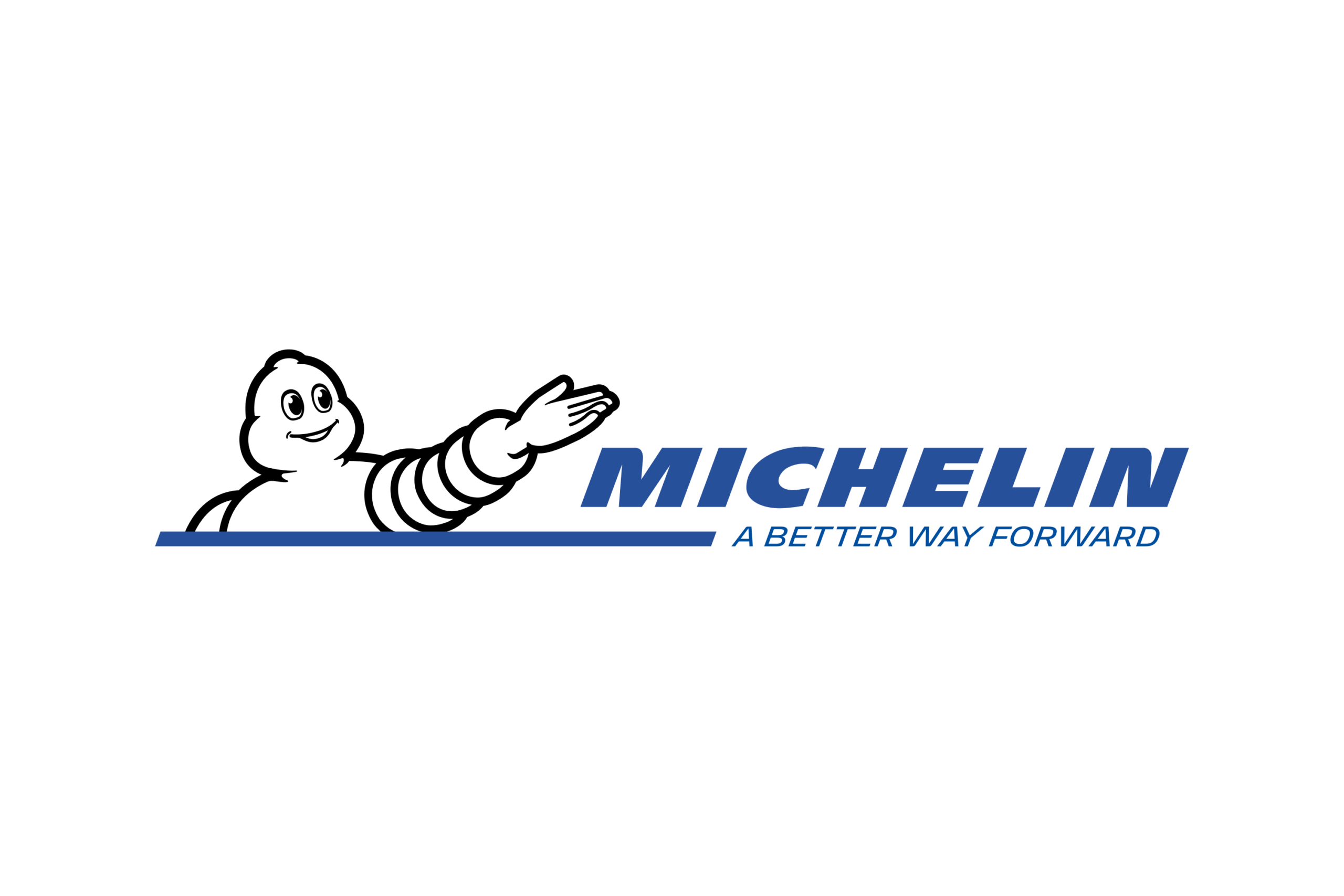
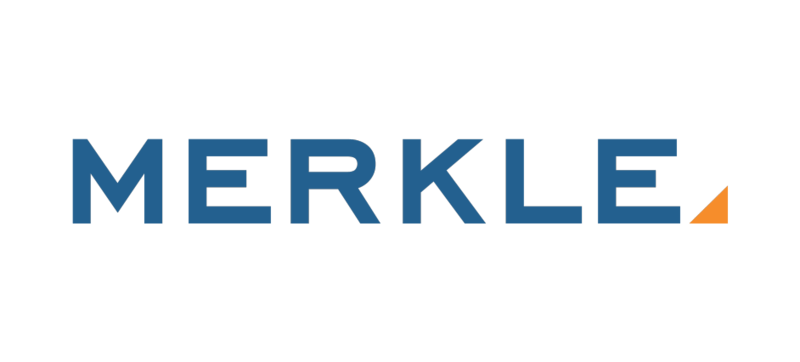

