New Steam Generator and Semi-Closed Receiver Saves Fuel
Headquartered in Cicero, Illinois, LBP Manufacturing is a multi-plant manufacturer of innovative paper and corrugated food service and catering supply products. In addition to manufacturing, its services include design consultation and customized product development.
LBP’s unique and patented products have been highly successful in the industries that they serve. These products include the Coffee Clutch™ corrugated hot cup sleeves, the Beverage on the Move™ insulated bulk beverage carrier, corrugated catering trays, and disposable Soup-N-Serve™, hot and cold food transport containers.
Due to the rapid growth of their corrugated product lines, LBP made the decision in 2007 to manufacture single-face corrugated board internally.
Sam Valdes, Plant Engineer for LBP, made the decision to purchase Clayton Industries steam generating equipment to support a new corrugating line and starch mixing station. Sam had first-hand experience with Clayton Steam Generators at another specialty packaging product manufacturer. His decision to purchase Clayton equipment was based on reliability, fuel efficiency, ease of operation, and a small footprint.
A complete 100 BHP Clayton steam system was installed in LBP’s new Chicago manufacturing facility in the first quarter of 2008. This system included a steam generator, feedwater components, and a semi-closed receiver tank to receive high temperature, high pressure condensate return for reuse, thus conserving fuel, water and water treatment chemicals.
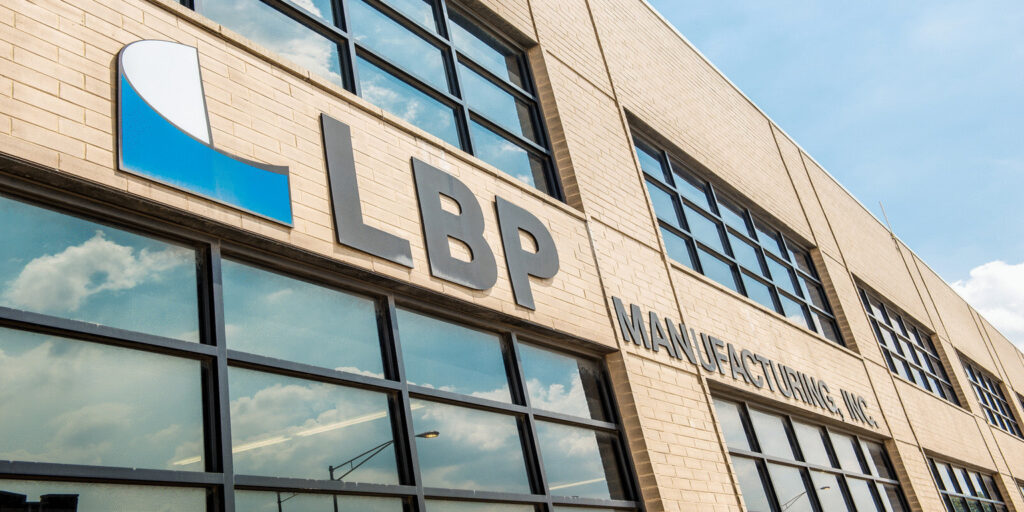
The Semi-Closed Receiver Feedwater System that LBP incorporated into their steam generating plant is designed to operate with a high degree of reliability and offers well defined economic benefits. The most important savings are in fuel consumption. The related fuel cost savings of an SCR system vs. a traditional open system will in many cases exceed 25% under similar operating conditions. Elimination of flash steam losses reduces the quantity of make-up water for the steam system resulting in reduced water consumption and feedwater chemical treatment, thus providing additional cost savings. Additionally, total solids build up is minimized and the frequency of manual or automatic blowdown cycles are reduced. A Clayton Steam Generator operating in conjunction with a Semi-Closed Receiver system is one of the most efficient steam supply systems available in the market today.