In terms of production technology, great importance is placed on the regional and direct purchase of hops and barley or malt – and with cooperation of local service companies and suppliers. According to Director Dr. Cem Schwarz-Thormann, the company has set itself the goal to strengthen the economy around Leipzig in this way.
Since the products bear distinctive names such as “Stolzer Hahn”, “Freche Ziege” and “Bunter Hund”, it is the express intention to strengthen aspects such as close connection to home and nature. “Quality has its origin; ours in this region also suits the flair of rural life,” explains Schwarz-Thormann.
After the fall of communism, the first generation of the family business took over the Malzfabrik in Landsberg from 1871, which was threatened with extinction. In 1996 the second generation of the family founded the brewery and connected it to the Malzfabrik.
Since its foundation, Landsberger used a horizontal steam generator to provide process steam. Operation of this could no longer be permanently maintained after more than 20 years. When the situation arose that the heating coil had to be changed again, it was no longer possible to postpone the new acquisition of a complete steam generation plant
In 2017, the Clayton Steam Master steam generator series from aroused the interest of the management for the first time at the BRAU trade fair. There they were introduced to the advantages of a vertical steam generator. In the course of an operational restructuring measure and in view of the requirements for higher steam volumes, the Landsberger Brewery decided in 2018 to use two CSM 30 Steam Masters. “Our objective was to produce steam at significantly lower costs and at the same time achieve greater operational reliability thanks to the double design,” says Schwarz-Thormann.
In addition to the safety aspect of redundancy, the brewery also focused on the individual load profile with regard to fluctuating steam requirements. With the parallel operation of the brewhouse and bottle filling both departments require a total output of both gas-fired steam generators of 95 %. The capacity utilization in barrel filling is limited to only 25 % with only one of the two Steam Masters.
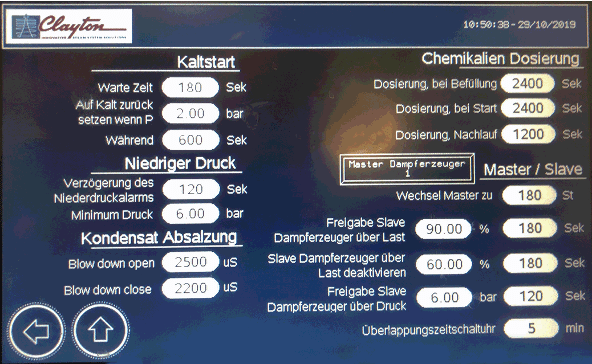
Display showing master-slave operation of both Clayton Steam Masters |
From the outset, we needed two boilers that had could easily deliver 100 kg or 850 – 900 kg of steam per hour alternatively, while working economically.
Having defined our base and maximum load requirement in advance, we knew which Steam Master solution was right for us, without the need for the boilers to be on and off continuously during normal operation. A further advantage of installing two steam generators with 450 kg/h steam output each instead of one steam generator with 900 kg/h output is the significantly lower administrative effort for approvals and the fact that the TÜV requirement is not longer required.“
The advantages of the “Steam-on-Demand” technology of both boilers have paid off economically. “Compared to the 1.5t predecessor model, we save at least 30 % of energy due to the intelligent modulation technology, the higher degree of efficiency and the corresponding reaction speed with fluctuating load requirements. The ideal solution