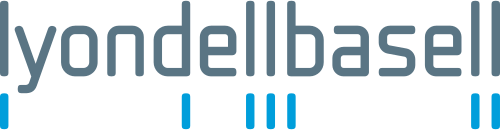
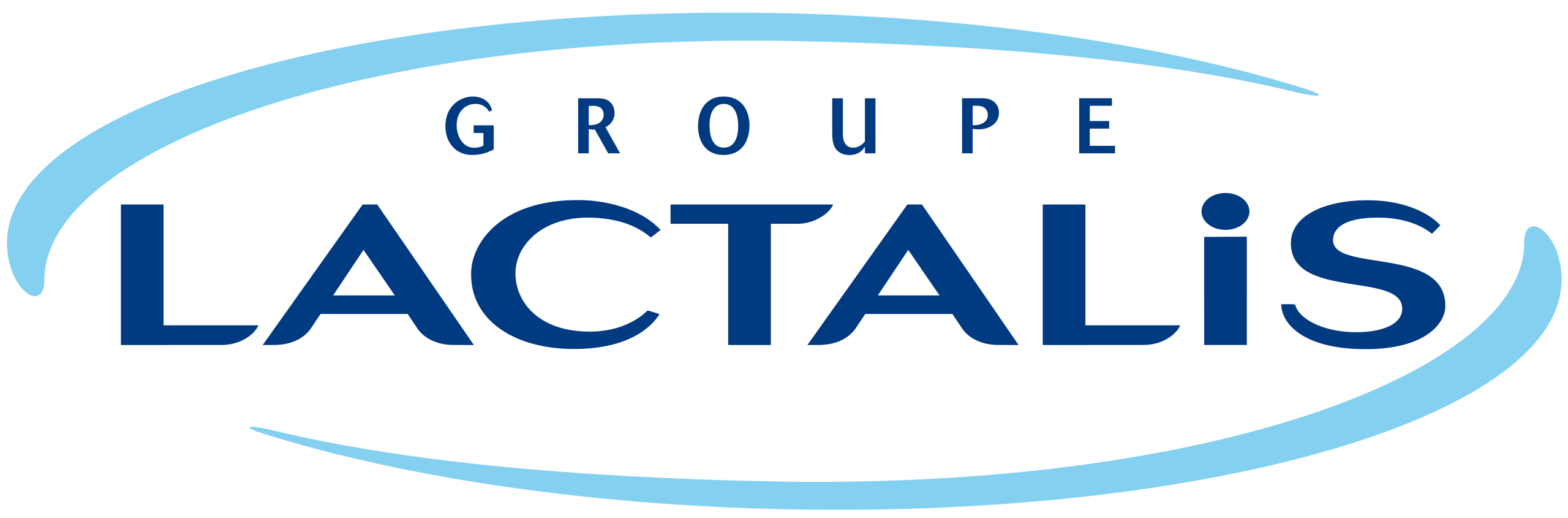
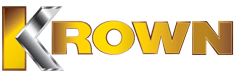
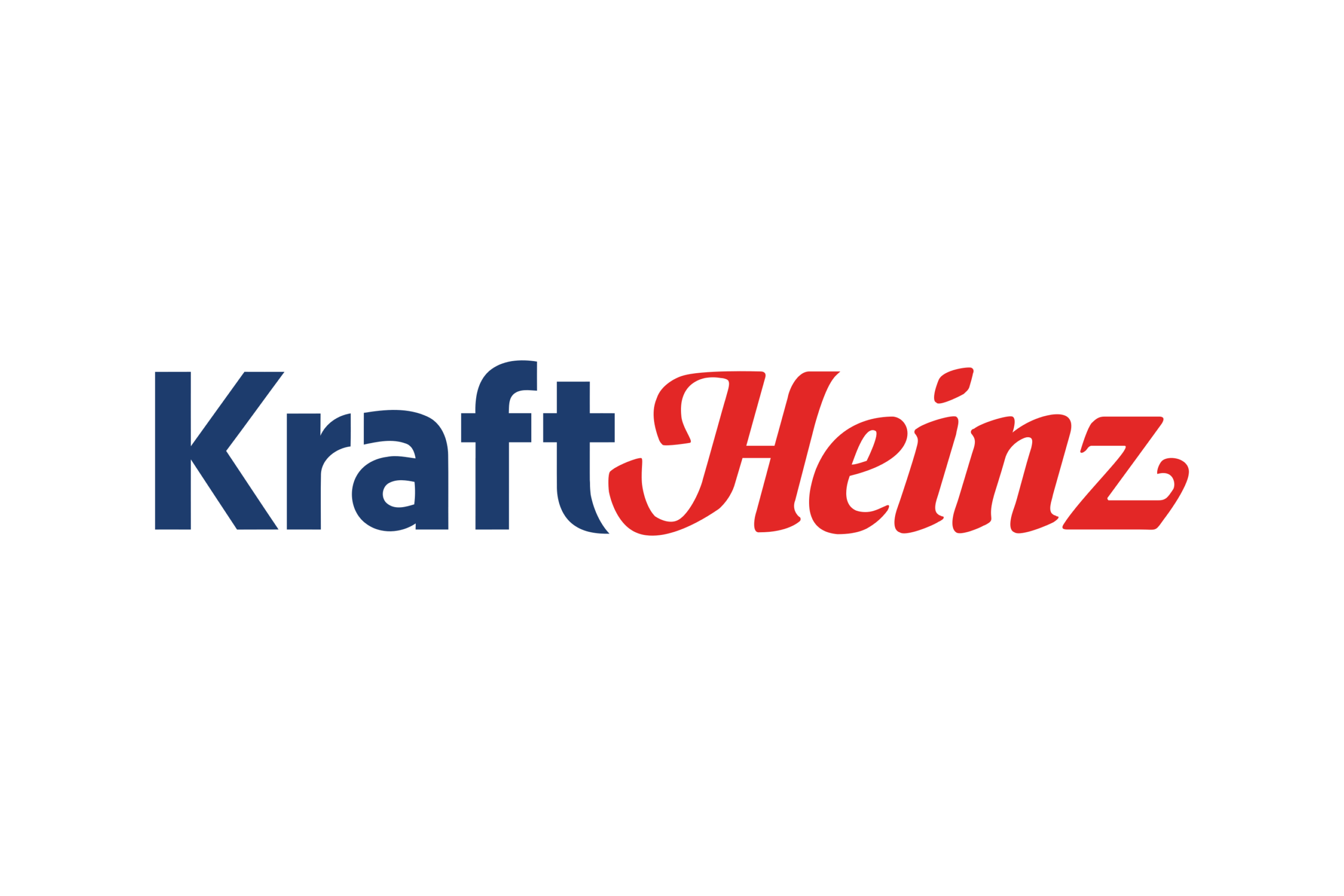
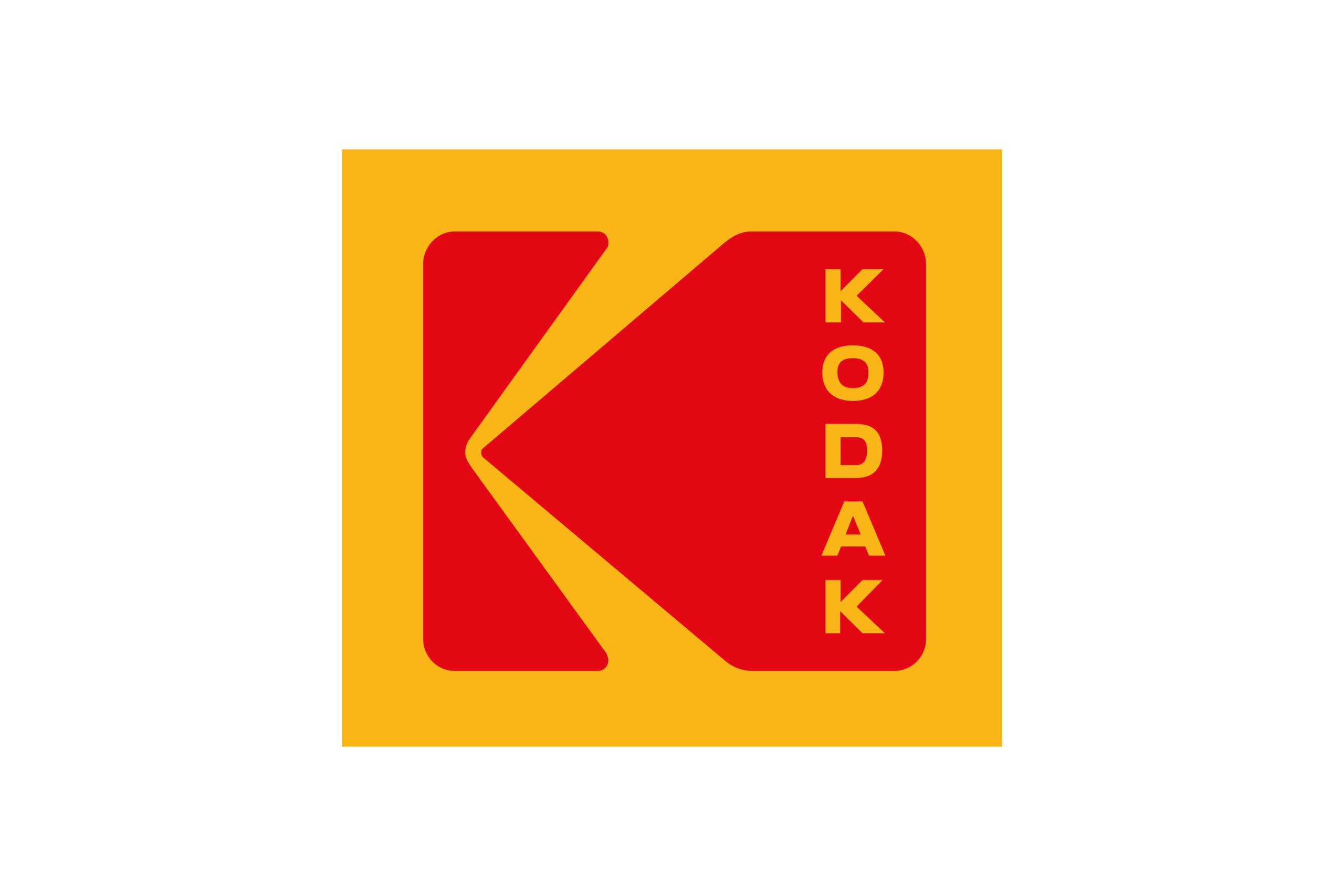
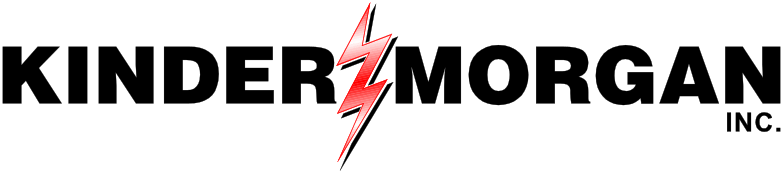
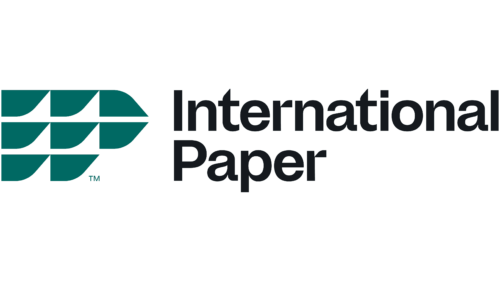
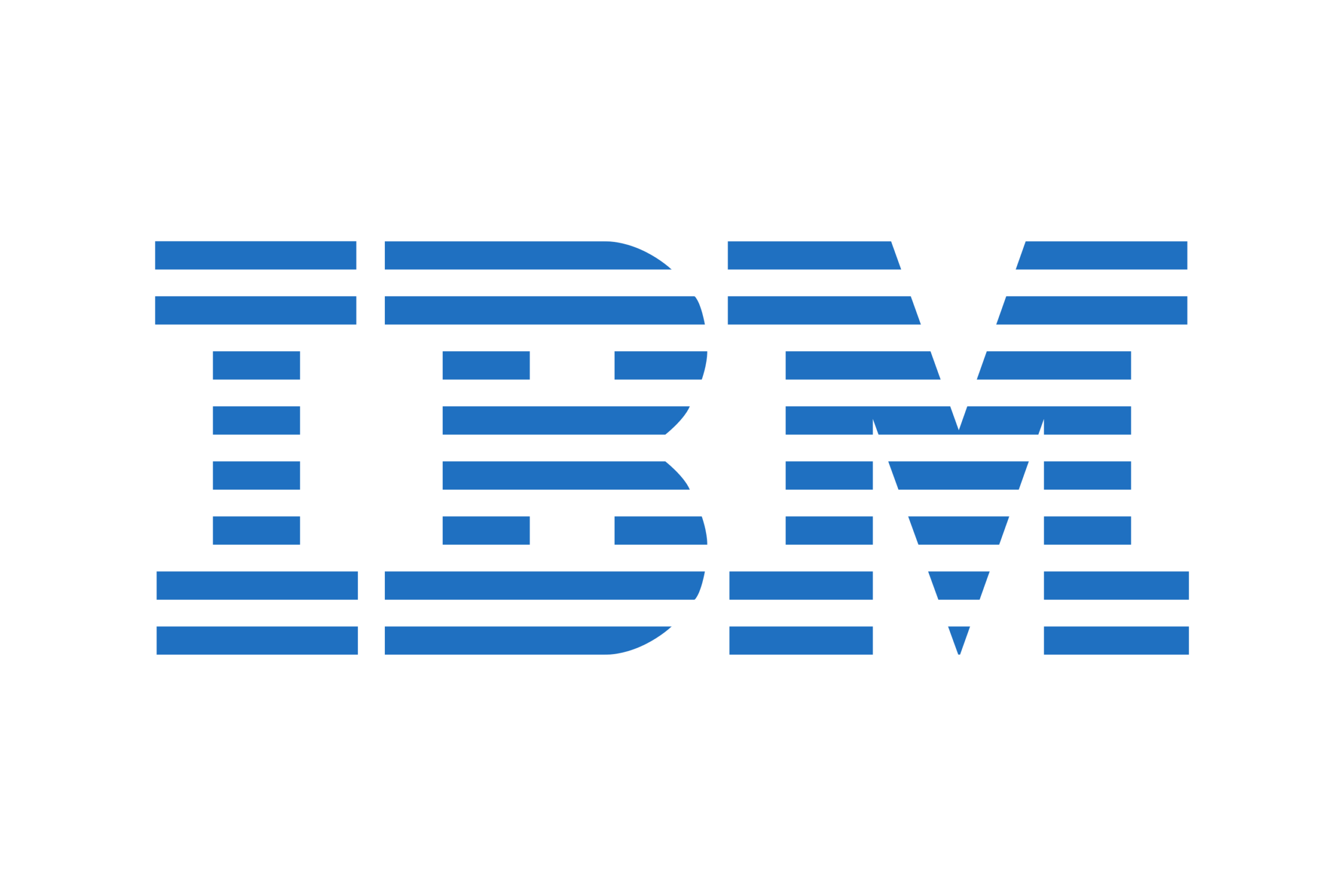

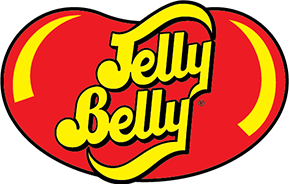
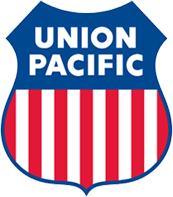